Introduction to Oil and Gas Inspections
In the intricate and high-stakes world of the oil and gas industry, meticulous inspections play a pivotal role in ensuring the safety, efficiency, and compliance of operations.
The oil and gas sector is a complex ecosystem, where even the slightest oversight or negligence can have far-reaching consequences. Rigorous inspections are the cornerstone of proactive risk management, enabling us to identify potential hazards, address vulnerabilities, and implement preventive measures before they escalate into catastrophic incidents.
Moreover, inspections are not merely a matter of regulatory compliance; they are a testament to our unwavering commitment to excellence and our dedication to upholding the highest standards of operational integrity. By prioritizing inspections, we demonstrate our respect for the trust placed in us by stakeholders, communities, and the broader public.
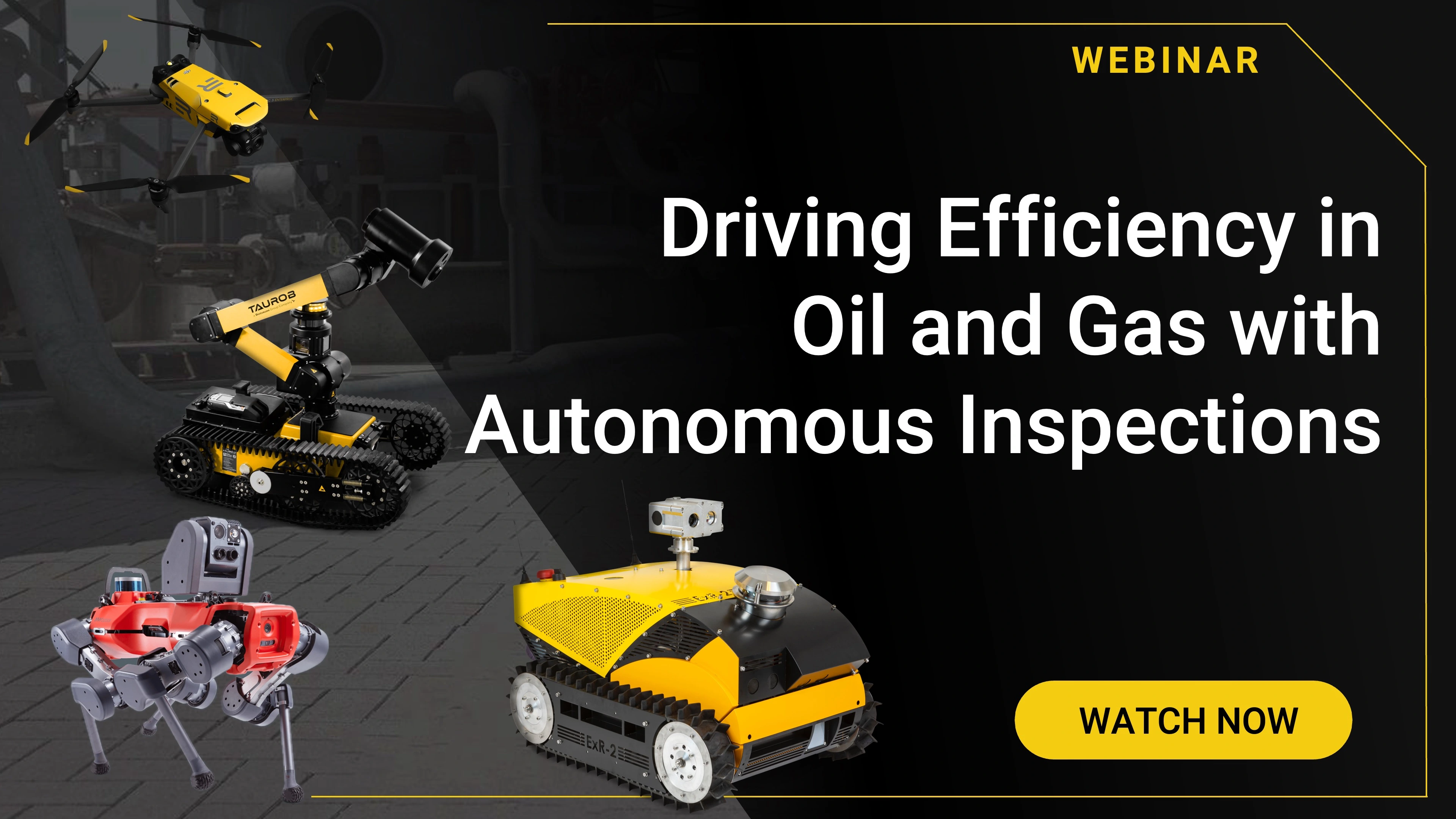
The Importance of Safety and Compliance in the Oil and Gas Industry
The oil and gas industry operates in a realm of inherent risks, where the consequences of accidents or incidents can be severe and far-reaching. From environmental disasters to worker injuries and financial losses, the potential ramifications underscore the paramount importance of maintaining rigorous safety protocols and adhering to stringent compliance regulations.
Safety is not merely a buzzword in our industry; it is a deeply ingrained value that permeates every aspect of our operations. We recognize that the well-being of our workforce, the protection of the environment, and the integrity of our assets are inextricably linked. By prioritizing safety through comprehensive inspections, we create a culture of vigilance and proactivity, where potential hazards are identified and mitigated before they can manifest into adverse events.
Compliance, on the other hand, is a non-negotiable obligation that we embrace wholeheartedly. The oil and gas industry is subject to a complex web of local, national, and international regulations, each designed to safeguard the public interest and ensure responsible practices. Inspections play a crucial role in verifying our adherence to these regulations, enabling us to operate with transparency and accountability.
