Turnaround time in the industrial sector has long been a critical challenge, impacting productivity, profitability, and overall operational efficiency. Understanding and managing turnaround time becomes increasingly essential as industries evolve and integrate more advanced technologies. This blog article delves into the multifaceted nature of turnaround time in the industrial sector, exploring its causes, consequences, and mitigation strategies.
Furthermore, we will examine the future trends poised to reshape the industrial landscape, profoundly influencing how turnaround time is perceived and addressed. From cost-prohibitive Internet of Things (IoT) devices to cost-effective implementation of predictive maintenance through robotic inspection, these emerging trends promise to revolutionize turnaround time management. By staying abreast of these developments, businesses can minimize disruptions and create more resilient and responsive operations. Join us as we navigate through the complexities of turnaround time and uncover the transformative future trends that are set to redefine the industrial sector.
What Is Turnaround Time? What Is Downtime?
In the realm of business operations, two critical concepts are inextricably linked: turnaround time (TAT) and downtime. To comprehend their significance, let us first define them.
Turnaround Time (TAT) refers to the duration required to complete a specific task or process, from start to finish. It encompasses the entire cycle, including any necessary preparation, execution, and post-processing activities.
Downtime, on the other hand, represents the period during which a system, equipment, or operation is unavailable or non-functional, resulting in a temporary halt in productivity.
Understanding these concepts is crucial for optimizing operational efficiency, minimizing disruptions, and maximizing profitability across various industries.
What Does Turnaround Time Mean?
Turnaround time is a multifaceted concept that holds different connotations depending on the context in which it is applied. In essence, it represents the time elapsed between the initiation of a request or process and its successful completion or delivery.
For instance, turnaround time in the oil and gas industry indicates the duration when a facility, like a refinery or processing plant, undergoes planned downtime for maintenance, inspections, enhancements, or repairs. This period is vital for maintaining operational safety, efficiency, and reliability. The objective is to execute all required tasks within a predetermined time frame, minimizing production interruptions and swiftly resuming operations. Industry leaders leverage cutting-edge technologies and innovative strategies to optimize these critical periods, ensuring maximum productivity and minimal downtime in this high-stakes sector.
Regardless of the specific application, turnaround time serves as a critical performance metric, providing insights into the efficiency and effectiveness of operations. Minimizing turnaround times can lead to improved customer satisfaction, increased productivity, and a competitive edge in the market.
Importance of Turnaround Time
The significance of turnaround time cannot be overstated, as it influences various aspects of a business's operations and success. Here are some key reasons why turnaround time is crucial:
- Operational Efficiency: Monitoring and optimizing turnaround times can reveal bottlenecks, inefficiencies, or areas for improvement within processes. By addressing these issues, organizations can streamline operations, reduce waste, and enhance overall productivity.
- Cost Savings: Prolonged turnaround times often result in increased costs due to factors such as inventory holding, resource allocation, and potential penalties or lost opportunities. By minimizing turnaround times, businesses can reduce these associated costs and improve profitability.
- Competitive Advantage: In highly competitive markets, the ability to deliver products or services faster than competitors can provide a significant edge. Shorter turnaround times can differentiate a business and attract customers seeking swift and reliable solutions.
- Resource Utilization: Efficient turnaround times enable better utilization of resources, including personnel, equipment, and materials. This optimization can lead to increased capacity, reduced downtime, and improved overall resource management.
- Customer Satisfaction: In today's fast-paced world, customers expect prompt and efficient service. Shorter turnaround times translate into quicker responses, faster delivery of products or services, and ultimately, higher customer satisfaction levels.
Turnaround Time Formula
While the specific formula for calculating turnaround time may vary based on the industry or process, a general turnaround time formula can be expressed as follows:
Turnaround Time = Completion Time - Arrival Time
Here, the "Arrival Time" represents the moment when a request or process is initiated, and the "Completion Time" signifies the completion or delivery of the desired outcome.
It's important to note that the start and end points may differ depending on the context. For example, in manufacturing, the start time could be when raw materials are received, and the end time could be when the finished products are shipped. In customer service, the start time might be when a support ticket is created, and the end time could be when the issue is resolved and communicated to the customer.
By consistently measuring and monitoring turnaround times using this formula, organizations can establish benchmarks, identify areas for improvement, and track progress over time.
