High risk, high cost - the two guaranteed factors that loom greatest over most inspections in the oil and gas industry. Autonomous ground robots can do much to lower both factors.
Oil and gas is an innately hazardous industry. This is true at any stage of the industry, whether upstream, midstream or downstream. Beyond operational hazards, maintenance and inspection procedures can be high risk too. It is an industry in which safety standards are pivotal to the viability of product and assets alike, not to mention the very survival of workers. As such, inspections abound, be they for the purpose of legal compliance, risk management or for ensuring asset protection and durability.
Inspections can prove immensely costly and are becoming more costly due to factors such as increasing demands for higher EHS standards, rising costs for deployment in high-risk facilities and the rising number of ageing facilities.
Institutional pressures on oil and gas will further drive up the need for inspections, such as ATEX, the two European Union (EU) directives that prescribe stringent minimum safety requirements for workplaces and equipment used in explosive atmospheres.
High risk, high cost - the two guaranteed factors that loom greatest over most inspections. Autonomous robots in the oil and gas industry can do much to lower both factors, as this article will outline.
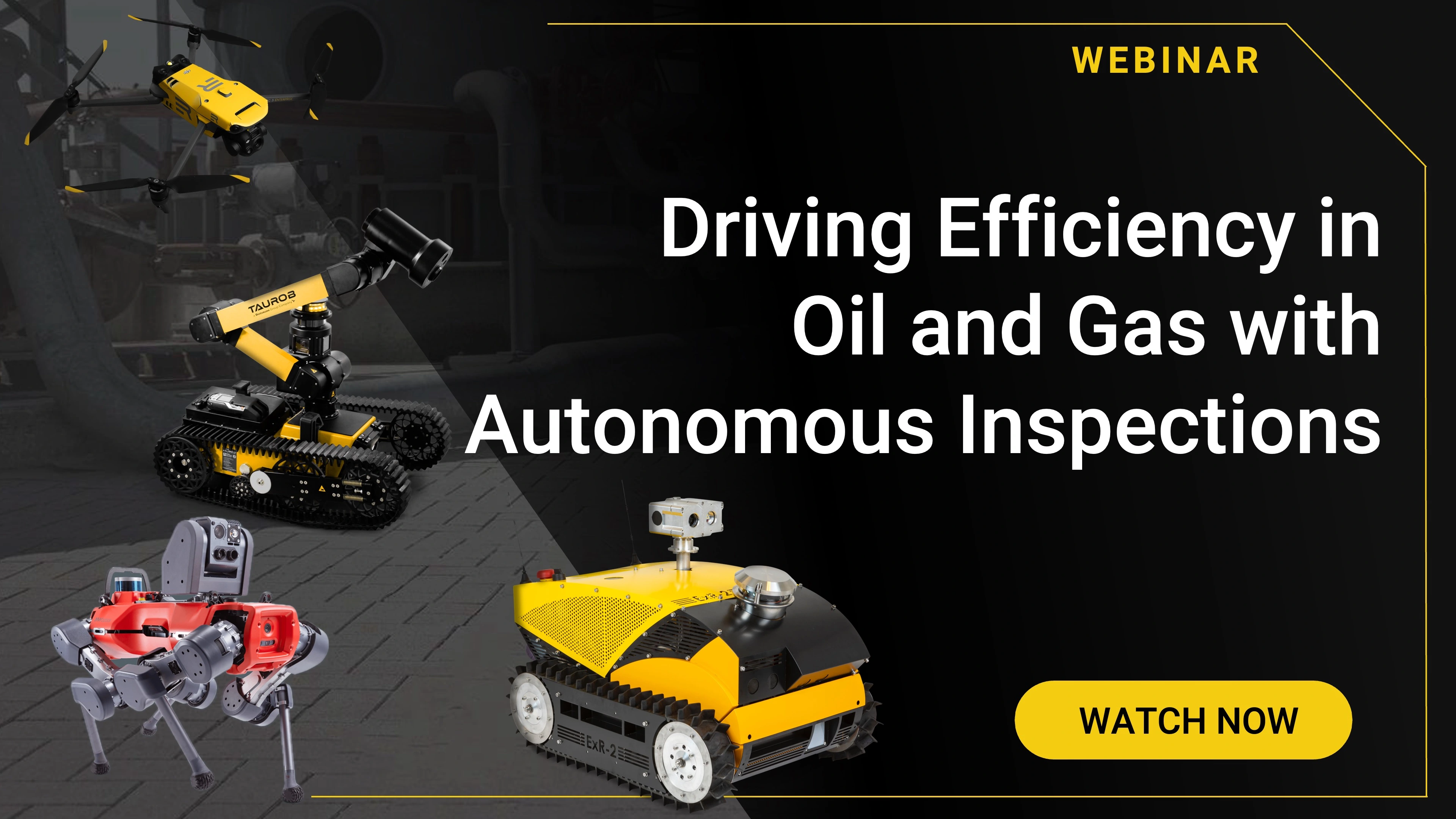
Hazards of Human Inspections in Oil & Gas
Risks abound with most oil and gas inspections, whether for detection of leaks or fugitive gas emissions, identifying fissures and other faults on compromised assets, integrity testing of pipelines, valves and pumps, or the host of other inspections required of the industry. However, it is the introduction of the human factor into these already hazardous inspections that exponentially increases the risk profile of a given inspection task. After all, it is well-established that human error is the most significant risk in any industrial setting and has been the leading cause of most major industrial accidents, including in the oil and gas industry.