Regulatory Requirements for Oil and Gas Inspections
The oil and gas industry is governed by a multitude of regulatory bodies and agencies, each with its own set of guidelines and mandates. Failure to comply with these regulations can result in severe penalties, operational disruptions, and reputational damage. As such, a comprehensive understanding of the applicable regulatory frameworks is essential for any organization operating in this sector.
At the international level, organizations such as the International Association of Oil & Gas Producers (IOGP) and the American Petroleum Institute (API) provide industry-wide standards and best practices for inspections and maintenance. These guidelines serve as a foundation upon which individual countries and regions build their specific regulatory frameworks.
In the United States, for example, the Occupational Safety and Health Administration (OSHA) and the Environmental Protection Agency (EPA) play crucial roles in overseeing workplace safety and environmental compliance, respectively. Similarly, in the European Union, the Seveso Directive outlines stringent regulations for the prevention and management of major industrial accidents.
Navigating this intricate web of regulations can be a daunting task, but it is one that we embrace with unwavering dedication. Our commitment to compliance is not merely a box-ticking exercise; it is a manifestation of our deep respect for the laws and regulations that safeguard the well-being of our stakeholders and the environment.
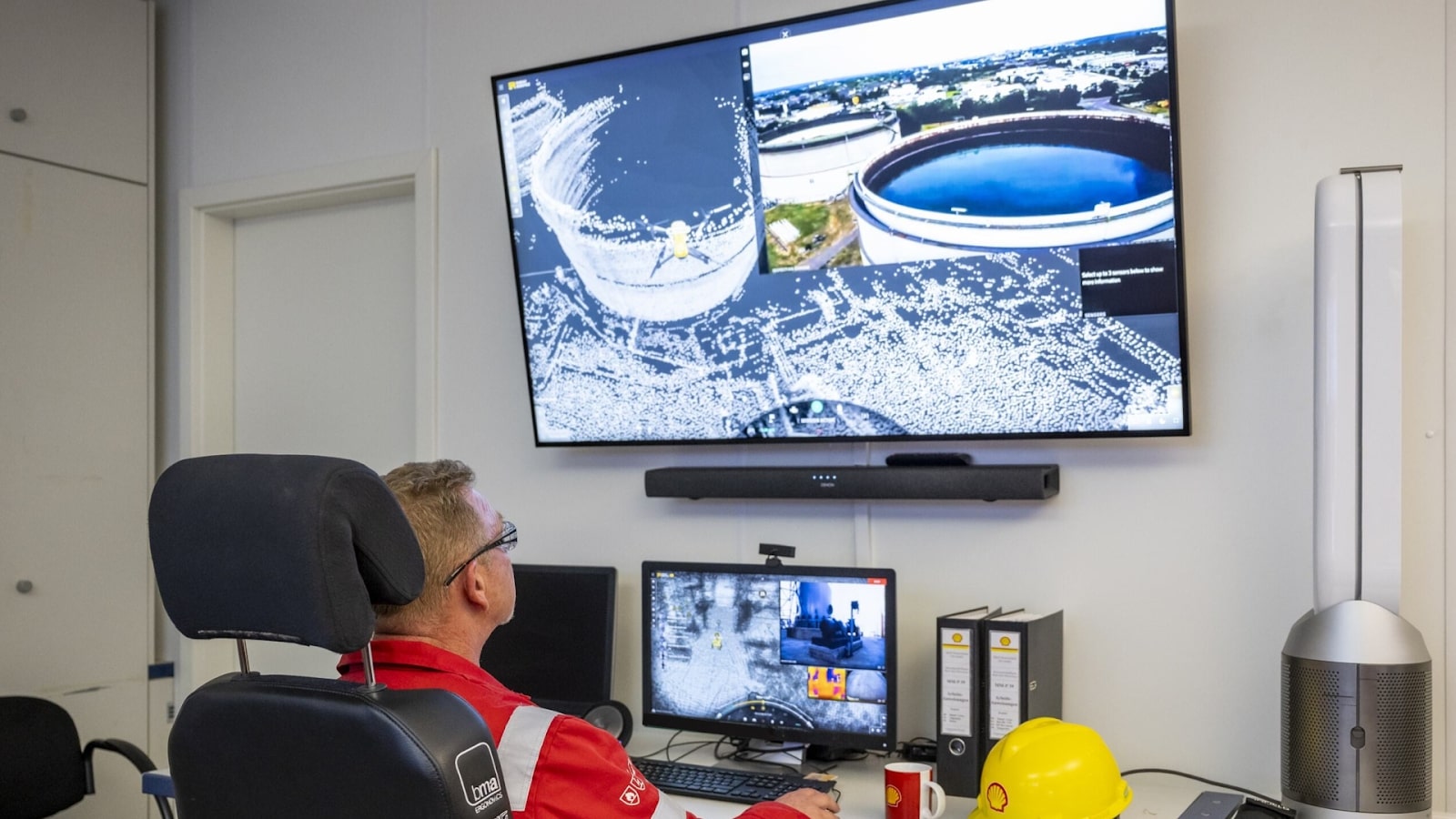
Types of Oil and Gas Inspections
The oil and gas industry encompasses a wide range of operations, each with its unique set of inspection requirements. From upstream exploration and production activities to midstream transportation and downstream refining and distribution, inspections play a critical role in ensuring the safe and efficient functioning of every aspect of the value chain.