Types of Turnaround Time
Turnaround time can be categorized into various types, each serving a specific purpose and providing insights into different aspects of operations. Here are some common types of turnaround time:
Turnaround Time in Oil and Gas: Turnaround time in the oil and gas industry is a critical factor that significantly impacts operational efficiency and profitability. This term refers to the period required to complete maintenance, inspection, and repair activities on industrial plants, such as refineries and petrochemical facilities. Minimizing turnaround time is essential to ensure that production downtime is reduced, thereby maximizing output and revenue.
Effective planning, meticulous scheduling, and the deployment of advanced technologies like AI-driven robotic inspection are pivotal in achieving shorter turnaround times. Additionally, a well-coordinated approach involving skilled personnel, adequate resources, and stringent safety protocols can further enhance the efficiency of these operations. Continuous monitoring and evaluation of past turnarounds help in identifying areas for improvement, ultimately leading to more streamlined and cost-effective processes. Consequently, optimizing turnaround time remains a top priority for stakeholders in the oil and gas sector.
Turnaround Time in Manufacturing: This refers to the duration required to transform raw materials into finished products, encompassing the entire production cycle, from receiving materials to shipping the final goods.
Turnaround Time in Order Processing: This type measures the time taken to process and fulfill customer orders, starting from when the order is placed until it is delivered to the customer.
Turnaround Time in Service: In the service industry, this represents the time required to respond to and resolve customer inquiries, requests, or issues, from the initial contact until the service is completed satisfactorily.
Repair Turnaround Time: Applicable in industries such as automotive, electronics, or equipment maintenance, this type of turnaround time measures the duration required to diagnose, repair, and return a faulty or damaged item to its owner.
Project Turnaround Time: For complex projects involving multiple phases or milestones, project turnaround time tracks the overall duration from project initiation to completion, including planning, execution, and delivery stages.
Logistics Turnaround Time: In the transportation and logistics sector, this type of turnaround time focuses on the duration required to move goods or materials from one location to another, encompassing activities such as loading, transportation, and unloading.
By understanding and measuring these various types of turnaround times, organizations can gain valuable insights into specific areas of their operations, enabling targeted improvements and optimizations.
