Einführung in die Öl- und Gasinspektionen
In der komplizierten Welt der Öl- und Gasindustrie, in der viel auf dem Spiel steht, spielen akribische Inspektionen eine entscheidende Rolle bei der Gewährleistung der Sicherheit, Effizienz und Einhaltung der Betriebsvorschriften.
Der Öl- und Gassektor ist ein komplexes Ökosystem, in dem selbst kleinste Versehen oder Fahrlässigkeit weitreichende Folgen haben können. Strenge Inspektionen sind der Eckpfeiler eines proaktiven Risikomanagements. Sie ermöglichen es uns, potenzielle Gefahren zu erkennen, Schwachstellen zu beheben und Präventivmaßnahmen zu ergreifen, bevor sie zu katastrophalen Vorfällen eskalieren.
Darüber hinaus sind Inspektionen nicht nur eine Frage der Einhaltung gesetzlicher Vorschriften; sie sind ein Beweis für unser unerschütterliches Engagement für Spitzenleistungen und unser Engagement für die Einhaltung der höchsten Standards der betrieblichen Integrität. Indem wir Inspektionen Priorität einräumen, zeigen wir unseren Respekt für das Vertrauen, das uns von Interessengruppen, Gemeinden und der breiten Öffentlichkeit entgegengebracht wird.
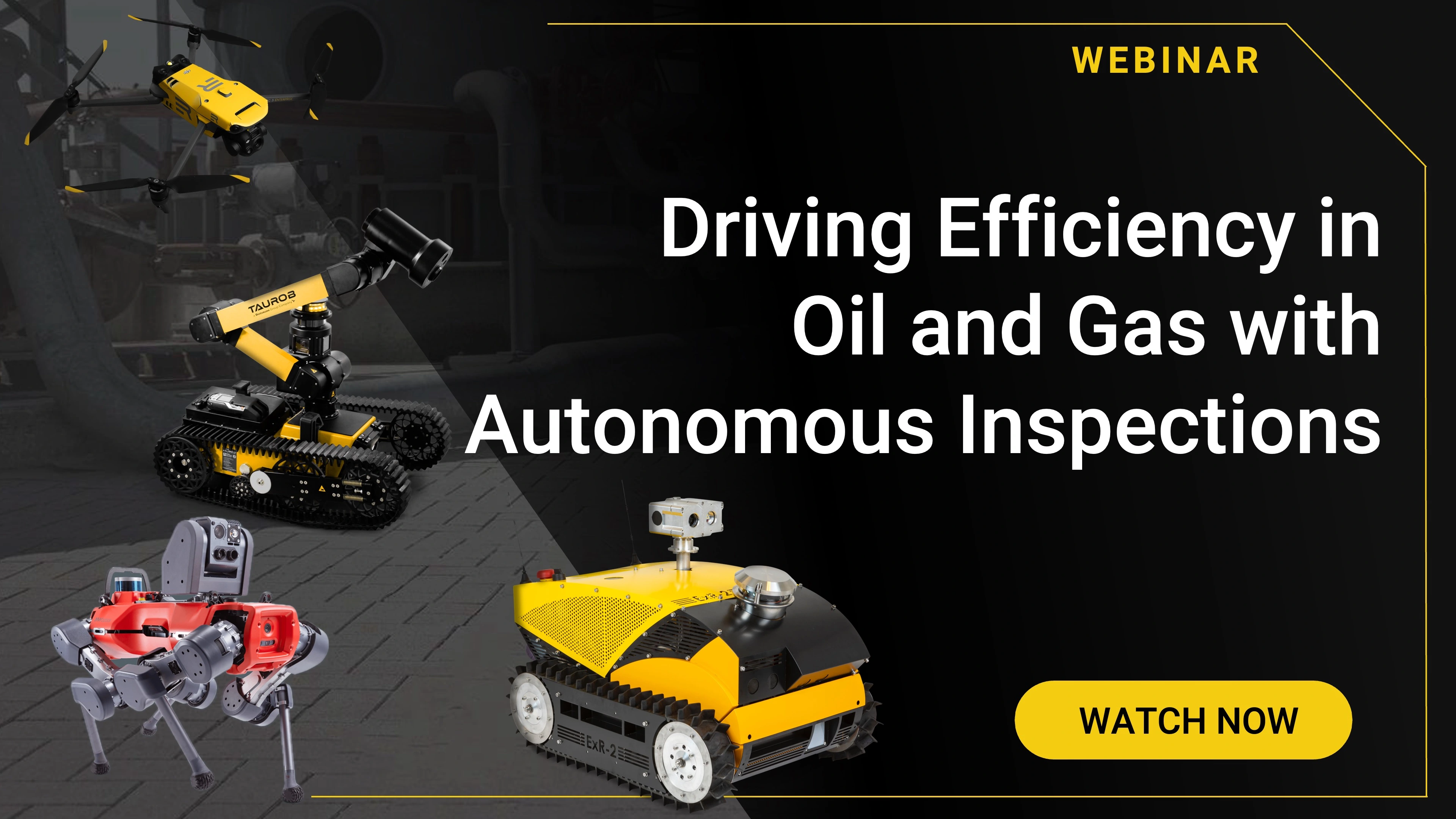
Die Bedeutung von Sicherheit und Compliance in der Öl- und Gasindustrie
Die Öl- und Gasindustrie ist in einem Bereich inhärenter Risiken tätig, in dem die Folgen von Unfällen oder Zwischenfällen schwerwiegend und weitreichend sein können. Von Umweltkatastrophen über Arbeitsunfälle bis hin zu finanziellen Verlusten — die potenziellen Auswirkungen unterstreichen, wie wichtig es ist, strenge Sicherheitsprotokolle einzuhalten und strenge Compliance-Vorschriften einzuhalten.
Sicherheit ist in unserer Branche nicht nur ein Schlagwort, sondern ein tief verwurzelter Wert, der jeden Aspekt unserer Geschäftstätigkeit durchdringt. Wir sind uns bewusst, dass das Wohlbefinden unserer Belegschaft, der Schutz der Umwelt und die Integrität unserer Vermögenswerte untrennbar miteinander verbunden sind. Indem wir der Sicherheit durch umfassende Inspektionen Priorität einräumen, schaffen wir eine Kultur der Wachsamkeit und Proaktivität, in der potenzielle Gefahren erkannt und gemindert werden, bevor sie sich in unerwünschten Ereignissen äußern können.
Die Einhaltung der Vorschriften ist dagegen eine nicht verhandelbare Verpflichtung, der wir uns voll und ganz stellen. Die Öl- und Gasindustrie unterliegt einem komplexen Geflecht lokaler, nationaler und internationaler Vorschriften, die jeweils darauf ausgerichtet sind, das öffentliche Interesse zu schützen und verantwortungsvolle Praktiken sicherzustellen. Inspektionen spielen eine entscheidende Rolle bei der Überprüfung unserer Einhaltung dieser Vorschriften und ermöglichen es uns, transparent und rechenschaftspflichtig zu arbeiten.
Regulatorische Anforderungen für Öl- und Gasinspektionen
Die Öl- und Gasindustrie wird von einer Vielzahl von Aufsichtsbehörden und Behörden kontrolliert, von denen jede ihre eigenen Richtlinien und Mandate hat. Die Nichteinhaltung dieser Vorschriften kann zu schweren Strafen, Betriebsstörungen und Reputationsschäden führen. Daher ist ein umfassendes Verständnis der geltenden regulatorischen Rahmenbedingungen für jedes Unternehmen, das in diesem Sektor tätig ist, unerlässlich.
Auf internationaler Ebene bieten Organisationen wie die International Association of Oil & Gas Producers (IOGP) und das American Petroleum Institute (API) branchenweite Standards und bewährte Verfahren für Inspektionen und Wartungsarbeiten an. Diese Richtlinien dienen als Grundlage, auf der die einzelnen Länder und Regionen ihre spezifischen regulatorischen Rahmenbedingungen aufbauen.