- Upstream Inspections: These inspections focus on the exploration and production phases of the oil and gas lifecycle. They include:some text
- Well integrity inspections
- Drilling rig inspections
- Offshore platform inspections
- Pipeline inspections
- Facility inspections (e.g., production plants, storage tanks)
- Midstream Inspections: These inspections are centered around the transportation and storage of oil and gas products. They encompass:
- Pipeline integrity inspections
- Tank farm inspections
- Pump station inspections
- Terminal inspections
- Downstream Inspections: These inspections concentrate on the refining, processing, and distribution phases of the oil and gas industry. They include:
- Refinery inspections
- Petrochemical plant inspections
- Terminal and storage facility inspections
- Retail station inspections
Within each of these broad categories, there are numerous specialized inspections tailored to specific equipment, processes, or regulatory requirements. For example, pressure vessel inspections, corrosion monitoring, and leak detection are all critical components of a comprehensive inspection program.
Traditional methods of inspections: Manual inspection, stationary sensors
The oil and gas industry has relied on conventional inspection methods, such as manual inspections and stationary sensors. While these methods have served the industry well in the past, they are increasingly being challenged by the evolving demands of modern operations and the rapid pace of technological advancements.
- Manual Inspections: These inspections involve trained personnel physically inspecting equipment, facilities, and infrastructure. While manual inspections provide a hands-on approach and allow for direct observation, they can be time-consuming, labor-intensive, and potentially expose workers to hazardous environments.
- Stationary Sensors: Stationary sensors, such as pressure gauges, temperature sensors, and flow meters, are installed at strategic locations throughout oil and gas facilities. These sensors provide continuous monitoring and data collection, enabling the detection of anomalies or deviations from normal operating conditions. However, the effectiveness of stationary sensors is limited by their fixed locations and the potential for sensor failures or calibration issues. Furthermore, IoT sensors are very cost-prohibitive as you need thousands of them instead of one robot moving around with a sensor
Challenges with the traditional methods
While traditional inspection methods have served the industry well, they are not without their limitations and challenges. As the oil and gas industry evolves, these challenges become increasingly apparent, necessitating the adoption of more advanced and innovative inspection techniques.
- Safety Concerns: Manual inspections often require personnel to work in hazardous environments, such as confined spaces, elevated heights, or areas with potential exposure to toxic gases or flammable materials. This heightens the risk of accidents and injuries, underscoring the need for safer inspection methods.
- Limited Coverage and Accessibility: Stationary sensors and manual inspections can only cover a limited area or range, leaving blind spots or hard-to-reach areas uninspected. This can lead to missed defects or potential hazards, compromising the overall effectiveness of the inspection program.
- Human Error and Subjectivity: Manual inspections are susceptible to human error and subjective interpretation, which can lead to inconsistencies in data collection and analysis. This can result in missed defects or inaccurate assessments, potentially compromising safety and operational integrity.
- Inefficiencies and Downtime: Traditional inspection methods can be time-consuming and labor-intensive, often requiring facility shutdowns or operational disruptions. This can lead to significant productivity losses and increased operational costs.
- Data Management Challenges: Manual data collection and analysis processes can be prone to errors, inefficiencies, and delays. Integrating data from multiple sources and making informed decisions based on that data can be a significant challenge.
To address these challenges, the oil and gas industry has embraced technological advancements, incorporating cutting-edge inspection techniques and tools that enhance safety, efficiency, and accuracy while minimizing disruptions to operations.
Key Components of an Effective Inspection Program
An effective inspection program in the oil and gas industry is not a one-size-fits-all solution. It requires a carefully crafted approach that considers the unique characteristics of each operation, the specific regulatory requirements, and the evolving best practices within the industry. However, there are several key components that are essential for any successful inspection program:
- Comprehensive Risk Assessment: A thorough risk assessment is the foundation upon which an effective inspection program is built. This process involves identifying potential hazards, evaluating their likelihood and potential consequences, and prioritizing inspection activities accordingly.
- Clearly Defined Inspection Scope and Frequency: Based on the risk assessment, a well-defined scope and frequency for inspections must be established. This ensures that critical assets, equipment, and processes are inspected at appropriate intervals, minimizing the risk of undetected issues or defects.
- Qualified and Trained Personnel: Inspections must be conducted by personnel who possess the necessary qualifications, certifications, and training. This not only ensures the accuracy and reliability of the inspections but also promotes a culture of professionalism and accountability within the organization.
- Robust Data Management and Analysis: Effective data management and analysis are crucial for extracting valuable insights from inspection data. This includes the use of advanced software and tools for data collection, storage, and analysis, as well as the implementation of standardized reporting and documentation processes.
- Continuous Improvement and Adaptation: The oil and gas industry is constantly evolving, with new technologies, regulations, and best practices emerging regularly. An effective inspection program must be flexible and adaptable, incorporating continuous improvement mechanisms to ensure its relevance and effectiveness over time.
- Integration with Other Safety and Compliance Programs: Inspections should not operate in isolation; they should be integrated with other safety and compliance programs within the organization, such as maintenance, asset integrity management, and emergency response planning. This holistic approach ensures a comprehensive and coordinated effort toward risk mitigation and operational excellence.
By incorporating these key components, oil and gas companies can develop and implement inspection programs that not only meet regulatory requirements but also proactively identify and mitigate risks, enhance operational efficiency, and foster a culture of safety and continuous improvement.
Common Inspection Techniques and Tools
The oil and gas industry employs a diverse array of inspection techniques and tools to ensure the safe and efficient operation of its facilities. These techniques and tools are designed to address specific inspection requirements, ranging from routine maintenance checks to advanced diagnostic assessments. Here are some of the most common inspection techniques and tools used in the industry:
Daily inspection rounds in oil and gas plants
Daily inspection rounds are a fundamental aspect of maintaining safe and efficient operations in oil and gas plants. These routine checks are typically performed by trained personnel who physically inspect various components, equipment, and systems within the facility. The primary objectives of daily inspection rounds include:
- Visual Inspections: Trained personnel visually inspect equipment, piping, valves, and other components for signs of wear, corrosion, leaks, or other visible defects. This hands-on approach allows for early detection of potential issues before they escalate into more significant problems.
