Expanding electricity demand, along with a rising percentage of inputs into the grid via renewable sources, means a rising number of electrical infrastructure, including substations. Substations are an integral and critically important part of any electrical generation, transmission and distribution system. Germany, for example, has 8,000 substations, whilst the U.S. has 55,000. The fact that they are often in remote locations makes the inspection of substations all the more logistically and financially burdensome and problematic for energy utilities. That is why inspections by mobile robots of certain key parameters in substations is a highly beneficial alternative to physical inspections by humans. This input by robots is particularly relevant within the context of four major potential risks or impacts posed by most substations, namely fire, explosion, emissions and theft.
Minimize the Risk of Fire or Explosion
An important robot inspection at a substation is to check on power couplings, an important consideration given that it is usually a facility with electrical (or switchable) equipment with multiple configurations. That inspection is critical because a leading cause of electrical fires and explosions at substations is electrical arcing. An ABB study of arc phenomenon found that most switchgear arcing accidents at substations occurred due to human factors during either installation, maintenance or inspection. As with so much hazardous work, remove the human factor and the risk tends to decrease, sometimes appreciably.
Another inspection that a robot can undertake at a substation is to check on oil levels in transformers. The voltage conversion process that occurs in transformers can generate immense amounts of heat due to electrical resistance, which is why insulating fluids are used to absorb this heat.
Robots can also assist in the inspection of leaks at transformers, which is important since transformer fires can be in the form of pool fires, which occur when transformer oil leaks from gaskets, breaches in the steel tank or other defects onto the ground. Leak detection during inspection is also important for spray fires, which occur when flammable vapours are released from an overheating transformer tank into the surrounding atmosphere.
The risk of fire at a substation is not negligible. A transformer has an average 4 percent risk of fire over a typical 40-year service life, according to The the International Council on Large Electric Systems (CIGRE) Technical Brochure 537, titled Guide for Transformer Fire Safety Practices.
.jpeg)
Minimize Emissions of SF6
Sulphur hexafluoride, or SF6, is a cheap and non-flammable synthetic gas that is widely used in the electrical industry to prevent short circuits due to over-heating in vessels and electrical equipment such as transformers. It is immensely effective as an insulating material in medium and high-voltage electrical installations. Unfortunately, it is also the most powerful and thus toxic greenhouse gas known to humanity, with 23,000 times more global warming potential than carbon dioxide. That is why just one kilogram of SF6 is the equivalent of 24 people flying from London to New York return in terms of global warming. In 2017, it was estimated that SF6 leakages in the European Union amounted to the equivalent of an extra 1.3 million cars on the road. It is also a highly persistent greenhouse gas with a lifespan of at least 1,000 years. Autonomous robots can be used for leak detection during an inspection, thereby solving the potential risk of undue SF6 leakages from substation equipment.
Minimize the Risk of Theft
Copper theft from substations and other electricity infrastructure has been on the rise in recent years due to the rising price of copper on the world market. This theft is a problem worldwide. In 2021 alone, copper theft from a substation left 2,137 households without power in Kingston, South Australia, at the height of winter, whilst copper theft resulted in a fire at a rural substation in eastern Texas that resulted in power outages for about 2000 homes.