In den Vereinigten Staaten spielen beispielsweise die Occupational Safety and Health Administration (OSHA) und die Environmental Protection Agency (EPA) eine entscheidende Rolle bei der Überwachung der Sicherheit am Arbeitsplatz bzw. der Einhaltung der Umweltvorschriften. In ähnlicher Weise enthält die Seveso-Richtlinie in der Europäischen Union strenge Vorschriften für die Verhütung und Bewältigung schwerer Arbeitsunfälle.
Es kann eine schwierige Aufgabe sein, sich in diesem komplizierten Netz von Vorschriften zurechtzufinden, aber wir stellen uns ihr mit unerschütterlichem Engagement. Unser Bekenntnis zur Einhaltung der Vorschriften ist nicht nur ein Ankreuzen von Kästchen, sondern Ausdruck unseres tiefen Respekts vor den Gesetzen und Vorschriften, die das Wohlergehen unserer Stakeholder und der Umwelt schützen.
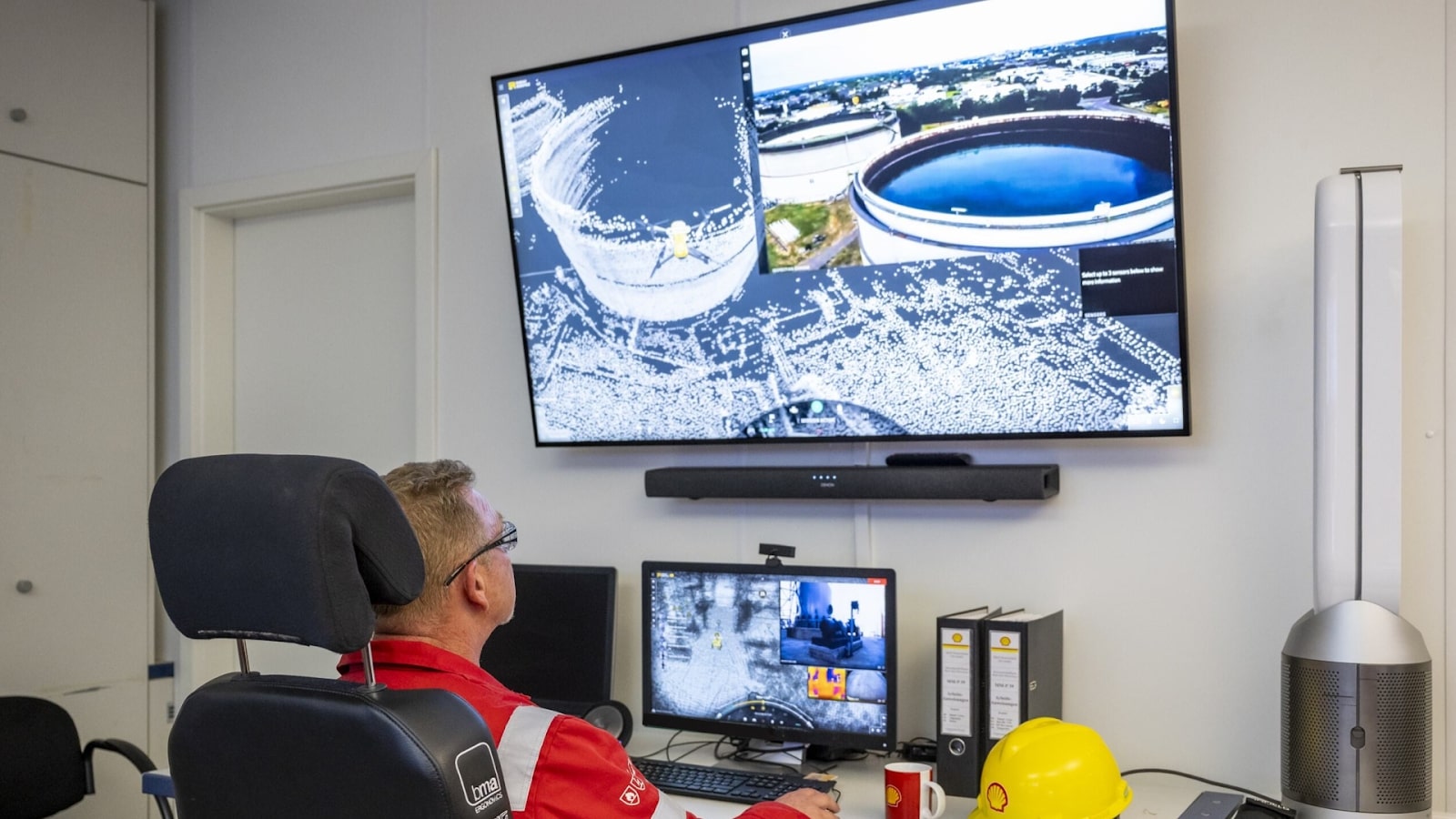
Arten von Öl- und Gasinspektionen
Die Öl- und Gasindustrie umfasst ein breites Spektrum von Betrieben, von denen jeder seine eigenen Inspektionsanforderungen hat. Von den vorgelagerten Explorations- und Produktionsaktivitäten über den Transport im Zwischenstrombereich bis hin zur nachgelagerten Raffination und Verteilung spielen Inspektionen eine entscheidende Rolle, wenn es darum geht, das sichere und effiziente Funktionieren aller Aspekte der Wertschöpfungskette zu gewährleisten.
- Upstream Inspektionen: Diese Inspektionen konzentrieren sich auf die Explorations- und Produktionsphasen des Öl- und Gaslebenszyklus. Sie beinhalten: etwas Text
- Inspektionen der Brunnenintegrität
- Inspektionen von Bohranlagen
- Inspektionen von Offshore-Plattformen
- Inspektionen von Rohrleitungen
- Anlageninspektionen (z. B. Produktionsanlagen, Lagertanks)
- Midstream Inspektionen: Diese Inspektionen konzentrieren sich auf den Transport und die Lagerung von Öl- und Gasprodukten. Sie umfassen:
- Inspektionen der Pipeline-Integrität
- Inspektionen von Tanklager
- Inspektionen von Pumpstationen
- Terminalinspektionen
- Downstream Inspektionen: Diese Inspektionen konzentrieren sich auf die Raffinations-, Verarbeitungs- und Vertriebsphasen der Öl- und Gasindustrie. Sie beinhalten:
- Inspektionen von Raffinerien
- Inspektionen petrochemischer Anlagen
- Inspektionen von Terminals und Lagereinrichtungen
- Inspektionen von Einzelhandelsstationen
In jeder dieser großen Kategorien gibt es zahlreiche spezialisierte Inspektionen, die auf bestimmte Geräte, Prozesse oder behördliche Anforderungen zugeschnitten sind. So sind beispielsweise die Inspektion von Druckbehältern, die Korrosionsüberwachung und die Lecksuche wichtige Bestandteile eines umfassenden Inspektionsprogramms.
Traditionelle Inspektionsmethoden: Manuelle Inspektion, stationäre Sensoren
Die Öl- und Gasindustrie hat sich auf konventionelle Inspektionsmethoden wie manuelle Inspektionen und stationäre Sensoren verlassen. Obwohl diese Methoden der Branche in der Vergangenheit gute Dienste geleistet haben, werden sie zunehmend durch die sich ändernden Anforderungen moderner Betriebsabläufe und das schnelle Tempo des technologischen Fortschritts in Frage gestellt.
- Manuelle Inspektionen: Bei diesen Inspektionen inspiziert geschultes Personal Ausrüstung, Einrichtungen und Infrastruktur physisch. Manuelle Inspektionen bieten zwar einen praktischen Ansatz und ermöglichen eine direkte Beobachtung, sie können jedoch zeitaufwändig und arbeitsintensiv sein und die Mitarbeiter potenziell gefährlichen Umgebungen aussetzen.
