The management of change can be both exciting and daunting for any organisation. Whilst change management can be transformative, it can also be disastrous if implemented poorly. Although the focus may be on change, the real driver should be transformation. As the entrepreneur and business process guru, Nick Candito, states, “Companies that change may survive, but companies that transform thrive.”
Robotic technology can be a very effective driver for change that is transformational, particularly if it is put to sophisticated use. An example of this could be using robots to conduct inspections in potentially hazardous or difficult locations. Robots can be used as conduits, as well as allies, for change to occur.
The possibilities of change brought about by robotic technology will be the central thesis of this article. However, the intent here will be even more precise: not only can robotic technology facilitate change management in an organisation, it is employees who should be the principal drivers (and benefactors) of that change management.
Resistance to Change Management
One cannot analyse any aspect of change management without acknowledging that there will invariably be those who resist it within an organisation. Resistance to change is inherently human, in that familiarity affords people comfort zones, something which can be particularly appealing in the workplace. Resistance to robots, for example, is a variation on a familiar theme, with push-back against technological change dating back to the Luddites who resisted certain forms of mechanization during the Industrial Revolution, and even further back to Ancient Roman times.
Woodside Energy: Real Change Management with Robotics
An excellent example of how robotics can help champion change management processes was highlighted during the SPRINT Robotics Awards in September 2021. The success story discussed was Woodside Energy, Australia's leading natural gas producer based in Perth, Western Australia. Woodside is a giant in its field - established in 1954, it produces 6% of the global LNG supply (2020) and has over 3,500 employees.
Mark Micire, the Head of Robotics and Production Technology at Woodside Energy, spoke about how the company had made significant investments in Internet of Things (IoT) and digital twin technologies to date. He believed that robotic technology would step it up, affording Woodside other, even more exciting and new capabilities as part of its digital-inspired change management strategy.
Woodside Energy is itself a company proud of its innovation in governance and sustainability. The company’s CEO, Meg O’Neill, is the embodiment of that proactive, progressive mindset. O’Neill is a huge believer in the importance of an open management style that encourages employee participation and that fosters empowerment throughout the company.
Micire discussed how Woodside has made use of ExRobotics hardware embedded with Energy Robotics software. This was achieved at the Karratha Gas Plant (KGP), which is located in northern Western Australia, some 1,500 kilometres north of Perth. It is considered one of the most advanced gas production facilities in the world, producing LPG, LNG, domestic gas and condensate. KGP operations employees teamed up with autonomous robots in order to undertake inspections. The ExR-1 robots were tasked to travel through zoned environments autonomously and with human supervision.
The robotic technology was found to be preferable to static sensors, as it allows cameras and gas sensors to roam throughout the plant, as and where needed.
.png)
The robots were found to be easy to set up and operated by operators appointed for the tasks. But the robot project had even more unexpected benefits, according to Micire. “Much to our surprise, the operations folks not only figured out the technical aspects of the robot, but also worked out permitting management to change and are coming up with new applications for this technology every day.”
There was a very important lesson to be learned from the Woodside Energy robotic pilot project at its KGP facility: allow customers to find out and learn solutions on their own. Critically, those ‘customers’ should include the operators/employees that will be working hands-on with the robots. As Mark Micire of Woodside noted, employees may even find novel and innovative ways of gaining value from the robotic technology. And‘ novel’ and ‘innovation’ should be the cornerstones of any digital change management process.
Robotics and A Change Management Ethos
As seen with the Woodside Energy case study, the transformative capabilities of robotic technology require sound leadership from executive management, as well as trust and belief in what employees will be able to achieve with said technology. An important part of the robotic change management ethos is that the technology should be viewed as a valuable and trustworthy ally for employees, not a replacement quasi-‘replicant’ that is going to make their work redundant. Boring, repetitive tasks can be supplanted by a robot so that employees can get on with more challenging, intellectually stimulating work.
This messaging is easily conveyed for those tasks where danger and difficulty are also key reasons why employees should be pleased that robots do the work instead. A good example of this approach is that of inspections in potentially hazardous or difficult locations, such as those found in oil and gas or chemical facilities. Inspections in these locations can often be hazardous to safety or physically challenging for employees. By having robots do the physical inspections instead, the operator is free to do other work. Furthermore, robots will often require some form of human input anyway, so those too are skills that can add to the competency and technical know-how of employees.