- Functional Testing: During daily rounds, personnel may also perform functional tests on critical equipment and systems to ensure they are operating within specified parameters. This can include testing safety devices, emergency shutoff valves, and other critical components.
- Housekeeping Checks: Daily rounds also involve inspecting the overall cleanliness and organization of the facility. Proper housekeeping is essential for maintaining a safe working environment and minimizing the risk of accidents or incidents.
- Documentation and Reporting: Detailed records of the inspection findings are typically maintained, allowing for trend analysis and proactive maintenance planning. Any identified issues or deficiencies are promptly reported and addressed through established protocols.
Daily inspection rounds are a proactive measure that helps to identify and address potential issues before they can escalate into more significant problems, thereby minimizing the risk of unplanned shutdowns, accidents, or environmental incidents.
Early detection of anomalies to avoid shutdowns
In the oil and gas industry, unplanned shutdowns can have severe consequences, ranging from lost production and revenue to potential safety hazards and environmental impacts. Early detection of anomalies is crucial to avoiding such shutdowns and ensuring the continuous and safe operation of facilities.
One of the key techniques employed for early detection is the use of advanced monitoring and sensing technologies. These technologies can include:
- Predictive Maintenance Systems: Predictive maintenance systems utilize sensor data, machine learning algorithms, and historical data to identify patterns and predict potential equipment failures or degradation. By detecting these anomalies early, maintenance can be scheduled proactively, avoiding unplanned shutdowns and minimizing downtime.
- Condition Monitoring: Condition monitoring involves the continuous or periodic monitoring of critical equipment and systems to assess their operational health. This can include monitoring vibration levels, temperature, pressure, and other parameters that can indicate potential issues or deviations from normal operating conditions.
- Leak Detection Systems: Advanced leak detection systems, such as acoustic sensors, infrared cameras, and gas detectors, are employed to identify and locate leaks in pipelines, tanks, and other infrastructure. Early detection of leaks can prevent escalation into more significant incidents and minimize environmental impact.
- Corrosion Monitoring: Corrosion is a major concern in the oil and gas industry, as it can compromise the integrity of equipment and infrastructure. Corrosion monitoring techniques, such as ultrasonic testing, radiography, and electrochemical techniques, are used to detect and monitor corrosion rates, enabling timely maintenance and repair actions.
By leveraging these advanced techniques and technologies, oil and gas companies can detect anomalies and potential issues at an early stage, allowing for proactive interventions and minimizing the risk of unplanned shutdowns or incidents.
To ensure the safety of the workers (gas leaks)
Ensuring the safety of workers is a paramount concern in the oil and gas industry, where the potential for gas leaks and other hazardous incidents is ever-present. Effective inspection techniques and tools play a crucial role in identifying and mitigating these risks, protecting the well-being of personnel, and maintaining a safe working environment.
One of the primary inspection techniques employed to detect gas leaks is the use of gas detection systems. These systems typically involve the deployment of fixed or portable gas detectors that are capable of detecting and monitoring the presence of various gases, such as hydrogen sulfide, methane, and other hydrocarbons.
- Fixed Gas Detection Systems: These systems consist of strategically placed gas detectors throughout the facility, providing continuous monitoring and early warning of gas leaks. They are often integrated with alarm systems and emergency response protocols, enabling rapid and coordinated action in the event of a detected leak.
- Portable Gas Detectors: Portable gas detectors are handheld devices that can be carried by personnel during inspections or maintenance activities. These devices allow for targeted monitoring in specific areas or confined spaces, providing an additional layer of protection for workers.
In addition to gas detection systems, other inspection techniques and tools are employed to ensure worker safety, including:
- Infrared Cameras: Infrared cameras can detect and visualize gas leaks by identifying temperature differences or patterns that may indicate the presence of hydrocarbons or other gases.
- Acoustic Emission Testing: This non-destructive testing technique can detect and locate leaks by analyzing the high-frequency sound waves generated by gas escaping from pressurized systems or components.
- Confined Space Entry Procedures: Rigorous confined space entry procedures, including atmospheric monitoring and ventilation, are implemented to ensure the safety of workers entering confined spaces, where the risk of gas accumulation or oxygen deficiency is heightened.
- Personal Protective Equipment (PPE): Appropriate PPE, such as gas-tight suits, self-contained breathing apparatus, and other specialized equipment, is provided to workers based on the specific hazards and risks associated with their tasks.
By employing these inspection techniques and tools, oil and gas companies can proactively identify and mitigate gas leak risks, creating a safer working environment for their personnel and minimizing the potential for incidents that could endanger human life or compromise operational integrity.
The Role of Technology in Modern Oil and Gas Inspections
In the ever-evolving landscape of the oil and gas industry, technology has emerged as a game-changer, revolutionizing the way inspections are conducted. Traditional methods, while still valuable, are being augmented and, in some cases, replaced by cutting-edge technological solutions that offer unprecedented levels of efficiency, accuracy, and safety.
AI-driven Robotic Inspection
Artificial Intelligence (AI) and robotics have ushered in a new era of inspection capabilities in the oil and gas industry. AI-driven robotic inspection systems can navigate and inspect even the most challenging and hazardous environments, minimizing the need for human intervention and reducing the risk of accidents or injuries.
These advanced robotic systems are equipped with a suite of sensors, cameras, and other specialized equipment that allow for comprehensive data collection and analysis. By leveraging machine learning algorithms and computer vision technologies, these systems can detect and identify defects, anomalies, and potential issues with remarkable accuracy and speed.