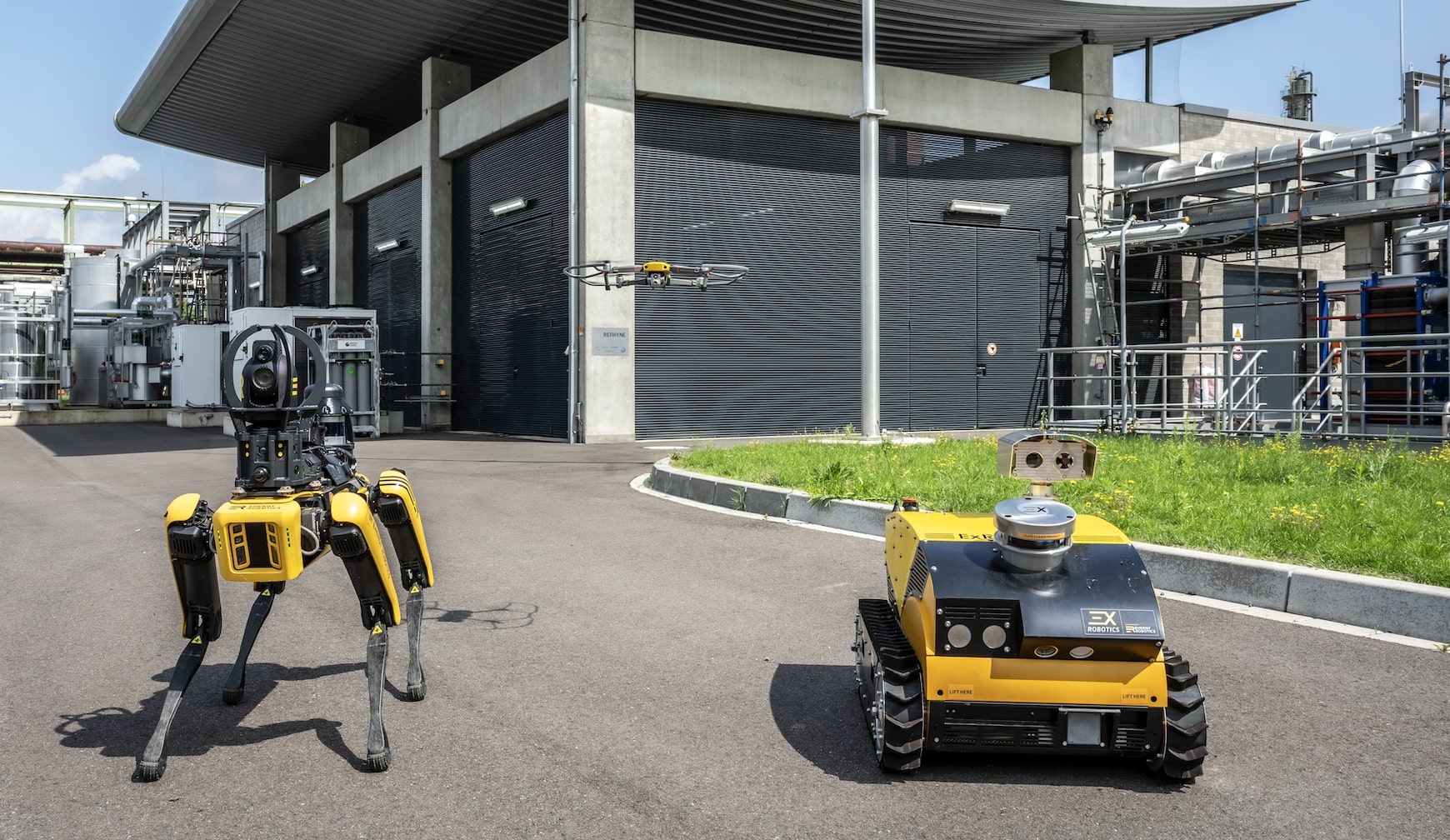
Industry-specific Examples and Use Cases
Turnaround time is a critical metric across numerous industries and applications. Here are some examples and use cases that illustrate its importance:
Oil and Gas: Turnaround time plays a crucial role in maintaining operational efficiency and safety. Refinery turnarounds, and planned shutdowns occurring every three to five years, are essential for preventive maintenance, renovations, and upgrades. These strategic events ensure safe, competitive, and compliant refinery operations. Optimizing turnaround time, refineries can significantly reduce operational costs and enhance overall performance, underscoring the critical nature of these periodic maintenance events in the industry. We at Energy Robotics work closely with Shell to minimize downtime at their largest facility in Germany through AI-driven autonomous inspection with robots and drones.
Power and Utilities: Industry-specific challenges include complex equipment maintenance, stringent safety protocols, and strict regulatory compliance requirements. For instance, a power plant undergoing a scheduled turbine overhaul must meticulously plan every step to minimize downtime while ensuring all safety and regulatory standards are met. The financial implications of extended downtimes can be staggering; a single day of unplanned outage at a large power plant can result in losses exceeding $1 million. Consequently, optimizing turnaround schedules and implementing robust preventive maintenance strategies are paramount for utilities to maintain reliability, reduce costs, and ensure uninterrupted power supply to consumers. Find out how we help Bayernwerk with our automated inspections to reduce downtime at their substations.
Chemical Industry: Downtime and turnaround time are critical factors in the chemical industry, significantly impacting operational efficiency and profitability. Unplanned downtime, such as equipment failures or safety incidents, can result in substantial production losses and potential environmental hazards. For instance, a sudden reactor shutdown at a petrochemical plant could lead to millions of dollars in lost revenue per day. Conversely, planned turnaround time, essential for maintenance and upgrades, requires meticulous scheduling to minimize disruptions. A well-executed turnaround at an ethylene cracker plant, typically lasting 4-6 weeks, can enhance plant reliability and output for years. However, poor planning can extend turnaround duration, causing ripple effects throughout the supply chain. Efficient management of both downtime and turnaround time is crucial for chemical companies to maintain competitiveness, ensure safety, and meet market demands in this high-stakes industry. Read our case study on how we enabled reliable autonomous inspections at Evonik.