- Stationäre Sensoren: Stationäre Sensoren wie Manometer, Temperatursensoren und Durchflussmesser werden an strategischen Stellen in allen Öl- und Gasanlagen installiert. Diese Sensoren sorgen für eine kontinuierliche Überwachung und Datenerfassung und ermöglichen die Erkennung von Anomalien oder Abweichungen von den normalen Betriebsbedingungen. Die Wirksamkeit stationärer Sensoren ist jedoch durch ihre feste Position und das Potenzial von Sensorausfällen oder Kalibrierungsproblemen begrenzt. Darüber hinaus sind IoT-Sensoren sehr kostenintensiv, da Sie Tausende von ihnen benötigen, anstatt dass ein Roboter mit einem Sensor herumläuft
Herausforderungen mit den traditionellen Methoden
Traditionelle Inspektionsmethoden haben der Branche zwar gute Dienste geleistet, sind jedoch nicht ohne Einschränkungen und Herausforderungen. Im Zuge der Weiterentwicklung der Öl- und Gasindustrie werden diese Herausforderungen immer offensichtlicher und erfordern die Einführung fortschrittlicherer und innovativerer Inspektionstechniken.
- Sicherheitsbedenken: Bei manuellen Inspektionen muss das Personal häufig in gefährlichen Umgebungen arbeiten, z. B. in engen Räumen, erhöhten Höhen oder Bereichen, in denen giftige Gase oder brennbare Materialien auftreten können. Dies erhöht das Unfall- und Verletzungsrisiko und unterstreicht die Notwendigkeit sichererer Inspektionsmethoden.
- Eingeschränkte Reichweite und Zugänglichkeit: Stationäre Sensoren und manuelle Inspektionen können nur einen begrenzten Bereich oder Bereich abdecken, sodass tote Winkel oder schwer zugängliche Bereiche nicht inspiziert werden. Dies kann dazu führen, dass Mängel oder potenzielle Gefahren übersehen werden, was die Gesamteffektivität des Inspektionsprogramms beeinträchtigt.
- Menschliches Versagen und Subjektivität: Manuelle Inspektionen sind anfällig für menschliche Fehler und subjektive Interpretationen, was zu Inkonsistenzen bei der Datenerfassung und -analyse führen kann. Dies kann dazu führen, dass Mängel übersehen oder ungenaue Bewertungen vorgenommen werden, was möglicherweise die Sicherheit und Betriebsintegrität beeinträchtigt.
- Ineffizienzen und Ausfallzeiten: Herkömmliche Inspektionsmethoden können zeitaufwändig und arbeitsintensiv sein und erfordern häufig Anlagenstillstände oder Betriebsunterbrechungen. Dies kann zu erheblichen Produktivitätsverlusten und erhöhten Betriebskosten führen.
- Herausforderungen beim Datenmanagement: Manuelle Datenerfassungs- und Analyseprozesse können anfällig für Fehler, Ineffizienzen und Verzögerungen sein. Die Integration von Daten aus mehreren Quellen und das Treffen fundierter Entscheidungen auf der Grundlage dieser Daten kann eine große Herausforderung sein.
Um diesen Herausforderungen zu begegnen, hat die Öl- und Gasindustrie technologische Fortschritte gemacht und modernste Inspektionstechniken und -werkzeuge eingeführt, die die Sicherheit, Effizienz und Genauigkeit erhöhen und gleichzeitig Betriebsunterbrechungen minimieren.
Schlüsselkomponenten eines effektiven Inspektionsprogramms
Ein effektives Inspektionsprogramm in der Öl- und Gasindustrie ist keine Universallösung. Es erfordert einen sorgfältig ausgearbeiteten Ansatz, der die einzigartigen Merkmale jedes Betriebs, die spezifischen regulatorischen Anforderungen und die sich entwickelnden Best Practices innerhalb der Branche berücksichtigt. Es gibt jedoch mehrere wichtige Komponenten, die für ein erfolgreiches Inspektionsprogramm unerlässlich sind:
- Umfassende Risikobewertung: Eine gründliche Risikobewertung ist die Grundlage für ein effektives Inspektionsprogramm. Dieser Prozess beinhaltet die Identifizierung potenzieller Gefahren, die Bewertung ihrer Wahrscheinlichkeit und potenziellen Folgen und die entsprechende Priorisierung der Inspektionsaktivitäten.
- Klar definierter Umfang und Häufigkeit der Inspektionen: Auf der Grundlage der Risikobewertung müssen Umfang und Häufigkeit der Inspektionen genau festgelegt werden. Dadurch wird sichergestellt, dass kritische Anlagen, Geräte und Prozesse in angemessenen Abständen überprüft werden, wodurch das Risiko unentdeckter Probleme oder Defekte minimiert wird.
- Qualifiziertes und geschultes Personal: Die Inspektionen müssen von Personal durchgeführt werden, das über die erforderlichen Qualifikationen, Zertifizierungen und Schulungen verfügt. Dies gewährleistet nicht nur die Genauigkeit und Zuverlässigkeit der Inspektionen, sondern fördert auch eine Kultur der Professionalität und Rechenschaftspflicht innerhalb der Organisation.
- Robustes Datenmanagement und Analyse: Effektives Datenmanagement und Analyse sind entscheidend, um wertvolle Erkenntnisse aus Inspektionsdaten zu gewinnen. Dazu gehören der Einsatz fortschrittlicher Software und Tools für die Datenerfassung, Speicherung und Analyse sowie die Implementierung standardisierter Berichts- und Dokumentationsprozesse.
- Kontinuierliche Verbesserung und Anpassung: Die Öl- und Gasindustrie entwickelt sich ständig weiter, und es kommen regelmäßig neue Technologien, Vorschriften und bewährte Verfahren hinzu. Ein effektives Inspektionsprogramm muss flexibel und anpassungsfähig sein und kontinuierliche Verbesserungsmechanismen beinhalten, um seine Relevanz und Wirksamkeit im Laufe der Zeit sicherzustellen.
- Integration mit anderen Sicherheits- und Compliance-Programmen: Inspektionen sollten nicht isoliert durchgeführt werden; sie sollten in andere Sicherheits- und Compliance-Programme innerhalb der Organisation integriert werden, wie z. B. Wartung, Anlagenintegritätsmanagement und Notfallplanung. Dieser ganzheitliche Ansatz gewährleistet ein umfassendes und koordiniertes Bemühen um Risikominderung und betriebliche Exzellenz.
Durch die Integration dieser Schlüsselkomponenten können Öl- und Gasunternehmen Inspektionsprogramme entwickeln und implementieren, die nicht nur die regulatorischen Anforderungen erfüllen, sondern auch proaktiv Risiken erkennen und mindern, die betriebliche Effizienz steigern und eine Kultur der Sicherheit und kontinuierlichen Verbesserung fördern.
Allgemeine Inspektionstechniken und Werkzeuge
Die Öl- und Gasindustrie setzt eine Vielzahl von Inspektionstechniken und -werkzeugen ein, um den sicheren und effizienten Betrieb ihrer Anlagen zu gewährleisten. Diese Techniken und Werkzeuge wurden entwickelt, um spezifische Inspektionsanforderungen zu erfüllen, die von routinemäßigen Wartungsprüfungen bis hin zu fortgeschrittenen diagnostischen Bewertungen reichen. Hier sind einige der in der Branche am häufigsten verwendeten Inspektionstechniken und -werkzeuge:
Tägliche Inspektionsrunden in Öl- und Gasanlagen
Tägliche Inspektionsrunden sind ein grundlegender Aspekt für den sicheren und effizienten Betrieb von Öl- und Gasanlagen. Diese Routinekontrollen werden in der Regel von geschultem Personal durchgeführt, das verschiedene Komponenten, Geräte und Systeme innerhalb der Anlage physisch inspiziert. Zu den Hauptzielen der täglichen Inspektionsrunden gehören:
- Visuelle Inspektionen: Geschultes Personal überprüft Geräte, Rohrleitungen, Ventile und andere Komponenten visuell auf Anzeichen von Verschleiß, Korrosion, Undichtigkeiten oder andere sichtbare Mängel. Dieser praxisorientierte Ansatz ermöglicht die Früherkennung potenzieller Probleme, bevor sie zu schwerwiegenderen Problemen eskalieren.
