Was sind Inspektionsrunden?
Inspektionsrunden, auch bekannt als Feld-Operator-Runden oder Anlagen-Runden, Routineinspektionen und Überwachungstätigkeiten, die von Betreibern in Industrieanlagen, wie z. B. Produktionsstätten, Raffinerien oder Energieerzeugungsanlagen, durchgeführt werden. Sie sind wichtig, um den sicheren und effizienten Betrieb der Anlagen zu gewährleisten, potenzielle Probleme zu erkennen und die Gesamtintegrität der Anlage zu erhalten.
Während der Inspektionsrunden inspizieren die Operatoren physisch verschiedene Bereiche der Anlage, überprüfen den Status der Ausrüstung, überwachen die Messwerte der Instrumente und beobachten alle Anomalien oder Abweichungen von den normalen Betriebsbedingungen. Diese Rundgänge werden in der Regel in regelmäßigen Abständen durchgeführt und folgen vordefinierten Routen und Checklisten.
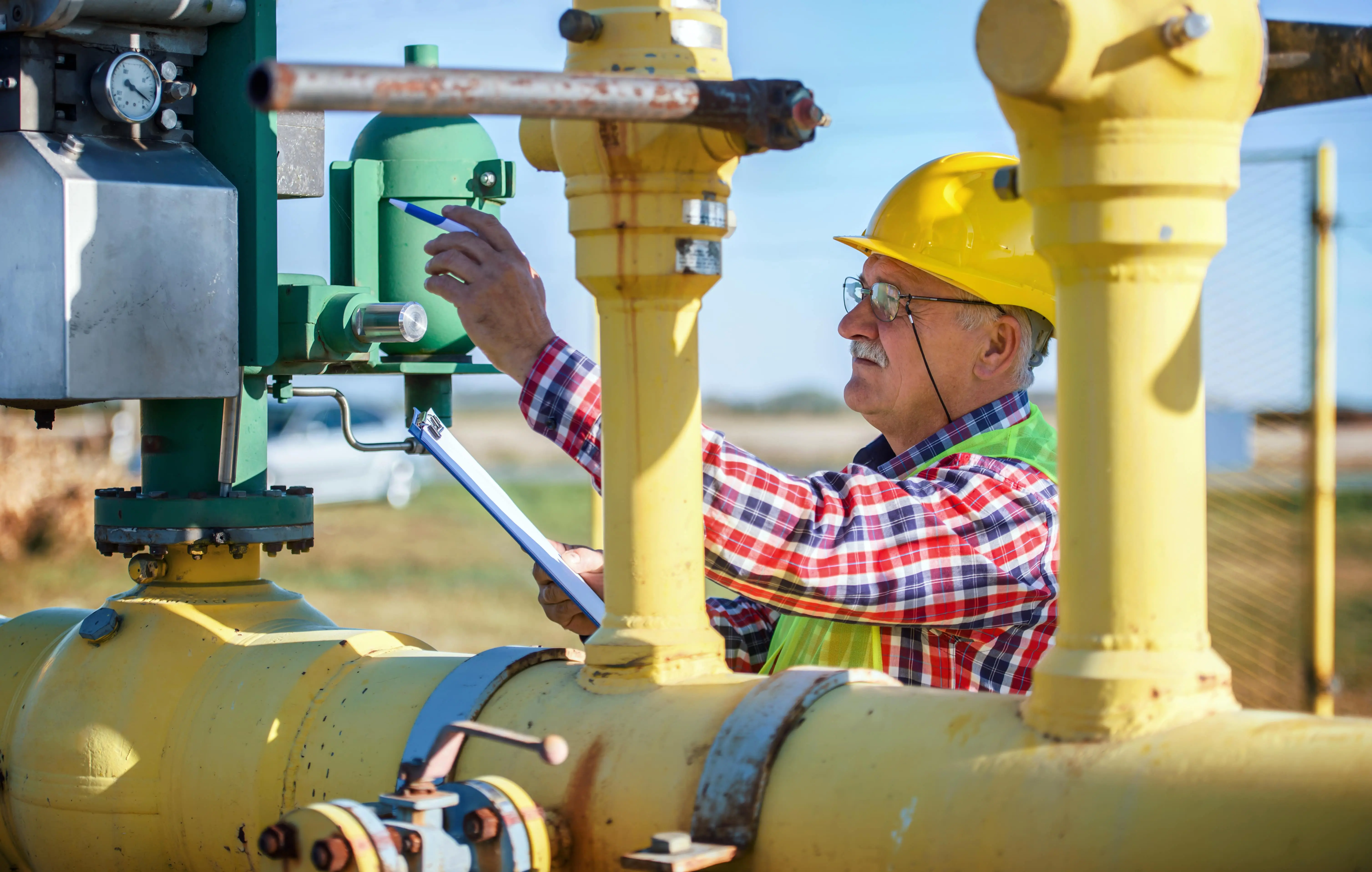
Wie wird eine Operator-Runde durchgeführt?