Manufacturing: In an automotive manufacturing plant, turnaround time can refer to the duration required to produce a vehicle, from the arrival of raw materials to the final assembly and quality checks. Minimizing turnaround times in this context can lead to increased production output, reduced inventory costs, and improved delivery times to customers.
E-commerce: For online retailers, turnaround time can refer to the duration from when a customer places an order to when the product is delivered to their doorstep. Shorter turnaround times in e-commerce can enhance customer satisfaction, reduce cart abandonment rates, and provide a competitive edge over slower competitors.
Healthcare: In a hospital setting, turnaround time can be applied to various processes, such as patient admission and discharge procedures, laboratory test result delivery, or emergency room wait times. Optimizing turnaround times in healthcare can improve patient experiences, ensure timely diagnoses and treatments, and potentially save lives in critical situations.
Software Development: In the software industry, turnaround time can be associated with the duration required to develop, test, and release new software versions or features. Efficient turnaround times in this context enable faster time-to-market, quicker bug fixes, and the ability to rapidly adapt to changing customer needs or market demands.
Customer Service: For call centers or support teams, turnaround time can measure the duration from when a customer initiates a request or inquiry to when it is satisfactorily resolved. Minimizing turnaround times in customer service can improve customer satisfaction, reduce churn rates, and enhance the overall brand reputation.
These examples demonstrate the widespread applicability of turnaround time across various sectors and highlight the potential benefits of optimizing this critical metric for operational excellence and customer satisfaction.
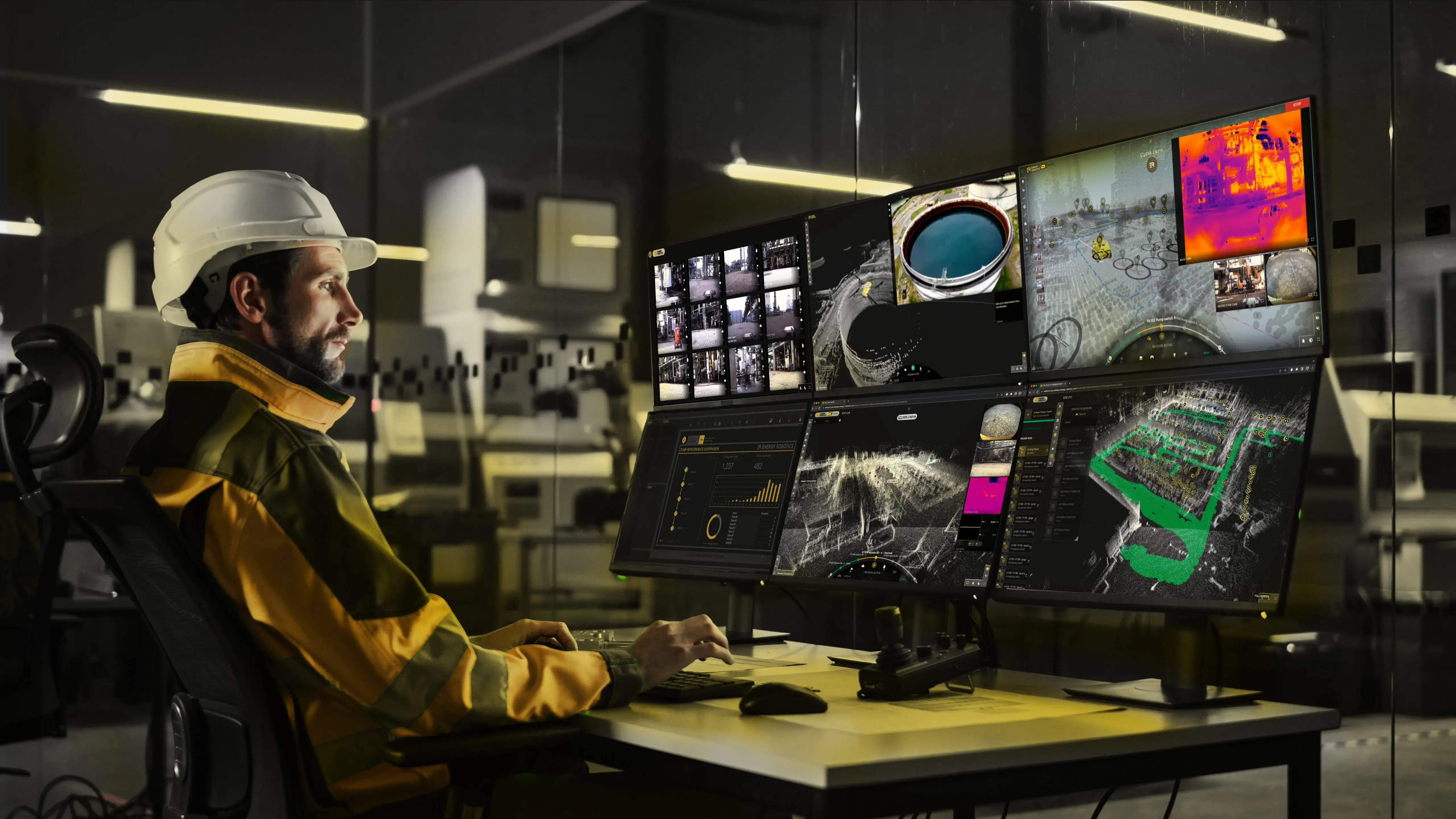
Factors Affecting Turnaround Time
Several factors can influence turnaround times, and understanding these factors is crucial for identifying areas for improvement and implementing effective strategies. Here are some common factors that can impact turnaround times:
Timely Alerts: Predictive maintenance through early alerts is crucial for minimizing turnaround times. By continuously monitoring equipment and processes, robots can detect anomalies or potential failures well in advance. These insights, coupled with AI analysis, generate actionable alerts that allow inspectors to address issues proactively. This proactive approach prevents equipment failures, reduces the scope of repairs, and optimizes maintenance schedules, ultimately leading to shorter turnaround times and increased plant efficiency.
Process Complexity: The more intricate or convoluted a process is, the longer the turnaround time may be. Complex processes often involve multiple steps, dependencies, or stakeholders, which can introduce delays or bottlenecks.