One of the key advantages of AI-driven robotic inspection is the ability to access and inspect areas that are difficult or impossible for human inspectors to reach safely. This includes confined spaces, elevated structures, and hazardous environments where the presence of toxic gases or extreme temperatures would pose significant risks to human personnel.
Furthermore, robotic inspection systems can operate continuously, minimizing the need for shutdowns or operational disruptions. This not only enhances productivity and efficiency but also reduces the potential for unplanned downtime and associated financial losses.
Oil Tank Aerial Inspections
Aerial inspections have become an integral part of the oil and gas industry, offering a comprehensive and efficient means of monitoring and inspecting vast areas of infrastructure, such as pipelines, well pads, and storage tanks. Advanced drone technology, coupled with high-resolution cameras and specialized sensors, has revolutionized this inspection approach.
Unmanned Aerial Vehicles (UAVs), or drones, can cover large areas quickly and safely, capturing detailed visual data and sensor readings that can be analyzed for potential issues or anomalies. This not only enhances the efficiency of inspections but also minimizes the risk to personnel who would otherwise need to physically access these areas.
Aerial inspections can detect a wide range of issues, including leaks, corrosion, structural defects, and vegetation encroachment. By utilizing thermal imaging cameras, gas detection sensors, and other specialized equipment, drones can provide a comprehensive assessment of the condition and integrity of oil and gas assets.
Moreover, the data collected during aerial inspections can be integrated with advanced analytics and machine learning algorithms, enabling predictive maintenance and proactive decision-making. This data-driven approach allows for more efficient resource allocation, optimized maintenance schedules, and improved overall asset management.
Early Gas Leak Detection
Early detection of gas leaks is a critical safety and environmental concern in the oil and gas industry. Traditional methods of leak detection, such as manual inspections or stationary sensors, can be time-consuming, labor-intensive, and limited in their coverage. However, modern technologies are revolutionizing the way gas leaks are detected and addressed.
One of the most promising technologies in this area is the use of advanced gas detection sensors and systems. These sensors can be deployed in various configurations, including fixed installations, mobile platforms, and even aerial drones. By leveraging cutting-edge sensor technologies, such as infrared, laser-based, or electrochemical sensors, these systems can detect and pinpoint gas leaks with high accuracy and sensitivity.
Additionally, advanced data analytics and machine learning algorithms are being integrated with these sensor systems, enabling real-time monitoring, pattern recognition, and predictive analytics. This allows for proactive identification of potential leak sources, enabling timely interventions and minimizing the risk of larger-scale incidents.
Another innovative approach to early gas leak detection is the use of hyperspectral imaging technology. This technology combines high-resolution imaging with spectroscopic analysis, enabling the detection and identification of gas plumes and leaks based on their unique spectral signatures. Hyperspectral imaging can be deployed from aerial platforms, such as drones or aircraft, providing a comprehensive and efficient means of surveying large areas for potential leaks.
By embracing these cutting-edge technologies, the oil and gas industry can significantly enhance its ability to detect and address gas leaks early, minimizing the environmental impact, ensuring worker safety, and maintaining operational integrity.
Monitor Analog Gauges
In the oil and gas industry, analog gauges remain widely used to monitor parameters such as pressure, temperature, and flow rates. Although these gauges are reliable, manual data collection can lead to challenges like human error and limited accessibility in hazardous or remote areas. To overcome these issues, robots equipped with AI are revolutionizing how analog gauges are monitored. These robots use advanced computer vision and machine learning algorithms to autonomously read and interpret the data from analog gauge displays. By employing AI-powered optical recognition, the robots can accurately capture readings without human intervention, eliminating manual data entry errors.
In addition, AI-enhanced robots can operate in dangerous or hard-to-reach locations, collecting real-time data and transmitting it for remote analysis. This not only enhances safety by reducing the need for human presence in hazardous environments but also boosts the efficiency and precision of data collection. Moreover, some robotic systems can be integrated with augmented reality (AR) tools, allowing personnel to visualize real-time gauge data overlaid onto their environment. These AR systems, combined with AI, can provide alerts when readings deviate from safe parameters, enabling timely interventions and preventing equipment failure. By incorporating AI-driven robots into their operations, the oil and gas industry can modernize the monitoring of analog gauges, ensuring greater safety, data accuracy, and operational efficiency.
Another innovative approach to monitoring analog gauges is the use of augmented reality (AR) technologies. AR systems can overlay digital information and visualizations onto the physical world, enabling personnel to view real-time gauge readings and other relevant data directly through their AR devices.
These AR systems can also incorporate predictive analytics and machine learning algorithms, providing real-time alerts and notifications when gauge readings deviate from expected norms or approach critical thresholds. This proactive approach allows for timely interventions and maintenance activities, minimizing the risk of equipment failure or operational disruptions.
By embracing these cutting-edge technologies, the oil and gas industry can modernize its approach to monitoring analog gauges, enhancing safety, improving data accuracy, and enabling more efficient and effective decision-making processes.