- Funktionstests: Während der täglichen Kontrollen kann das Personal auch Funktionstests an kritischen Geräten und Systemen durchführen, um sicherzustellen, dass diese innerhalb der angegebenen Parameter arbeiten. Dies kann das Testen von Sicherheitseinrichtungen, Notabsperrventilen und anderen kritischen Komponenten umfassen.
- Schecks beim Reinigungsservice: Bei den täglichen Rundgängen wird auch die allgemeine Sauberkeit und Organisation der Anlage überprüft. Eine ordnungsgemäße Reinigung ist unerlässlich, um ein sicheres Arbeitsumfeld zu gewährleisten und das Risiko von Unfällen oder Zwischenfällen zu minimieren.
- Dokumentation und Berichterstattung: In der Regel werden detaillierte Aufzeichnungen der Inspektionsergebnisse geführt, die eine Trendanalyse und eine proaktive Wartungsplanung ermöglichen. Alle festgestellten Probleme oder Mängel werden umgehend gemeldet und anhand festgelegter Protokolle behoben.
Tägliche Inspektionsrunden sind eine proaktive Maßnahme, mit der potenzielle Probleme erkannt und behoben werden können, bevor sie zu schwerwiegenderen Problemen eskalieren können. Dadurch wird das Risiko ungeplanter Abschaltungen, Unfälle oder Umweltvorfälle minimiert.
Früherkennung von Anomalien zur Vermeidung von Ausfällen
In der Öl- und Gasindustrie können ungeplante Stillstände schwerwiegende Folgen haben, die von Produktions- und Umsatzeinbußen bis hin zu potenziellen Sicherheitsrisiken und Umweltauswirkungen reichen. Die frühzeitige Erkennung von Anomalien ist entscheidend, um solche Abschaltungen zu vermeiden und den kontinuierlichen und sicheren Betrieb der Anlagen zu gewährleisten.
Eine der wichtigsten Techniken zur Früherkennung ist der Einsatz fortschrittlicher Überwachungs- und Sensortechnologien. Zu diesen Technologien können gehören:
- Prädiktive Wartungssysteme: Prädiktive Wartungssysteme nutzen Sensordaten, Algorithmen für maschinelles Lernen und historische Daten, um Muster zu identifizieren und potenzielle Geräteausfälle oder -verschlechterungen vorherzusagen. Durch die frühzeitige Erkennung dieser Anomalien können Wartungsarbeiten proaktiv geplant werden, wodurch ungeplante Abschaltungen vermieden und Ausfallzeiten minimiert werden.
- Zustandsüberwachung: Die Zustandsüberwachung umfasst die kontinuierliche oder regelmäßige Überwachung kritischer Geräte und Systeme zur Bewertung ihres Betriebszustands. Dies kann die Überwachung von Schwingungspegeln, Temperatur, Druck und anderen Parametern umfassen, die auf potenzielle Probleme oder Abweichungen von den normalen Betriebsbedingungen hinweisen können.
- Systeme zur Erkennung von Leckagen: Moderne Lecksuchsysteme wie akustische Sensoren, Infrarotkameras und Gaswarngeräte werden eingesetzt, um Leckagen in Rohrleitungen, Tanks und anderen Infrastrukturen zu identifizieren und zu lokalisieren. Durch die frühzeitige Erkennung von Leckagen kann eine Eskalation zu schwerwiegenderen Vorfällen verhindert und die Umweltbelastung minimiert werden.
- Korrosionsüberwachung: Korrosion ist in der Öl- und Gasindustrie ein großes Problem, da sie die Integrität von Ausrüstung und Infrastruktur gefährden kann. Techniken zur Korrosionsüberwachung wie Ultraschallprüfungen, Radiographie und elektrochemische Verfahren werden zur Erkennung und Überwachung von Korrosionsraten eingesetzt, sodass rechtzeitige Wartungs- und Reparaturmaßnahmen möglich sind.
Durch den Einsatz dieser fortschrittlichen Techniken und Technologien können Öl- und Gasunternehmen Anomalien und potenzielle Probleme in einem frühen Stadium erkennen, was proaktive Interventionen ermöglicht und das Risiko ungeplanter Abschaltungen oder Zwischenfälle minimiert.
Um die Sicherheit der Arbeiter zu gewährleisten (Gaslecks)
Die Gewährleistung der Sicherheit der Arbeitnehmer ist in der Öl- und Gasindustrie, in der die Gefahr von Gaslecks und anderen gefährlichen Zwischenfällen allgegenwärtig ist, von größter Bedeutung. Wirksame Inspektionstechniken und -instrumente spielen eine entscheidende Rolle bei der Identifizierung und Minderung dieser Risiken, beim Schutz des Wohlbefindens des Personals und bei der Aufrechterhaltung einer sicheren Arbeitsumgebung.
Eine der wichtigsten Inspektionstechniken zur Erkennung von Gaslecks ist der Einsatz von Gaswarnsystemen. Bei diesen Systemen werden in der Regel stationäre oder tragbare Gaswarngeräte eingesetzt, die in der Lage sind, verschiedene Gase wie Schwefelwasserstoff, Methan und andere Kohlenwasserstoffe zu erkennen und zu überwachen.
- Stationäre Gaswarnsysteme: Diese Systeme bestehen aus strategisch platzierten Gaswarngeräten in der gesamten Anlage, die eine kontinuierliche Überwachung und Frühwarnung vor Gaslecks ermöglichen. Sie sind häufig in Alarmsysteme und Notfallprotokolle integriert und ermöglichen so ein schnelles und koordiniertes Handeln im Falle eines erkannten Lecks.
- Tragbare Gaswarngeräte: Tragbare Gaswarngeräte sind tragbare Geräte, die bei Inspektionen oder Wartungsarbeiten vom Personal getragen werden können. Diese Geräte ermöglichen eine gezielte Überwachung in bestimmten Bereichen oder engen Räumen und bieten so eine zusätzliche Schutzschicht für die Arbeiter.
Zusätzlich zu den Gaswarnsystemen werden andere Inspektionstechniken und -werkzeuge eingesetzt, um die Sicherheit der Mitarbeiter zu gewährleisten, darunter:
- Infrarotkameras: Infrarotkameras können Gaslecks erkennen und visualisieren, indem sie Temperaturunterschiede oder Muster erkennen, die auf das Vorhandensein von Kohlenwasserstoffen oder anderen Gasen hinweisen könnten.
- Prüfung der Schallemission: Dieses zerstörungsfreie Prüfverfahren kann Leckagen erkennen und lokalisieren, indem es die hochfrequenten Schallwellen analysiert, die durch Gas erzeugt werden, das aus druckbeaufschlagten Systemen oder Komponenten austritt.
- Verfahren für den Zutritt zu engen Räumen: Strenge Verfahren für den Zutritt zu engen Räumen, einschließlich Überwachung der Atmosphäre und Belüftung, werden eingeführt, um die Sicherheit von Arbeitnehmern zu gewährleisten, die enge Räume betreten, in denen das Risiko einer Gasansammlung oder eines Sauerstoffmangels erhöht ist.
- Persönliche Schutzausrüstung (PSA): Den Arbeitnehmern wird je nach den spezifischen Gefahren und Risiken, die mit ihren Aufgaben verbunden sind, geeignete Schutzausrüstung wie gasdichte Schutzanzüge, in sich geschlossene Atemschutzgeräte und andere Spezialausrüstungen zur Verfügung gestellt.
Durch den Einsatz dieser Inspektionstechniken und -instrumente können Öl- und Gasunternehmen proaktiv Gasleckrisiken erkennen und mindern, wodurch eine sicherere Arbeitsumgebung für ihr Personal geschaffen und das Risiko von Zwischenfällen minimiert wird, die Menschenleben gefährden oder die Betriebsintegrität gefährden könnten.
Die Rolle der Technologie bei modernen Öl- und Gasinspektionen
In der sich ständig weiterentwickelnden Landschaft der Öl- und Gasindustrie hat sich die Technologie als wegweisend erwiesen und die Art und Weise, wie Inspektionen durchgeführt werden, revolutioniert. Traditionelle Methoden sind zwar immer noch wertvoll, werden jedoch erweitert und in einigen Fällen durch modernste technologische Lösungen ersetzt, die ein beispielloses Maß an Effizienz, Genauigkeit und Sicherheit bieten.