Resource Availability: Inadequate resources, such as personnel, equipment, or materials, can significantly prolong turnaround times. Ensuring sufficient resource allocation and optimizing resource utilization are essential for minimizing turnaround times.
Workflow Inefficiencies: Poorly designed or outdated workflows can lead to unnecessary steps, redundancies, or inefficiencies, resulting in longer turnaround times. Streamlining workflows and eliminating non-value-added activities can improve efficiency and reduce turnaround times.
Communication and Collaboration: Ineffective communication or lack of collaboration among team members, departments, or external stakeholders can cause delays, misunderstandings, or rework, ultimately increasing turnaround times.
Unexpected Disruptions: Unforeseen events, such as equipment breakdowns, supply chain disruptions, or natural disasters, can significantly impact turnaround times by causing unplanned downtime or delays.
Skill and Experience Levels: The expertise and proficiency of the individuals involved in a process can influence turnaround times. Highly skilled and experienced personnel may be able to complete tasks more efficiently, while a lack of training or knowledge can lead to longer turnaround times.
Technology and Automation: The adoption of advanced technologies, automation tools, or digital solutions can streamline processes, reduce manual efforts, and ultimately improve turnaround times. Conversely, outdated or inefficient systems can hinder productivity and prolong turnaround times.
By identifying and addressing these factors, organizations can implement targeted strategies and improvements to optimize turnaround times and enhance overall operational efficiency.
4 Ways to Improve Turnaround Time
Improving turnaround times is an ongoing pursuit for organizations seeking to enhance operational efficiency, customer satisfaction, and overall competitiveness. Here are four effective ways to achieve this goal:
Process Optimization and Automation:
- Conduct thorough process mapping and analysis to identify bottlenecks, redundancies, or inefficiencies.
- Implement process re-engineering initiatives to streamline workflows and eliminate non-value-added activities.
- Leverage automation technologies, such as robotic inspection or workflow management systems, to automate repetitive tasks and reduce manual efforts.
- Continuously monitor and measure process performance to identify opportunities for further optimization.
Resource Management and Capacity Planning:
- Conduct resource capacity planning to ensure adequate staffing, equipment, and material availability.
- Implement workforce optimization strategies, such as cross-training or flexible scheduling, to better align resources with demand fluctuations.
- Invest in modern equipment or infrastructure upgrades to enhance operational capabilities and reduce downtime.
- Optimize inventory management practices to maintain sufficient stock levels while minimizing excess inventory.