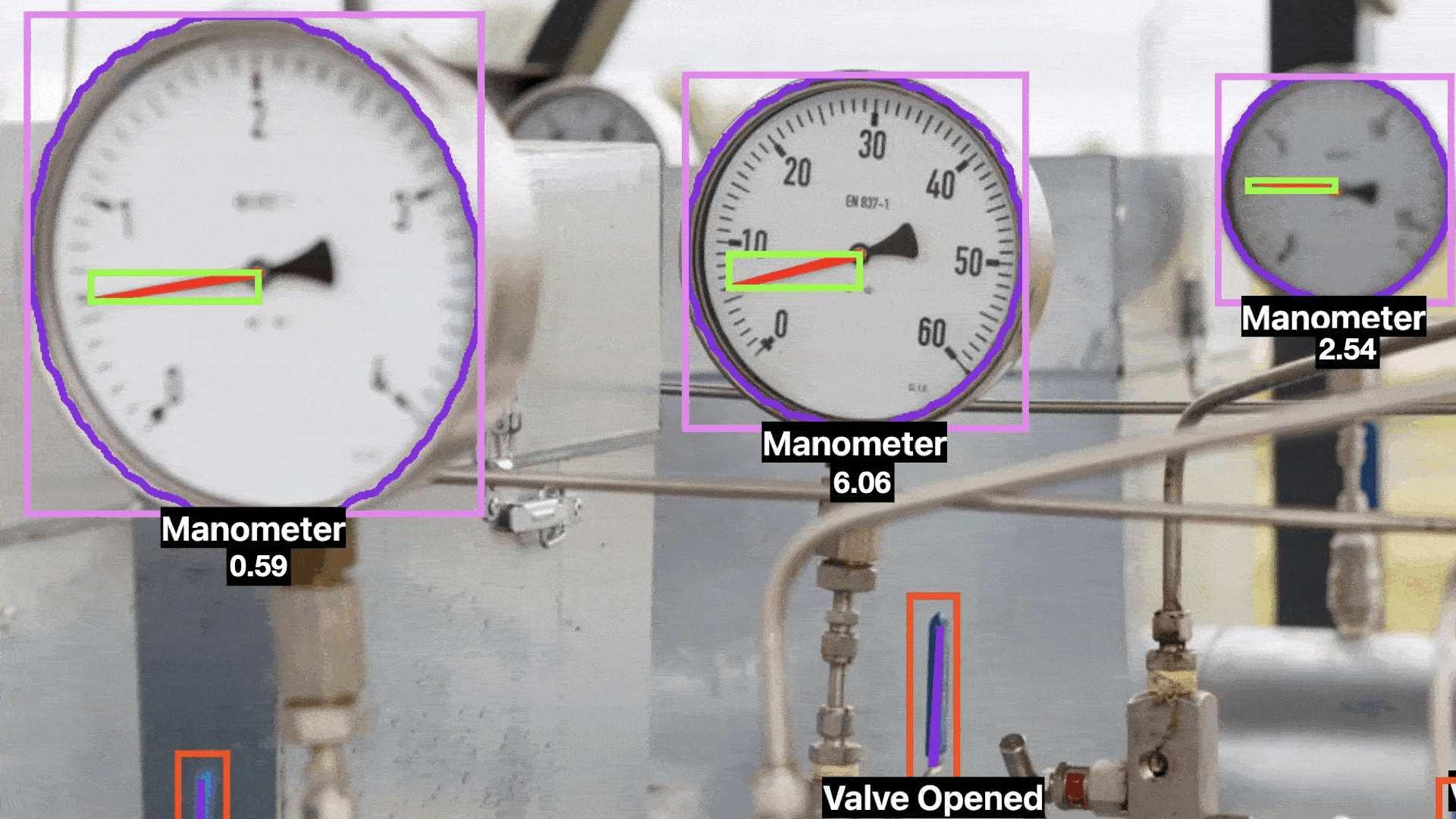
On-demand Inspection Rounds
Operator rounds, where personnel manually inspect and monitor oil and gas facilities, are essential for ensuring safe and efficient operations. However, traditional rounds can be time-consuming, repetitive, and expose workers to dangerous environments. To address these issues, the concept of "On-demand Inspection Rounds" has gained traction, with drones and autonomous robots playing a central role in transforming this process.
Drones and robots, equipped with advanced sensors and cameras, can autonomously navigate facilities to monitor equipment, perform inspections and detect anomalies. These machines continuously gather data on operational conditions, such as pressure, temperature, and environmental factors, and send it in real time for analysis. Using artificial intelligence and machine learning, the data is processed to identify deviations from normal conditions, triggering alerts for operators to intervene only where necessary.
This shift towards drones and robots as key inspection tools not only enhances efficiency by reducing the need for routine manual rounds but also significantly improves worker safety by minimizing exposure to hazardous areas. Furthermore, the precision and consistency of data collected by these autonomous systems improve accuracy, reducing human error in reporting equipment conditions. When integrated with digital twins or virtual models of the facility, drones and robots provide operators with a comprehensive, real-time view of the plant. This enables more informed decision-making, proactive maintenance, and better resource allocation.
By adopting drones and robots in on-demand inspection rounds, the oil and gas industry can achieve a safer, more efficient, and data-driven approach to facility monitoring, ultimately optimizing performance and minimizing risks.