KI-gestützte Roboterinspektion
Künstliche Intelligenz (KI) und Robotik haben eine neue Ära der Inspektionsmöglichkeiten in der Öl- und Gasindustrie eingeleitet. KI-gestützte robotische Inspektionssysteme können sich selbst in den anspruchsvollsten und gefährlichsten Umgebungen zurechtfinden und diese inspizieren, wodurch der Bedarf an menschlichem Eingreifen minimiert und das Risiko von Unfällen oder Verletzungen verringert wird.
Diese fortschrittlichen Robotersysteme sind mit einer Reihe von Sensoren, Kameras und anderen Spezialgeräten ausgestattet, die eine umfassende Datenerfassung und -analyse ermöglichen. Durch den Einsatz von Algorithmen für maschinelles Lernen und Computer-Vision-Technologien können diese Systeme Defekte, Anomalien und potenzielle Probleme mit bemerkenswerter Genauigkeit und Geschwindigkeit erkennen und identifizieren.
Einer der Hauptvorteile der KI-gestützten Roboterinspektion ist die Fähigkeit, Bereiche zu erreichen und zu inspizieren, die für menschliche Inspektoren schwer oder unmöglich sicher zu erreichen sind. Dazu gehören enge Räume, erhöhte Bauwerke und gefährliche Umgebungen, in denen das Vorhandensein giftiger Gase oder extreme Temperaturen ein erhebliches Risiko für das menschliche Personal darstellen würden.
Darüber hinaus können robotische Inspektionssysteme kontinuierlich arbeiten, wodurch die Notwendigkeit von Abschaltungen oder Betriebsunterbrechungen minimiert wird. Dies erhöht nicht nur die Produktivität und Effizienz, sondern reduziert auch das Risiko ungeplanter Ausfallzeiten und der damit verbundenen finanziellen Verluste.
Inspektionen von Öltanks aus der Luft
Inspektionen aus der Luft sind zu einem festen Bestandteil der Öl- und Gasindustrie geworden und bieten ein umfassendes und effizientes Mittel zur Überwachung und Inspektion riesiger Infrastrukturbereiche wie Pipelines, Bohrlöcher und Lagertanks. Fortschrittliche Drohnentechnologie, gepaart mit hochauflösenden Kameras und speziellen Sensoren, hat diesen Inspektionsansatz revolutioniert.
Unbemannte Luftfahrzeuge (UAVs) oder Drohnen können große Gebiete schnell und sicher abdecken und detaillierte visuelle Daten und Sensorwerte erfassen, die auf potenzielle Probleme oder Anomalien hin analysiert werden können. Dies erhöht nicht nur die Effizienz der Inspektionen, sondern minimiert auch das Risiko für das Personal, das diese Bereiche sonst physisch betreten müsste.
Inspektionen aus der Luft können eine Vielzahl von Problemen erkennen, darunter Leckagen, Korrosion, Strukturdefekte und Eingriffe in die Vegetation. Durch den Einsatz von Wärmebildkameras, Gaswarnsensoren und anderen Spezialgeräten können Drohnen eine umfassende Bewertung des Zustands und der Integrität von Öl- und Gasanlagen durchführen.
Darüber hinaus können die bei Drohneninspektionen gesammelten Daten in fortschrittliche Analysen und Algorithmen für maschinelles Lernen integriert werden, was eine vorausschauende Wartung und proaktive Entscheidungsfindung ermöglicht. Dieser datengestützte Ansatz ermöglicht eine effizientere Ressourcenallokation, optimierte Wartungspläne und ein verbessertes allgemeines Anlagenmanagement.
Frühe Erkennung von Gaslecks
Die Früherkennung von Gaslecks ist ein kritisches Sicherheits- und Umweltproblem in der Öl- und Gasindustrie. Herkömmliche Methoden der Lecksuche, wie manuelle Inspektionen oder stationäre Sensoren, können zeitaufwändig, arbeitsintensiv und in ihrer Reichweite begrenzt sein. Moderne Technologien revolutionieren jedoch die Art und Weise, wie Gaslecks erkannt und behoben werden.
Eine der vielversprechendsten Technologien in diesem Bereich ist der Einsatz fortschrittlicher Gaswarnsensoren und -systeme. Diese Sensoren können in verschiedenen Konfigurationen eingesetzt werden, einschließlich fester Installationen, mobiler Plattformen und sogar Flugdrohnen. Durch den Einsatz modernster Sensortechnologien wie Infrarot-, Laser- oder elektrochemischer Sensoren können diese Systeme Gaslecks mit hoher Genauigkeit und Empfindlichkeit erkennen und lokalisieren.
Darüber hinaus werden fortschrittliche Datenanalysen und Algorithmen für maschinelles Lernen in diese Sensorsysteme integriert, was Echtzeitüberwachung, Mustererkennung und prädiktive Analysen ermöglicht. Dies ermöglicht eine proaktive Identifizierung potenzieller Leckquellen, was zeitnahe Interventionen ermöglicht und das Risiko größerer Vorfälle minimiert.
Ein weiterer innovativer Ansatz zur Früherkennung von Gaslecks ist der Einsatz hyperspektraler Bildgebungstechnologie. Diese Technologie kombiniert hochauflösende Bildgebung mit spektroskopischer Analyse und ermöglicht so die Erkennung und Identifizierung von Gaswolken und Gaslecks anhand ihrer einzigartigen spektralen Signaturen. Hyperspektrale Bildgebung kann von Flugplattformen wie Drohnen oder Flugzeugen aus eingesetzt werden und bietet eine umfassende und effiziente Möglichkeit, große Bereiche auf potenzielle Leckagen zu untersuchen.
Durch den Einsatz dieser Spitzentechnologien kann die Öl- und Gasindustrie ihre Fähigkeit, Gaslecks frühzeitig zu erkennen und zu beheben, die Umweltbelastung zu minimieren, die Sicherheit der Mitarbeiter zu gewährleisten und die Betriebsintegrität aufrechtzuerhalten, erheblich verbessern.
Überwachen Sie analoge Messgeräte
In der Öl- und Gasindustrie werden analoge Messgeräte nach wie vor häufig zur Überwachung von Parametern wie Druck, Temperatur und Durchflussraten verwendet. Obwohl diese Messgeräte zuverlässig sind, kann die manuelle Datenerfassung zu Problemen wie menschlichem Versagen und eingeschränkter Zugänglichkeit in gefährlichen oder abgelegenen Bereichen führen. Um diese Probleme zu lösen, revolutionieren mit KI ausgestattete Roboter die Art und Weise, wie analoge Messgeräte überwacht werden. Diese Roboter verwenden fortschrittliche Algorithmen für maschinelles Sehen und maschinelles Lernen, um die Daten von analogen Messgeräten autonom zu lesen und zu interpretieren. Durch den Einsatz einer KI-gestützten optischen Erkennung können die Roboter Messwerte ohne menschliches Eingreifen präzise erfassen, wodurch manuelle Dateneingabefehler vermieden werden.
Darüber hinaus können KI-gestützte Roboter an gefährlichen oder schwer zugänglichen Orten operieren, Echtzeitdaten sammeln und zur Fernanalyse übertragen. Dies erhöht nicht nur die Sicherheit, da die Anwesenheit von Menschen in gefährlichen Umgebungen reduziert wird, sondern erhöht auch die Effizienz und Präzision der Datenerfassung. Darüber hinaus können einige Robotersysteme in Augmented-Reality-Tools (AR) integriert werden, sodass das Personal in Echtzeit Messdaten visualisieren kann, die in seiner Umgebung eingeblendet sind. Diese AR-Systeme können in Kombination mit KI Warnmeldungen ausgeben, wenn die Messwerte von den sicheren Parametern abweichen, sodass zeitnahe Interventionen möglich sind und Geräteausfälle vermieden werden können. Durch die Integration von KI-gesteuerten Robotern in ihren Betrieb kann die Öl- und Gasindustrie die Überwachung analoger Messgeräte modernisieren und so für mehr Sicherheit, Datengenauigkeit und Betriebseffizienz sorgen.