Technology Adoption and Integration:
- Evaluate and implement advanced technologies that can streamline processes, improve visibility, and enable real-time decision-making.
- Leverage data analytics and business intelligence tools to gain insights into performance metrics and identify areas for improvement.
- Integrate systems and platforms across different departments or functions to enable seamless data sharing and collaboration.
- Adopt cloud-based solutions or software-as-a-service (SaaS) offerings to enhance scalability, accessibility, and cost-effectiveness.
Continuous Improvement and Employee Engagement:
- Foster a culture of continuous improvement by encouraging employee feedback and suggestions for process enhancements.
- Implement regular training and development programs to upskill employees and enhance their capabilities.
- Promote cross-functional collaboration and knowledge sharing to break down silos and improve coordination.
- Implement performance management systems that incentivize and recognize efforts to improve turnaround times.
By implementing these strategies, organizations can achieve substantial improvements in turnaround times, leading to increased operational efficiency, enhanced customer satisfaction, and a competitive edge in their respective markets.
Future Trends and Emerging Technologies
As technology continues to evolve at a rapid pace, new trends and emerging technologies are poised to revolutionize the way organizations approach and optimize turnaround times. Here are some notable developments to watch out for:
Artificial Intelligence (AI) and Machine Learning (ML):
- AI and ML algorithms can be leveraged to analyze vast amounts of data, identify patterns, and provide predictive insights for optimizing processes and minimizing turnaround times.
- Intelligent automation, powered by AI and ML, can automate complex decision-making processes, reducing human intervention and accelerating turnaround times.
.gif)
Internet of Things (IoT) and Sensor Technology:
- IoT-enabled sensors and devices can provide real-time monitoring and data collection capabilities, enabling organizations to track and optimize turnaround times with greater precision.
- Predictive maintenance enabled by IoT can help minimize unplanned downtime, reducing disruptions and improving overall turnaround times.
- However, replacing thousands of devices with IoT sensors is cost-prohibitive for brownfield industries. Furthermore, these IoT sensors themselves need to be inspected on a regular basis.
Blockchain and Distributed Ledger Technology:
- Blockchain can enhance supply chain transparency, enabling faster and more secure data sharing among stakeholders, and potentially reducing turnaround times in logistics and procurement processes.
- Smart contracts enabled by blockchain can automate and streamline complex business processes, minimizing delays and improving turnaround times.
5G and Edge Computing:
- The advent of 5G technology and edge computing can enable real-time data processing and decision-making, facilitating faster response times and reducing turnaround times in time-critical applications.
- Enhanced connectivity and low latency enabled by 5G can support remote monitoring, control, and collaboration, improving turnaround times in industries such as manufacturing and healthcare.
Augmented Reality (AR) and Virtual Reality (VR):
- AR and VR technologies can enhance training and knowledge transfer, enabling employees to acquire skills more efficiently and potentially reducing turnaround times associated with learning curves.
- Remote collaboration and assistance enabled by AR/VR can facilitate faster problem-solving and decision-making, improving turnaround times in maintenance, repair, and troubleshooting scenarios.
Autonomous Robots and Drones:
- Autonomous inspections through robots and drones equipped with advanced sensors bring together AI and ML capabilities, real-time monitoring with low-latency streams, edge computing and ever-green digital twin technologies, making it the most comprehensive solution.
- Data collected and analyzed through multiple daily inspection rounds performed by AI-driven robots and drones has the greatest impact in minimizing downtime by delivering timely insights and alerts.
- Autonomous robots and drones are the best and most cost-effective solution for automated inspections in the industrial sector due to their ability to access hard-to-reach areas, operate in hazardous environments, and conduct inspections with precision and consistency. They reduce the need for human intervention, minimizing safety risks and labor costs while providing real-time data and insights. Their efficiency in performing routine inspections without the need for downtime enhances productivity and ensures that potential issues are identified and addressed quickly, leading to significant savings in maintenance and operational costs.
How Autonomous Robots Help Significantly Reduce Turnaround Times
In industries such as oil and gas, power generation, and manufacturing, turnaround times for maintenance and inspection activities can be significantly reduced through the integration of autonomous robots. These intelligent and self-navigating robots offer several advantages:
24/7 Operation: Autonomous robots can operate continuously, without the need for human intervention or breaks, enabling round-the-clock monitoring and inspection capabilities.