Human inspections are exacerbated by the many hazardous locations in which inspections take place in the industry. Inspections can often occur in very remote locations or in locations to which access is very difficult or constricted. Confined spaces, by their very definition hazardous workspaces, can include petroleum and other storage tanks, reserve pits and other excavated areas, storage containers and other confined locations. These inspection areas or vessels often have hazardous levels of noxious/toxic gases or flammable vapours, including high levels of methane, which are a common threat to worker safety, particularly in the gas industry, where methane can comprise as much as 85% of natural gases. Sour gas is another notable hazard, given its significant amounts of hydrogen sulphide (H2S), which is both extremely poisonous and explosive. Furthermore, some petroleum-derived by-products can hasten the deterioration of metals through corrosion, including H2S, thereby creating additional risks to workers undertaking inspections.
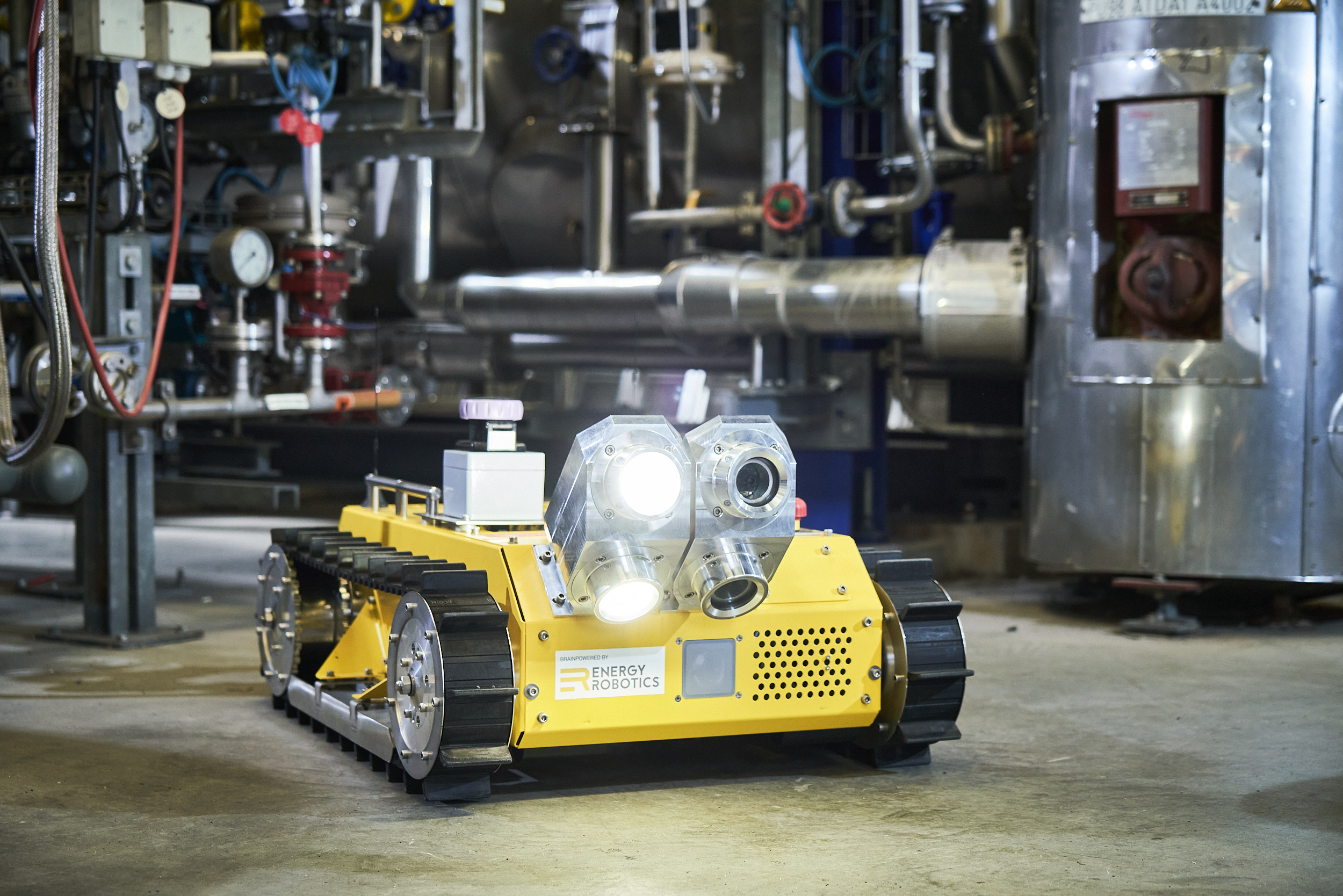
Benefits of Robotic Inspections in Oil and Gas
Ground robots are mobile or fixed robots that operate autonomously and can support operational activities, including inspections. Tasks they can perform include first-level visual and thermal inspections, gauge readings and environmental and mechanical vibration analysis. A combination of artificial intelligence (AI) and data analytics mean that these robots can act as hyper-intelligent, functionally versatile lead or adjunct inspectors in multiple non-destructive inspection processes.
A 2020 World Economic Forum (WEF) report found that robotics would be expected to be one of the highest-adopted technologies among all digital technology investments in the next three to five years. And the industry predicted to have the highest growth in robotics during this period? That would be the oil and gas industry.