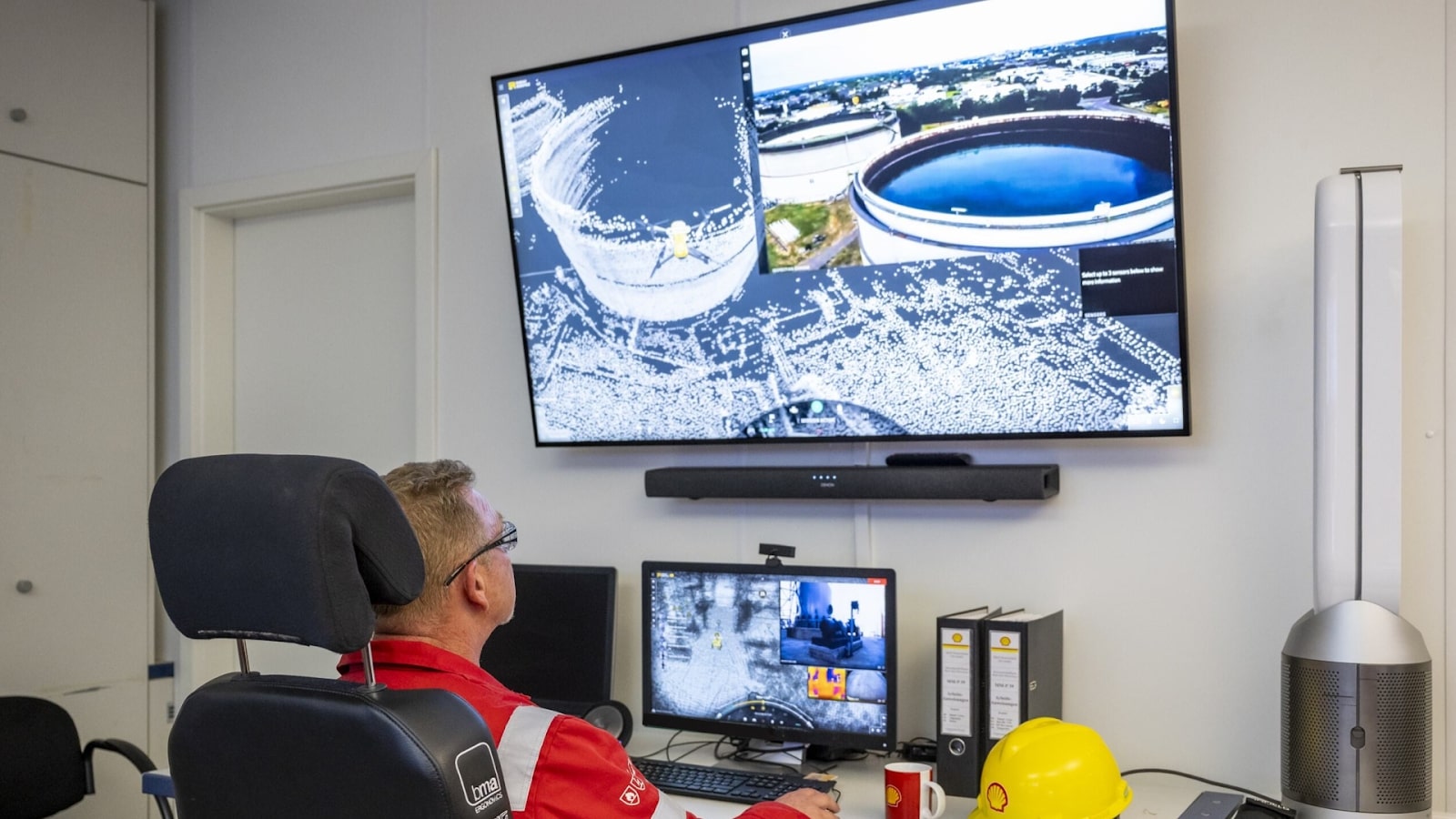
Thermal Imaging
Thermal imaging technology has become an indispensable tool in the oil and gas industry, providing a non-invasive, efficient method for inspecting and monitoring various assets and processes. By detecting and visualizing temperature differences, thermal imaging cameras reveal crucial information that might not be visible to the naked eye.
A key application of thermal imaging is the detection of leaks and insulation defects. Hydrocarbons and other gases often show temperature variations compared to their surroundings, making them detectable through thermal imaging. This technology allows for rapid and precise identification of leaks in pipelines, storage tanks, and other equipment, enabling timely repairs and minimizing environmental risks and safety hazards.
In addition to leak detection, thermal imaging is essential for monitoring electrical and mechanical equipment. Abnormal temperature patterns can indicate issues like overheating components, bearing failures, or electrical faults, which, if caught early, can prevent costly shutdowns, extend equipment lifespan, and reduce overall maintenance costs.
Thermal imaging also plays a significant role in enhancing worker safety by detecting potential hazards, such as hot surfaces or gas leaks. These early warnings enable personnel to take appropriate safety measures or evacuate when necessary, reducing the risk of accidents.
The integration of thermal imaging with advanced technologies, such as drones and robots, has revolutionized inspections. Robots equipped with AI-driven thermographic analysis, as developed by Energy Robotics, can autonomously detect and interpret temperature anomalies in real time. These robots perform thermal inspections of pipelines, electrical systems, and machinery with precision, spotting irregularities that signal potential faults. This integration enables robots to access hazardous or difficult-to-reach areas, capturing thermal data without endangering human workers, and offering continuous monitoring with enhanced accuracy.
As safety, efficiency, and environmental sustainability remain top priorities in the oil and gas industry, thermal imaging, especially when paired with AI-driven robotic inspections, will continue to be a vital tool. It enables proactive maintenance, effective leak detection, and improved situational awareness, contributing to safer and more efficient operations.
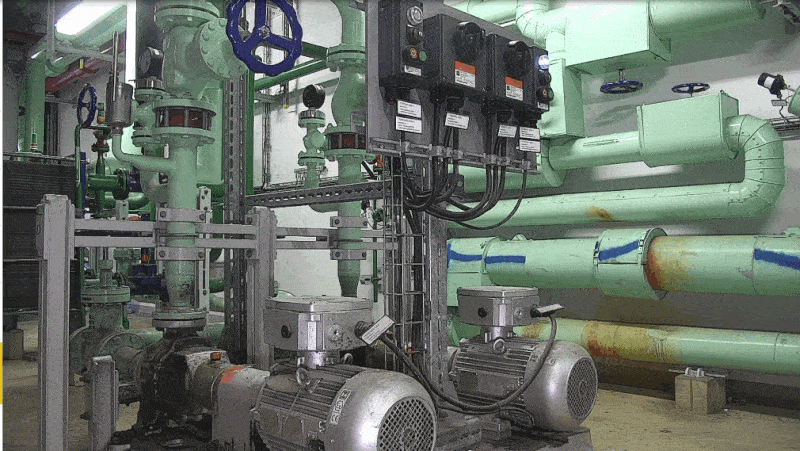
Inspect in ATEX/IECEx Zone 1 Areas
The oil and gas industry often involves operations in hazardous areas where the presence of flammable gases or vapors creates a risk of explosions. These areas are classified according to international standards, such as ATEX (Atmosphere Explosible) in Europe and IECEx (International Electrotechnical Commission System for Certification to Standards Relating to Equipment for Use in Explosive Atmospheres) globally.