Hazardous Environment Access: Robots can safely access and operate in hazardous or extreme environments, such as confined spaces, high-temperature areas, potentially explosive zones (ATEX/IECEx Zone 1 areas) or radioactive zones, reducing the need for human exposure and associated safety risks.
Consistent and Reliable Data Collection: Equipped with advanced sensors autonomous robots can consistently and accurately collect data, minimizing the risk of human error or variability in data quality.
Predictive Maintenance Integration: By integrating with predictive maintenance systems and leveraging AI-driven real-time data analysis, autonomous robots can identify potential issues early, enabling predictive maintenance and minimizing unplanned downtime.
Collaboration with Human Workers: Autonomous robots can work alongside human operators, complementing their capabilities and enhancing overall efficiency and productivity.
Adaptability and Scalability: Autonomous robot systems can be easily adapted and scaled to meet changing operational requirements, providing flexibility and responsiveness to dynamic business needs.
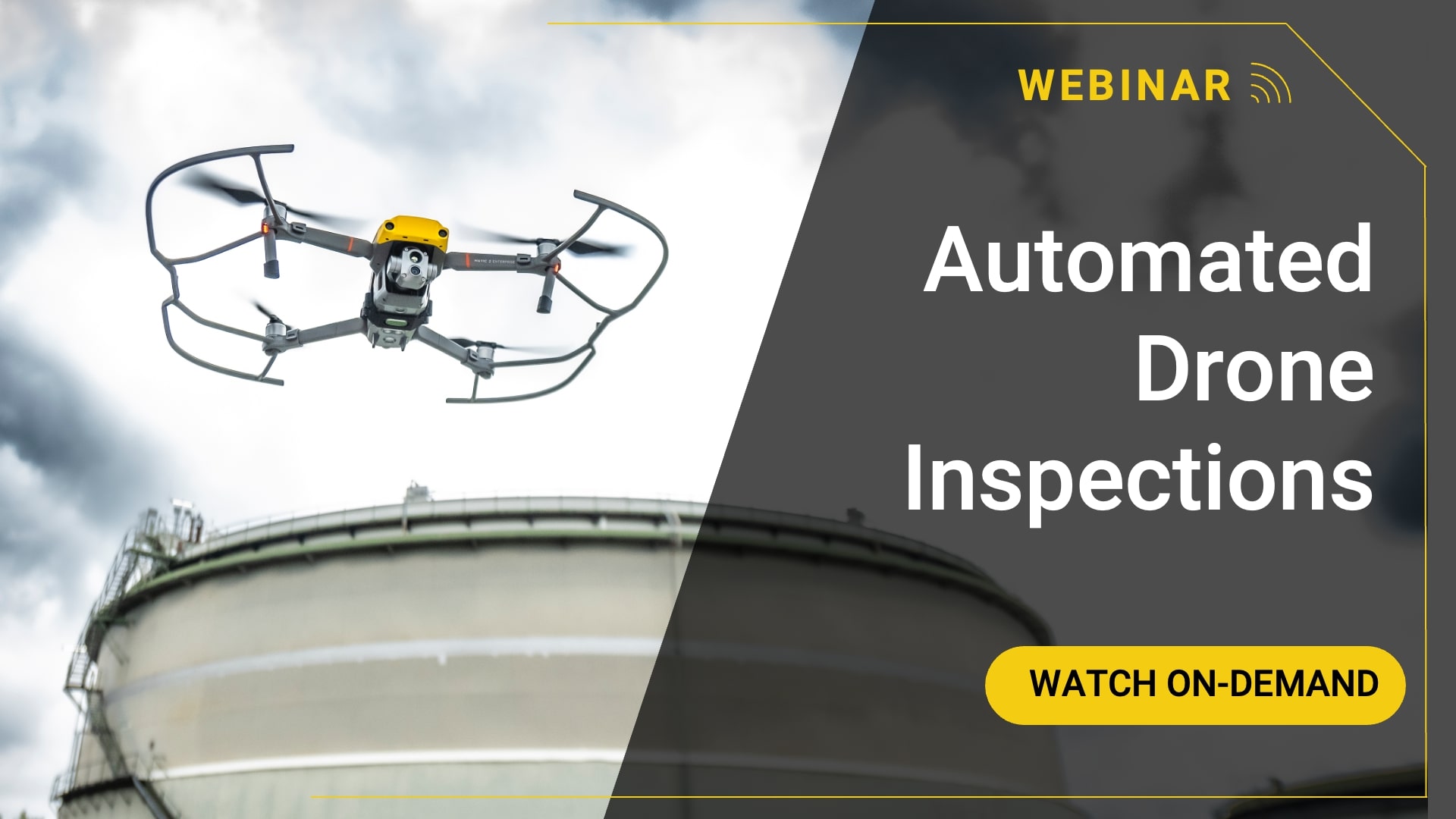
How Automated Drones Help Significantly Reduce Turnaround Times
In addition to robots, the integration of drones for automated inspections is another emerging technology that can contribute to reduced turnaround times in various industries.