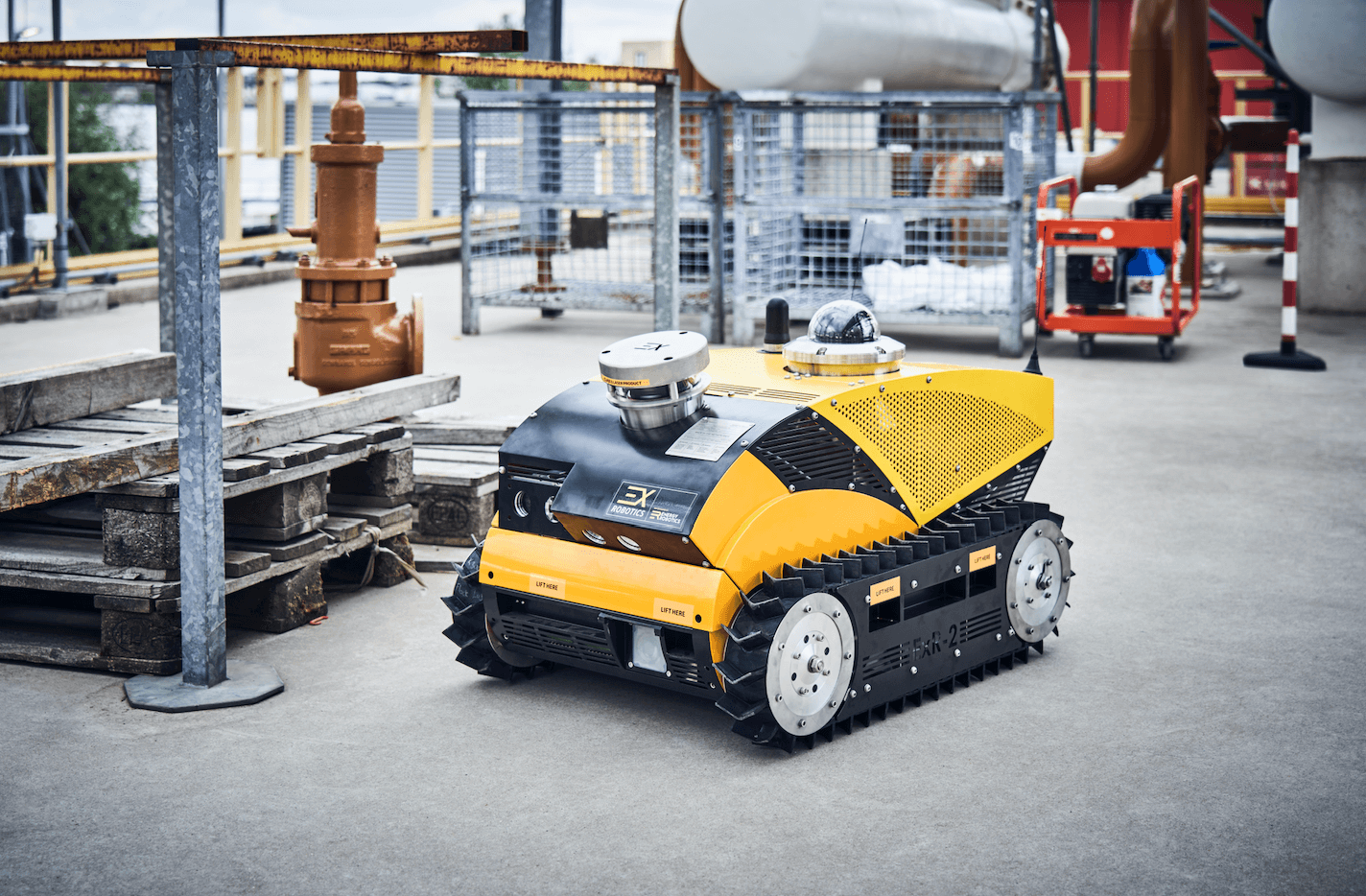
This important point regarding the viability of using inspection robots is driven home by Marc Dassler, CEO and co-founder of Energy Robotics, who comments that, “In general, robots can perform certain routine inspections in a more accurate way, than humans. Whether it's due to a person's physical limitations or even a hostile environment for humans...we increase safety because we remove humans from these dangerous environments. Ultimately, we increase the quality of the inspection because humans are simply not made for this type of work.”
The bottom line is that a robot will invariably be far more error-free than a human operator, whatever the task. That fact need not intimidate nor antagonize employees who need to work side-by-side with robots.
Fundamentals of Robotics-Led Change Management
There are certain fundamentals that should always be considered when investing in robotics for the purpose of change management goals. Below are three important fundamentals to consider for such a process:
1. Be Open: According to Susan Steele, global chief human resources (HR) officer for the media intelligence company, Cision, it is important that any form of automation must be transparently implemented in full co-operation with those employees who will need to work with whatever robotic technology may be used. Steele found that an open, transparent approach transformed anxiety among employees regarding the introduction of robotics to excitement about what the employees could achieve with the technology.
2. Be Prepared: Employees/operators need to be fully prepared for a robotics-centred change management process. Important considerations for a smooth, successful transition include appropriate training, being open to questions and doubts by employees (i.e. managing expectations) and timely, inclusive communication at all times.
3. Be Human: Employees/operators are the human face of an organisation and they should command the respect they deserve during any change management initiative that includes robotics. As already discussed, a significant (and, very probably, the leading reason) for resistance by employees to robots is the perception that they will ‘steal’ jobs and make employees redundant. These are very real fears that need to intelligently assuaged by management, a point driven home by Forbes regarding transformative technologies such as robots. This means making clear the benefits of said technology and the value that change will bring to the organisation and employees alike.
To conclude, Financial Management observed in 2020 that, “The human side of change remains the most challenging element in managing any digital transformation.” This is as true in 2021 - and will be so for some time to come. Nor should it be surprising, given that the focus of employees is on their work in the here and now, rather than a broader, strategic view of an entire organisation. The latter is, after all, the purview of management. However, resistance to change, such as robotic technology for inspection purposes, can hinder and even block much-needed change.
There is no denying the value that robots can bring to an organisation in terms of efficiency, productivity, asset integrity and even safety. As such, a ‘robotic revolution’ within an organisation that is well-considered and well-communicated will reap rich rewards. The result will not only be needed change, but, better still, true transformation. Demystify the robot, and the rest will follow.