Ein weiterer innovativer Ansatz zur Überwachung analoger Messgeräte ist der Einsatz von Augmented-Reality-Technologien (AR). AR-Systeme können die physische Welt mit digitalen Informationen und Visualisierungen überlagern, sodass das Personal Messwerte und andere relevante Daten in Echtzeit direkt über seine AR-Geräte einsehen kann.
Diese AR-Systeme können auch prädiktive Analysen und Algorithmen für maschinelles Lernen enthalten und in Echtzeit Warnmeldungen und Benachrichtigungen bereitstellen, wenn die Messwerte von den erwarteten Normen abweichen oder sich kritischen Schwellenwerten nähern. Dieser proaktive Ansatz ermöglicht zeitnahe Interventionen und Wartungsarbeiten und minimiert so das Risiko von Geräteausfällen oder Betriebsstörungen.
Durch die Nutzung dieser Spitzentechnologien kann die Öl- und Gasindustrie ihren Ansatz zur Überwachung analoger Messgeräte modernisieren, die Sicherheit erhöhen, die Datengenauigkeit verbessern und effizientere und effektivere Entscheidungsprozesse ermöglichen.
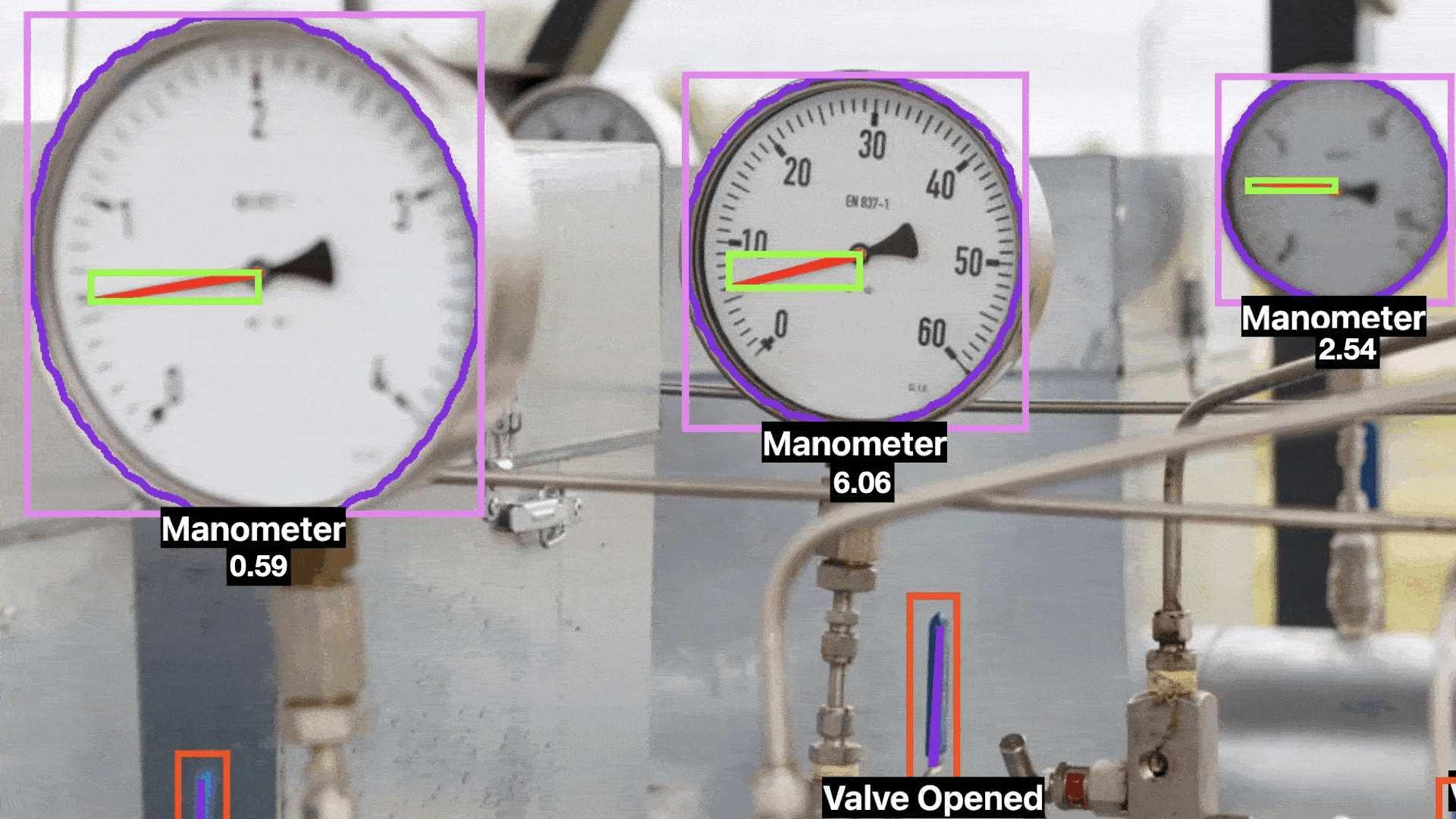
Operator in Ausnahmefällen
Inspektionen, bei denen das Personal Öl- und Gasanlagen manuell überwacht, sind unerlässlich, um einen sicheren und effizienten Betrieb zu gewährleisten. Herkömmliche Rundgänge können jedoch zeitaufwändig sein, sich wiederholen und die Arbeiter gefährlichen Umgebungen aussetzen. Um diesen Problemen zu begegnen, hat das Konzept der „in Ausnahmefällen“ an Bedeutung gewonnen, wobei Drohnen und autonome Roboter eine zentrale Rolle bei der Transformation dieses Prozesses spielen.
Drohnen und Roboter, die mit fortschrittlichen Sensoren und Kameras ausgestattet sind, können autonom durch Einrichtungen navigieren, um Geräte zu überwachen, Inspektionen durchzuführen und Anomalien zu erkennen. Diese Maschinen sammeln kontinuierlich Daten über Betriebsbedingungen wie Druck, Temperatur und Umweltfaktoren und senden sie in Echtzeit zur Analyse. Mithilfe künstlicher Intelligenz und maschinellem Lernen werden die Daten verarbeitet, um Abweichungen von den normalen Bedingungen zu erkennen und Warnmeldungen auszulösen, sodass das Bedienpersonal nur dann eingreifen kann, wenn dies erforderlich ist.
Diese Umstellung auf Drohnen und Roboter als wichtige Inspektionswerkzeuge erhöht nicht nur die Effizienz, da weniger routinemäßige manuelle Inspektionen erforderlich sind, sondern verbessert auch die Sicherheit der Mitarbeiter erheblich, da die Exposition gegenüber Gefahrenbereichen minimiert wird. Darüber hinaus verbessern die Präzision und Konsistenz der von diesen autonomen Systemen gesammelten Daten die Genauigkeit und reduzieren menschliche Fehler bei der Meldung von Gerätezuständen. In Kombination mit digitalen Zwillingen oder virtuellen Modellen der Anlage bieten Drohnen und Roboter den Bedienern einen umfassenden Überblick über die Anlage in Echtzeit. Dies ermöglicht fundiertere Entscheidungen, eine proaktive Wartung und eine bessere Ressourcenzuweisung.
Indem die Öl- und Gasindustrie in Ausnahmefällen Drohnen und Roboter in Inspektionsrunden einsetzt, kann sie bei der Anlagenüberwachung einen sichereren, effizienteren und datengestützten Ansatz verfolgen, der letztlich die Leistung optimiert und Risiken minimiert.