Mobile robots installed with cameras can undertake surveillance of substation perimeters and result in speedier alerts at off-site security control stations of breaches by unauthorized persons, as well as other unwanted ‘visitors’ such as children or animals. These robots can also do checks on the integrity of fencing and other barriers limiting access into a facility, as well as whether doors and gates have been locked, and so forth.
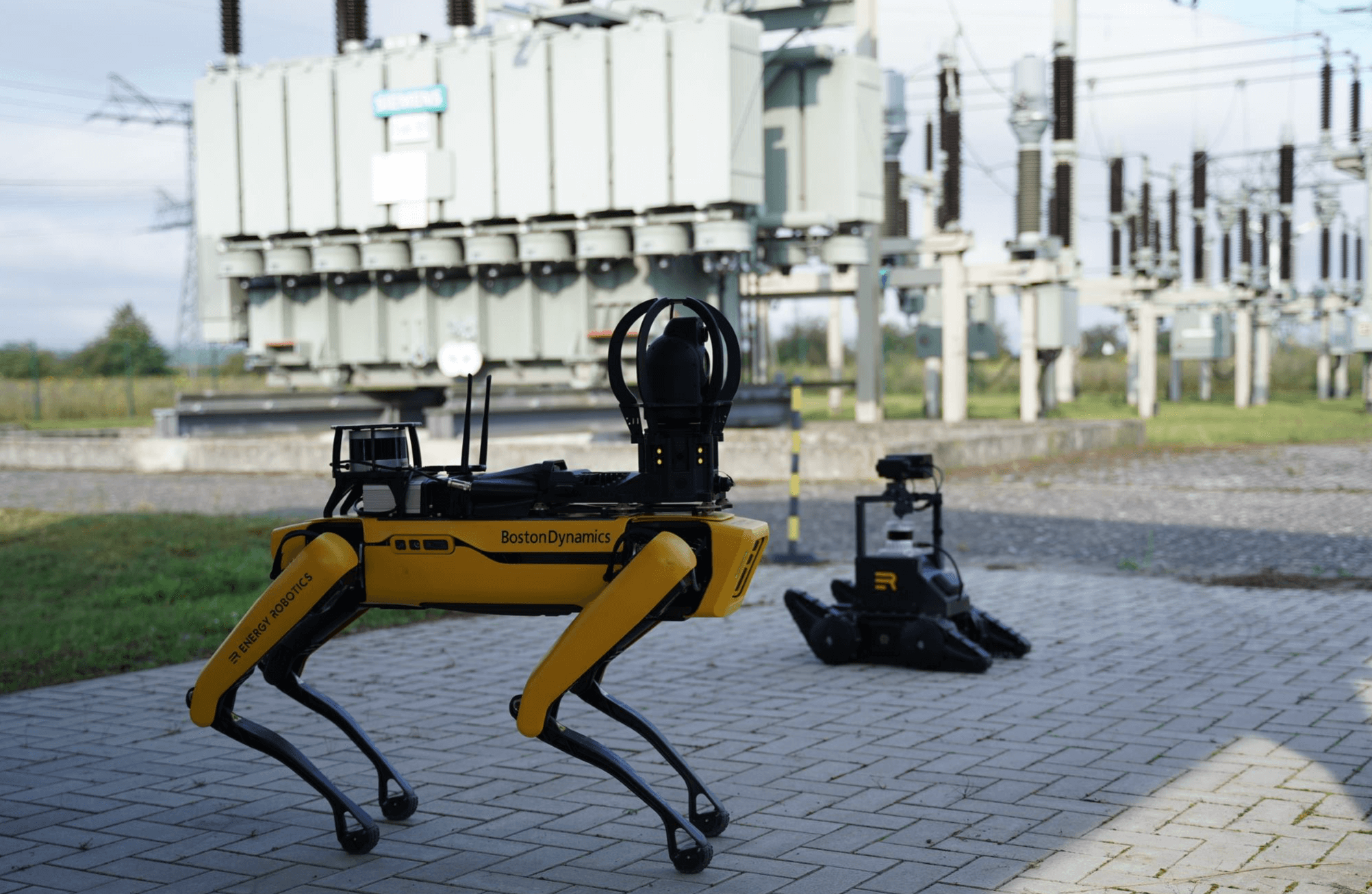
Other Relevant Factors
Besides the risk factors of fire, explosion, emissions and theft discussed above, there are other factors that are also relevant regarding the viability of using mobile robots for inspections at substations.
The Renewable Energy Factor
As mentioned in the introduction, many countries worldwide are experiencing an ongoing boom in renewable power generation. For example, energy from renewable sources such as wind, solar PV and biomass already accounts for 45 percent of Germany’s national grid. This means that hundreds of thousands of small installations for renewables transmission will continue to be added to the grid, with, for example, over 1.7 million solar PV installations and over 29,000 onshore wind turbines already existing in Germany by 2020. The result is an invariable increase in the numbers of substations or additional burden on existing substations, which, in turn, means heightened substation-related risks countrywide. That reality is replicated worldwide.
The Issue of Demographics
Germany, like so many Western countries, has an ageing population and, therefore, a demographics issue. In 2020, Germany's population declined by 0.05 percent to 83.1 million people in the first half of this year, with 112,000 more deaths in the country than births. More alarmingly, Germany's population is expected to shrink by around five million people to approximately 78.2 million by 2030, according to the country’s statistical office, Destatis.
This demographic dilemma is reflected in the declining number of electrical and electronic engineers being trained in Germany. According to a December 2018 report by the Verband der Elektrotechnik Elektronik Informationstechnik (VDE) technology association, there will be over 100,000 unfilled engineering jobs in Germany within 10 years. Some 10,900 new electrical and electronic engineers were required to replace those engineers retiring in 2018 alone. Energy companies battling with those types of skills shortages will not be wanting to dispatch expensive engineers to do inspections at substations on trips that can take hours, only to get to the location and discover that human error, such as forgotten inspection tools ,will prolong the process even further. Robots can do much of the same work with far less logistical and cost-related variables.
A Successful Pilot Project
A pilot project was undertaken between German electricity company E.DIS (a subsidiary of E.ON) and Energy Robotics at a substation in the town of Altentreptow in eastern Germany.The purpose of the project was to provide important insights into the use of modern robot technology for inspections at substations. The collaboration commenced at the beginning of 2021, with Energy Robotics chosen due to it being able to offer the first commercially available software platform that combines a hardware-independent robot operating system, cloud-based fleet management and AI-driven data analysis for applications such as mobile inspections at substations.
E.DIS was especially keen to assess the inspection of substation technology possible with the robot-enhanced software, such as the reading of analogue measuring instruments. The company was also interested in assessing how fundamental security-related issues could be checked and monitored with the robot, such as whether existing substation fences have been damaged or doors not properly locked. Furthermore, LiDAR installed on the robots can be used to create comprehensive 3D maps of the substation site.
With the potential safety, environmental and financial risks posed by substations, and an ever-growing demand for electricity in most markets, the future of inspections at these facilities will be increasingly robotic.