These unmanned aerial vehicles (UAVs) offer several advantages that can streamline operations and minimize downtime:
Rapid Deployment: Drones can be quickly deployed to inspect hard-to-reach or hazardous areas, eliminating the need for time-consuming and costly manual inspections or scaffolding setups.
Comprehensive Data Collection: Equipped with advanced sensors and cameras, drones can capture high-resolution visual data, thermal imaging, and other critical information, providing a comprehensive understanding of asset conditions without the need for physical access.
Continuous Monitoring: Drones can be programmed to conduct regular, automated inspections, enabling continuous monitoring of assets and early detection of potential issues, reducing the risk of unplanned downtime.
Improved Safety: By eliminating the need for personnel to access hazardous or confined spaces, drones enhance worker safety and reduce the risks associated with manual inspections.
Cost Savings: The use of drones can significantly reduce inspection costs by minimizing the need for specialized equipment, personnel, and downtime, leading to substantial cost savings over traditional inspection methods.
Data Integration: Drone-captured data can be seamlessly integrated with other systems, such as asset management platforms or digital twins, enabling predictive maintenance strategies and optimized decision-making.
By leveraging automated drones for inspection and monitoring activities, organizations can significantly reduce turnaround times associated with maintenance and inspection tasks, improving operational efficiency, minimizing downtime, and maximizing asset utilization.
Our AI-driven software for automated inspections integrates multiple cutting-edge technologies and enables asset owners to onboard a mixed fleet of different robots and drones. Though our primary objective is to automate repetitive operations using robots and drones, our comprehensive solution also delivers real-time data processing and AI-backed actionable insights, making our service the most efficient method to minimize downtime and enhance turnaround times.
By staying abreast of these emerging technologies and trends, organizations can position themselves to leverage cutting-edge solutions and gain a competitive advantage in optimizing turnaround times and enhancing operational efficiency.
Conclusion
In today's fast-paced and competitive business landscape, optimizing turnaround times is a critical endeavor for organizations striving for operational excellence, customer satisfaction, and long-term success. By understanding the nuances of turnaround time, its various types, and the factors that influence it, businesses can develop targeted strategies to streamline processes, enhance resource utilization, and leverage emerging technologies.
As we have explored, turnaround time is a multifaceted concept that permeates various industries and operations, from manufacturing and healthcare to logistics and customer service. By measuring and monitoring turnaround times, organizations can identify bottlenecks, inefficiencies, and areas for improvement, enabling data-driven decision-making and continuous process optimization.
The adoption of comprehensive digital technologies, such as autonomous robots and drones for industrial inspections, presents exciting opportunities to revolutionize maintenance operations, enhance data quality, and unlock new levels of operational efficiency. By embracing these innovations, organizations can stay ahead of the curve and gain a competitive edge in their respective markets.
However, it is essential to recognize that optimizing turnaround times is an ongoing journey that requires a commitment to continuous improvement, employee engagement, and a culture of innovation. By fostering a mindset of adaptability and embracing emerging trends, organizations can future-proof their operations and position themselves for long-term success.
In conclusion, mastering turnaround time is a critical endeavor that transcends industries and disciplines. By embracing the strategies and technologies outlined in this comprehensive guide, organizations can unlock new levels of efficiency, productivity, and customer satisfaction, paving the way for sustained growth and success in an ever-evolving business landscape.