Traditionell werden Bedienerrunden manuell durchgeführt, wobei die Bediener physisch durch die Anlage gehen, die Geräte visuell inspizieren und ihre Beobachtungen auf Papier oder Handheld-Geräten festhalten. Der Prozess umfasst in der Regel die folgenden Schritte:
Routenplanung: Den Bedienern werden bestimmte Routen oder Bereiche zugewiesen, die sie bei ihren Rundgängen ablaufen müssen, um eine umfassende Abdeckung der Anlage zu gewährleisten.
Überprüfung der Checkliste: Vor Beginn des Rundgangs lesen die Bediener die entsprechenden Checklisten oder Inspektionsformulare durch, um sicherzustellen, dass sie die zu inspizierenden Punkte und die Kriterien für die Bewertung verstehen.
Inspektion der Ausrüstung: Die Bediener inspizieren die ihnen zugewiesene Ausrüstung physisch und überprüfen sie auf Anzeichen von Verschleiß, Lecks, abnormalen Temperaturen oder anderen möglichen Problemen.
Datenerfassung: Die Bediener zeichnen verschiedene Parameter wie Temperatur, Druck, Durchflussraten oder andere relevante Messwerte entweder manuell oder mit Handgeräten auf.
Protokollierung von Beobachtungen: Alle Beobachtungen, Anomalien oder potenziellen Probleme werden für weitere Untersuchungen oder Abhilfemaßnahmen dokumentiert.
Kommunikation und Berichterstattung: Nach Abschluss des Rundgangs teilen die Bediener ihre Ergebnisse den Vorgesetzten oder dem zuständigen Personal mit, und es werden formelle Berichte zur Dokumentation und für Folgemaßnahmen erstellt.
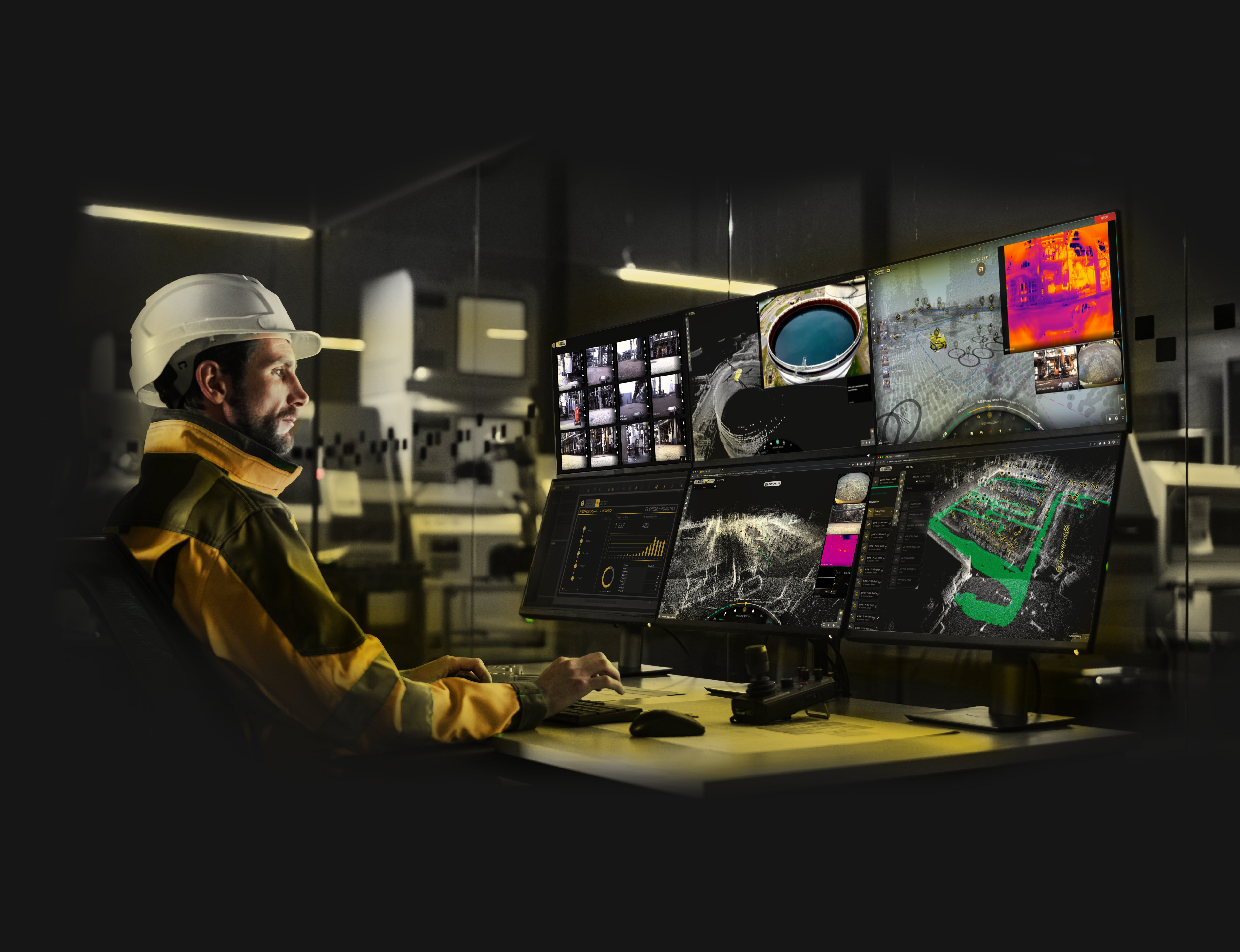
Inspektionsrunden auf Abruf
ist ein innovativer Ansatz für die Inspektion von Industrieanlagen, der die Effizienz und die Ressourcenzuweisung optimiert. Diese Methode weicht von den traditionellen zeitbasierten Inspektionsroutinen ab, indem sie sich auf Bereiche konzentriert, die sofortige Aufmerksamkeit erfordern. Bei diesem System führen die Bediener die Rundgänge auf der Grundlage von Echtzeitdaten und vordefinierten Auslösern durch, anstatt einem festen Zeitplan zu folgen.