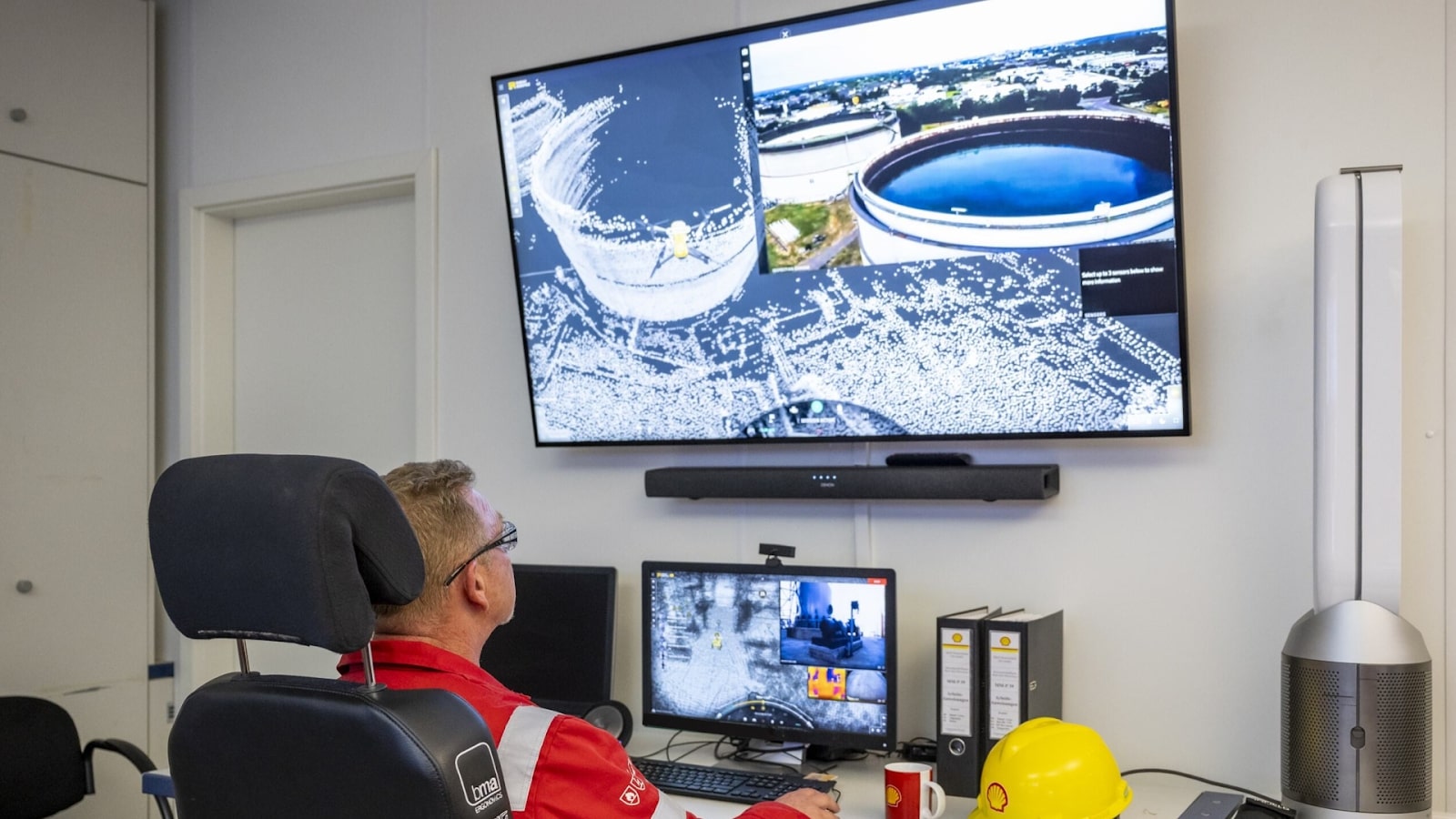
Wärmebilder
Die Wärmebildtechnologie ist in der Öl- und Gasindustrie zu einem unverzichtbaren Instrument geworden und bietet eine nichtinvasive, effiziente Methode zur Inspektion und Überwachung verschiedener Anlagen und Prozesse. Durch die Erkennung und Visualisierung von Temperaturunterschieden enthüllen Wärmebildkameras wichtige Informationen, die mit bloßem Auge möglicherweise nicht sichtbar sind.
Eine wichtige Anwendung der Wärmebildgebung ist die Erkennung von Lecks und Isolationsdefekten. Kohlenwasserstoffe und andere Gase weisen im Vergleich zu ihrer Umgebung häufig Temperaturschwankungen auf, sodass sie mit Wärmebildern nachweisbar sind. Diese Technologie ermöglicht die schnelle und präzise Identifizierung von Lecks in Rohrleitungen, Lagertanks und anderen Geräten, was zeitnahe Reparaturen ermöglicht und Umwelt- und Sicherheitsrisiken minimiert.
Neben der Lecksuche ist die Wärmebildgebung für die Überwachung elektrischer und mechanischer Geräte unerlässlich. Abnormale Temperaturmuster können auf Probleme wie Überhitzung von Komponenten, Lagerausfälle oder elektrische Störungen hinweisen. Wenn diese frühzeitig erkannt werden, können kostspielige Abschaltungen verhindert, die Lebensdauer der Geräte verlängert und die allgemeinen Wartungskosten gesenkt werden.
Die Wärmebildgebung spielt auch eine wichtige Rolle bei der Erhöhung der Arbeitssicherheit, indem sie potenzielle Gefahren wie heiße Oberflächen oder Gaslecks erkennt. Diese Frühwarnungen ermöglichen es dem Personal, geeignete Sicherheitsmaßnahmen zu ergreifen oder bei Bedarf zu evakuieren, wodurch das Unfallrisiko verringert wird.
Die Integration der Wärmebildgebung mit fortschrittlichen Technologien wie Drohnen und Robotern hat Inspektionen revolutioniert. Roboter, die mit KI-gesteuerter thermografischer Analyse ausgestattet sind, wie sie von Energy Robotics entwickelt wurden, können Temperaturanomalien autonom in Echtzeit erkennen und interpretieren. Diese Roboter führen präzise thermische Inspektionen von Rohrleitungen, elektrischen Systemen und Maschinen durch und erkennen Unregelmäßigkeiten, die auf potenzielle Fehler hinweisen. Diese Integration ermöglicht es Robotern, gefährliche oder schwer zugängliche Bereiche zu erreichen, thermische Daten zu erfassen, ohne menschliche Mitarbeiter zu gefährden, und bietet eine kontinuierliche Überwachung mit erhöhter Genauigkeit.
Da Sicherheit, Effizienz und ökologische Nachhaltigkeit in der Öl- und Gasindustrie nach wie vor oberste Priorität haben, wird die Wärmebildgebung, insbesondere in Kombination mit KI-gesteuerten Roboterinspektionen, weiterhin ein wichtiges Instrument sein. Sie ermöglicht eine proaktive Wartung, eine effektive Lecksuche und ein besseres Situationsbewusstsein und trägt so zu einem sichereren und effizienteren Betrieb bei.
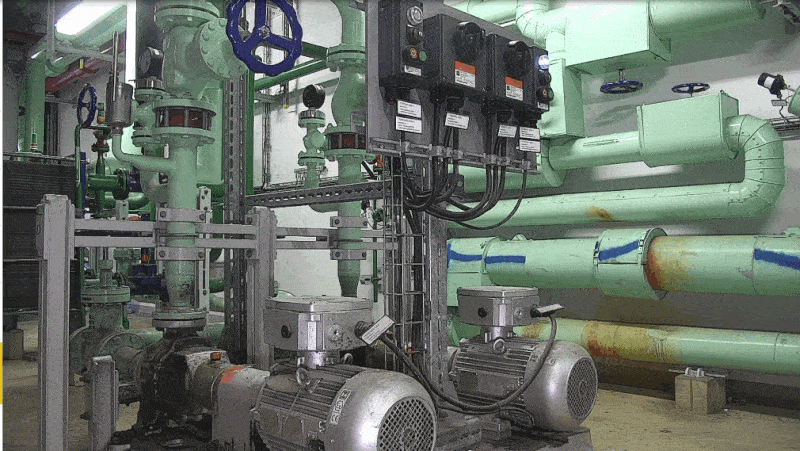
Inspektion in Bereichen der ATEX/IECEx Zone 1
In der Öl- und Gasindustrie wird häufig in Gefahrenbereichen gearbeitet, in denen das Vorhandensein brennbarer Gase oder Dämpfe die Gefahr von Explosionen birgt. Diese Bereiche sind nach internationalen Normen wie ATEX (Atmosphere Explosible) in Europa und IECEx (International Electrotechnical Commission System for Certification to Standards Relating on Equipment for Use in explosionsgefährdeten Bereichen) weltweit klassifiziert.