As with high risk, the high costs of inspections, in terms of both required time and personnel, is a major negative factor for any oil and gas company. A study of advanced non-destructive testing (NDT) technology, including extensive use of robotics, was undertaken by the Abu Dhabi National Oil Company at its gas-processing field sites, as reported by the Journal of Petroleum Technology (JPT). The Emirati company found that the use of the technology for asset integrity-related inspections (specifically offline pressure vessels) was highly beneficial in terms of time and operational cost savings. Furthermore, there was no compromise in safety, the study stressed. On the contrary, the use of robotics will always be safer than sending people in for the same work, particularly those locations that are inaccessible for humans for safety reasons. Far better to send ground robots into ATEX areas, rather than send in humans to do work in such potentially explosive areas.
Other benefits noted in the Abu Dhabi study included that (1) using the robotic technology avoided or minimized the need for entry by workers into vessels, which automatically improved the safety risk profiles of a site; (2) it minimized operational disruptions due to shorter, more efficient inspections with high quality data; (3) potential environmental impacts were also minimized or avoided; and (4) costs associated with the opening and cleaning of vessels were dramatically decreased.
A further benefit worth noting regarding the use of autonomous ground robots for inspections is within the context of the risk based inspection (RBI) methodology, which is prevalent in the oil and gas industry. RBI focuses on inspections on ‘priority assets,’ as based on a risk-based assessment of the probability of failure (PoF) and the consequence of failure (CoF) of a given asset. These failures are typically health and safety impacts, environmental impacts and business impacts. Lowering all these impacts by using ground robots means that RBI can be used even more effectively in the assessment of all assets on a site - and perhaps for more assets to be considered ‘priority assets’ without undue financial or time costs.