Bei diesem Verfahren werden Roboter und Drohnen eingesetzt, um mehrmals täglich automatisierte Inspektionsrunden durchzuführen und qualitativ hochwertige Daten von allen relevanten Anlagen zu erfassen. Weichen die Werte vom Normalbereich ab, werden Warnungen generiert und gezielte Inspektionen veranlasst. Auf diese Weise können die Bediener kritische Probleme priorisieren und ihre Zeit effektiv einteilen.
Die Einführung von Bedienerrunden nach Ausnahmen bietet mehrere Vorteile:
1. Minimierung von Ausfallzeiten: Dieser Ansatz nutzt Echtzeitdaten und Überwachungssysteme, um die Aufmerksamkeit des Bedienpersonals auf potenzielle Probleme zu lenken, die ein sofortiges Eingreifen erfordern, um unnötige Störungen zu vermeiden und einen reibungslosen Betriebsablauf mit minimalen Unterbrechungen zu gewährleisten.
2. Eliminiert Abschaltungen: Ungeplante Abschaltungen können verhindert werden, indem Probleme erkannt und behoben werden, bevor sie eskalieren - mit Hilfe von rechtzeitigen Warnmeldungen und KI-gesteuerten Erkenntnissen von Robotern und Drohnen. Dieser Ansatz priorisiert proaktive Problemlösungen anstelle von reaktiven Maßnahmen, was zu einer erhöhten Zuverlässigkeit der Anlagen und einer kontinuierlichen Produktion führt
3. Gesteigerte Effizienz: Weniger unnötige Inspektionen von gut funktionierenden Geräten
4. Verbesserte Sicherheit: Ermöglicht eine schnellere Reaktion auf potenzielle Gefahren und erhöht die Sicherheit des Personals, da ein Bediener die Anlage seltener betreten muss.
5. Höhere Arbeitszufriedenheit: Die Bediener sind von den ermüdenden täglichen Kontrollgängen befreit und werden nur in Ausnahmesituationen gerufen, wenn die Roboter eine Anomalie entdeckt haben.
6. Kosteneffizienz: Optimiert die Arbeitsauslastung und reduziert Ausfallzeiten.
7. Erhöhte Verlässlichkeit: Konzentriert die Aufmerksamkeit auf die Bereiche, die sie am meisten benötigen.
8. Lücken im Personalbestand schließen: Der Einsatz von Robotern für regelmäßige tägliche Inspektionsrunden ermöglicht es Anlagenbesitzern, Personallücken in der drohenden demografischen Krise zu schließen.
Mit diesem Ansatz können Industrieanlagen ihre Inspektionsprozesse erheblich verbessern und so einen sichereren und effizienteren Betrieb bei maximaler Ressourcennutzung gewährleisten.
Ermöglichung von Inspektionsrunden auf Abruf
Die End-to-End-Inspektionslösung von Energy Robotics ermöglicht es Anlagenbesitzern, tägliche Inspektionsrunden durch eine Flotte von verschiedenen Robotern und Drohnen zu automatisieren. Die Betreiber können über die Energy Robotics-Benutzeroberfläche automatisierte Inspektionsrunden auf Abruf durchführen und erhalten in Echtzeit Einblicke und Warnmeldungen aus der Anlage, ohne den Komfort ihres Kontrollraums verlassen zu müssen. Die von den Robotern und Drohnen gesammelten Daten werden mit fortschrittlichen Anwendungen der künstlichen Intelligenz (KI) verarbeitet, um den Bedienern Einblicke zu geben. Nur im Falle eines Alarms muss ein Bediener ausnahmsweise einen Kontrollgang durchführen und proaktiv handeln, um potenzielle Ausfallzeiten zu minimieren und Abschaltungen zu vermeiden.
Durch den Einsatz einer Flotte von verschiedenen Robotern und Drohnen können Anlagenbesitzer eine 360°-Überwachung ihrer Einrichtungen rund um die Uhr erreichen, sowohl vom Land als auch aus der Luft, und gleichzeitig die Betriebskosten senken und die Sicherheit und Zufriedenheit der Mitarbeiter verbessern.