Bereiche der Zone 1, wie sie in diesen Normen definiert sind, sind Orte, an denen im Normalbetrieb mit einer explosiven Gasatmosphäre zu rechnen ist. Für die Durchführung von Inspektions- und Wartungsarbeiten in diesen Umgebungen mit hohem Risiko sind spezielle Geräte und Verfahren erforderlich, um die Sicherheit des Personals zu gewährleisten und potenzielle Zündquellen zu vermeiden.
Um dieser Herausforderung zu begegnen, hat die Öl- und Gasindustrie fortschrittliche Technologien und Inspektionsmethoden eingeführt, die speziell für den Einsatz in ATEX/IECEx-Bereichen der Zone 1 entwickelt wurden. Eine dieser Technologien ist der Einsatz eigensicherer Geräte (IS), die so konzipiert sind, dass die für die Zündung verfügbare Energiemenge begrenzt wird, selbst wenn brennbare Gase oder Dämpfe vorhanden sind.
Eigensichere Kameras, Sensoren und andere Inspektionswerkzeuge ermöglichen es dem Personal, visuelle Inspektionen sicher durchzuführen, Daten zu sammeln und den Zustand der Ausrüstung zu überwachen, ohne potenzielle Zündquellen einzuführen. Diese Werkzeuge wurden strengen Tests unterzogen und sind zertifiziert, um die strengen Sicherheitsanforderungen für den Einsatz in gefährlichen Umgebungen zu erfüllen.
Ein weiterer Ansatz zur Inspektion von ATEX/IECEx-Zone-1-Bereichen ist der Einsatz von ferngesteuerten Fahrzeugen (ROVs) oder Robotern. Diese unbemannten Systeme können mit verschiedenen Sensoren, Kameras und anderen Inspektionswerkzeugen ausgestattet werden, sodass eine umfassende Datenerfassung und Überwachung möglich ist, ohne dass das Personal einer gefährlichen Umgebung ausgesetzt wird.
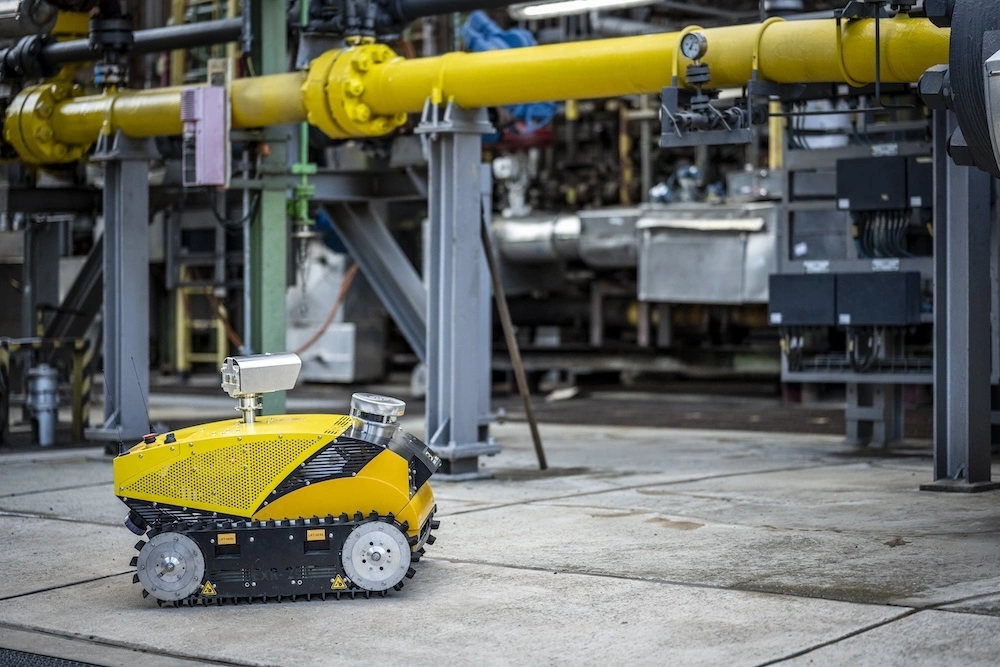
Fortschrittliche Robotik- und Automatisierungstechnologien werden auch zur Durchführung von Wartungs- und Reparaturarbeiten in Bereichen der Zone 1 eingesetzt, wodurch der Bedarf an menschlichem Eingreifen weiter minimiert und die damit verbundenen Risiken verringert werden.
Darüber hinaus nutzt die Öl- und Gasindustrie fortschrittliche Simulations- und digitale Zwillingstechnologien, um virtuelle Darstellungen von Gefahrenbereichen zu erstellen. Diese digitalen Modelle können zu Schulungszwecken verwendet werden und ermöglichen es dem Personal, Inspektions- und Wartungsverfahren in einer sicheren, simulierten Umgebung zu üben und sich mit ihnen vertraut zu machen, bevor es den tatsächlichen Gefahrenbereich betritt.
Durch den Einsatz dieser Spitzentechnologien und Inspektionsmethoden kann die Öl- und Gasindustrie ein hohes Maß an betrieblicher Exzellenz aufrechterhalten und gleichzeitig der Sicherheit des Personals Priorität einräumen und strenge behördliche Standards für den Betrieb in Gefahrenbereichen einhalten.
Fazit
Während wir uns in der sich ständig weiterentwickelnden Landschaft der Öl- und Gasindustrie zurechtfinden, kann die entscheidende Rolle von Inspektionen nicht genug betont werden. Von der Sicherstellung der Einhaltung gesetzlicher Vorschriften und der betrieblichen Integrität bis hin zum Schutz des Wohlbefindens unserer Mitarbeiter und der Umwelt — Inspektionen sind der Eckpfeiler, auf dem der Erfolg unserer Branche basiert.
In diesem Artikel haben wir die verschiedenen Facetten von Inspektionen untersucht und uns mit ihrer Bedeutung, den regulatorischen Anforderungen und der Vielzahl der verwendeten Techniken und Instrumente befasst. Wir haben miterlebt, wie die Technologie den Inspektionsprozess revolutioniert hat und innovative Lösungen eingeführt hat, die Effizienz, Genauigkeit und Sicherheit verbessern.
Es ist jedoch wichtig zu erkennen, dass Inspektionen nicht nur eine Checkliste mit Aufgaben oder ein Kästchen sind, das angekreuzt werden muss. Sie sind Ausdruck unseres unerschütterlichen Engagements für Spitzenleistungen, ein Beweis für unser Engagement für die Einhaltung höchster Standards der betrieblichen Integrität und ein Ausdruck unseres Respekts für das Vertrauen, das uns von Interessengruppen, Gemeinden und der breiten Öffentlichkeit entgegengebracht wird.
Mit Blick auf die Zukunft muss die Öl- und Gasindustrie weiterhin Innovationen fördern und sich an die sich ständig ändernde Technologielandschaft anpassen. Wir müssen in unserem Streben nach Sicherheit, Umweltschutz und betrieblicher Exzellenz wachsam, proaktiv und kompromisslos bleiben.
Ich hoffe aufrichtig, dass dieser Artikel nicht nur wertvolle Einblicke in die Welt der Öl- und Gasinspektionen gegeben hat, sondern auch ein Gefühl der Leidenschaft und Wertschätzung für die entscheidende Rolle geweckt hat, die sie bei der Gestaltung des Erfolgs und der Nachhaltigkeit unserer Branche spielen.