In an industry rightly obsessed with risk and cost, the use of autonomous ground robots for inspections is a sensible, risk-savvy and money-saving choice.
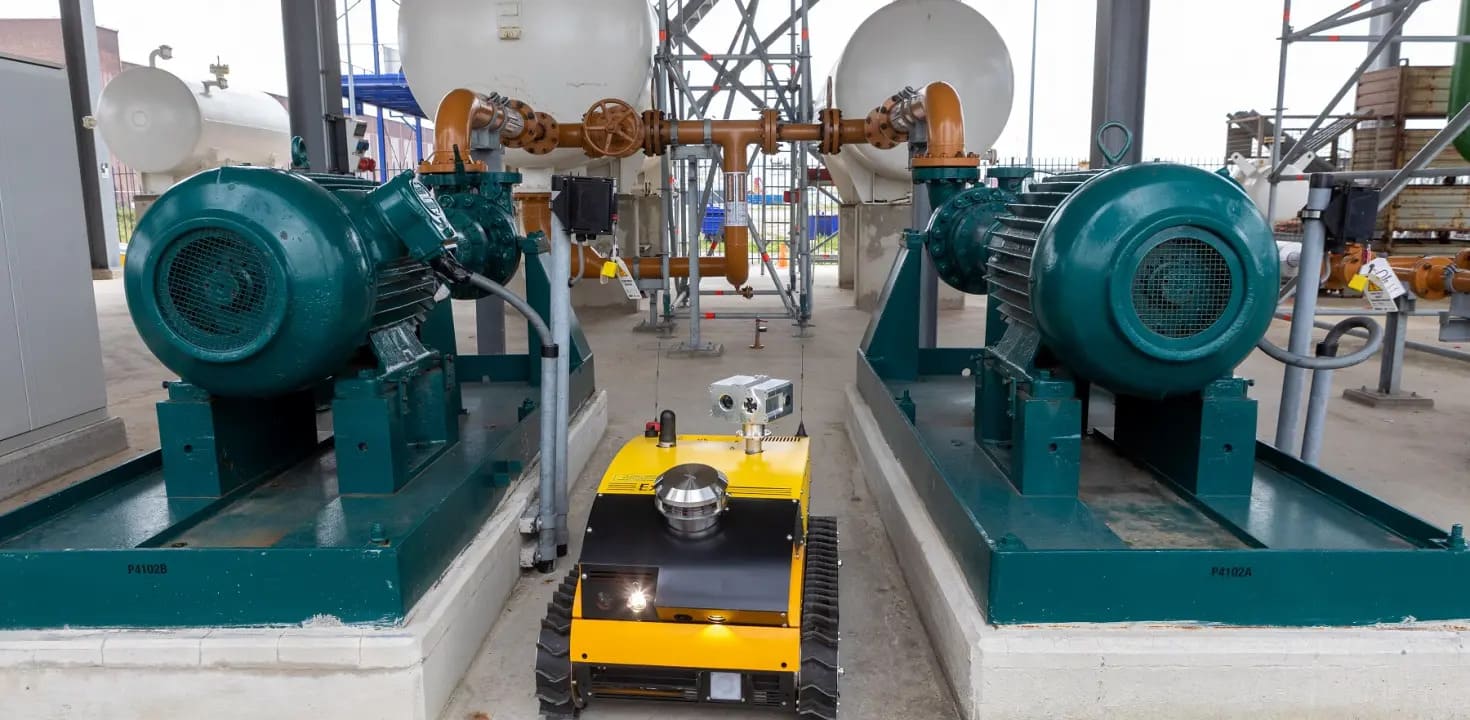
Energy Robotics brain-powers ATEX certified robots from ExRobotics, the ExR-1 and ExR-2 , to perform inspections and monitor oil and gas plants autonomously.
The mission of Energy Robotics is to improve the productivity, safety and data of capital-intensive industrial sites, such as those in the oil and gas industry, through leading mobile AI robotics solutions. We achieve this with cutting-edge functionalities such as:
- Cloud-based fleet management
- AI-driven analytics that delivers actionable information
- Ability to perform inspections in hazardous ATEX zones
- State-of-the-art autonomous navigation
- Remote deployment with robot communication via WiFi/3G/4G/5G networks