Zone 1 areas, as defined by these standards, are locations where an explosive gas atmosphere is likely to occur in normal operation. Conducting inspections and maintenance activities in these high-risk environments requires specialized equipment and procedures to ensure the safety of personnel and prevent potential ignition sources.
To address this challenge, the oil and gas industry has embraced advanced technologies and inspection methods specifically designed for use in ATEX/IECEx Zone 1 areas. One such technology is the use of intrinsically safe (IS) equipment, which is designed to limit the amount of energy available for ignition, even in the presence of flammable gases or vapors.
Intrinsically safe cameras, sensors, and other inspection tools allow personnel to safely conduct visual inspections, collect data, and monitor equipment conditions without introducing potential ignition sources. These tools are rigorously tested and certified to meet the stringent safety requirements for use in hazardous environments.
Another approach to inspecting ATEX/IECEx Zone 1 areas is the use of remotely operated vehicles (ROVs) or robots. These unmanned systems can be equipped with various sensors, cameras, and other inspection tools, enabling comprehensive data collection and monitoring without exposing personnel to a hazardous environment.
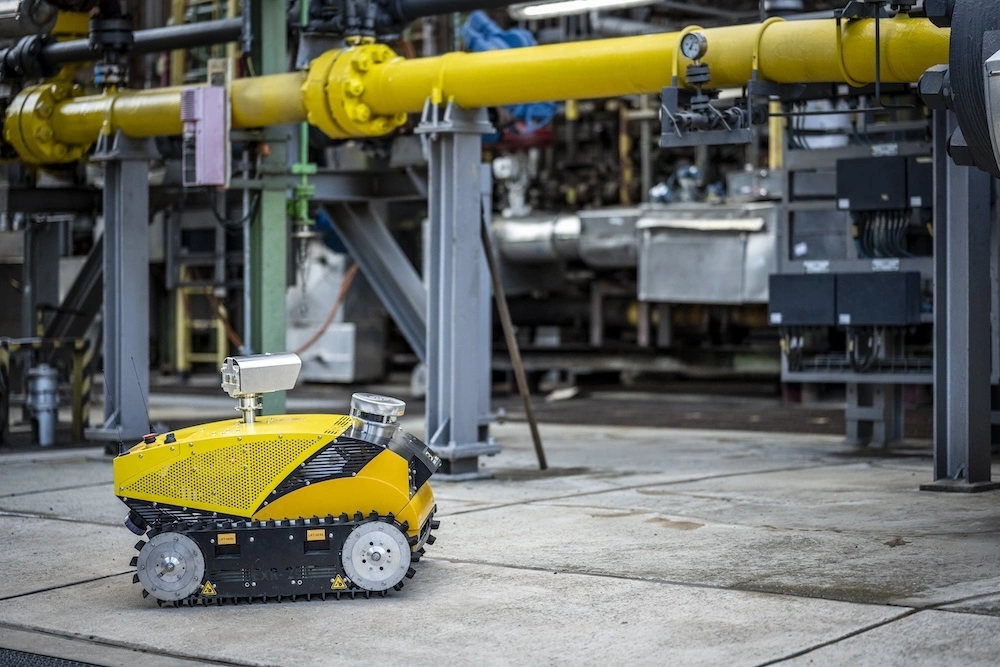
Advanced robotics and automation technologies are also being employed to perform maintenance and repair tasks in Zone 1 areas, further minimizing the need for human intervention and reducing the associated risks.
Additionally, the oil and gas industry is leveraging advanced simulation and digital twin technologies to create virtual representations of hazardous areas. These digital models can be used for training purposes, allowing personnel to practice and familiarize themselves with inspection and maintenance procedures in a safe, simulated environment before entering the actual hazardous area.
By embracing these cutting-edge technologies and inspection methods, the oil and gas industry can maintain a high level of operational excellence while prioritizing the safety of personnel and adhering to stringent regulatory standards for hazardous area operations.
Conclusion
As we navigate the ever-evolving landscape of the oil and gas industry, the crucial role of inspections cannot be overstated. From ensuring regulatory compliance and operational integrity to safeguarding the well-being of our workforce and the environment, inspections are the cornerstone upon which our industry's success is built.
Throughout this article, we have explored the various facets of inspections, delving into their importance, regulatory requirements, and the diverse array of techniques and tools employed. We have witnessed how technology has revolutionized the inspection process, introducing innovative solutions that enhance efficiency, accuracy, and safety.
However, it is important to recognize that inspections are not merely a checklist of tasks or a box to be ticked. They are a manifestation of our unwavering commitment to excellence, a testament to our dedication to upholding the highest standards of operational integrity, and a reflection of our respect for the trust placed in us by stakeholders, communities, and the broader public.
As we look towards the future, the oil and gas industry must continue to embrace innovation and adapt to the ever-changing technological landscape. We must remain vigilant, proactive, and uncompromising in our pursuit of safety, environmental stewardship, and operational excellence.
It is my sincere hope that this article has not only provided valuable insights into the world of oil and gas inspections but has also ignited a sense of passion and appreciation for the critical role they play in shaping the success and sustainability of our industry.