Industrial inspection is a fundamental aspect of the industrial manufacturing process. It involves a meticulous examination of equipment, systems, and processes in an industry to ensure they meet the specified standards. This process is critical because it helps to detect defects or irregularities that could potentially lead to accidents or operational failures.
Industrial inspection is not only about maintaining machinery and equipment; it also involves assessing the safety of the working environment. This includes examining the physical state of the workplace, evaluating the safety practices in place, and checking the health status of employees. In essence, industrial inspection encompasses every facet of industrial operation to guarantee optimal functionality and safety.
The process of industrial inspection is usually performed by trained and certified inspectors who utilize various inspection methods and technologies. These inspectors are often employees of the company, but they can also be external professionals hired to conduct the inspection rounds. Their expertise and reliability are crucial factors in ensuring the effectiveness of the inspection process.
However, as we explore in this article manual inspection is ridden with a plethora of challenges and there is a cost-effective, reliable, and safer way to perform industrial inspections. With the advent of Industry 4.0 and the technological advancements it has entailed, autonomous robots and drones are disrupting this field significantly.
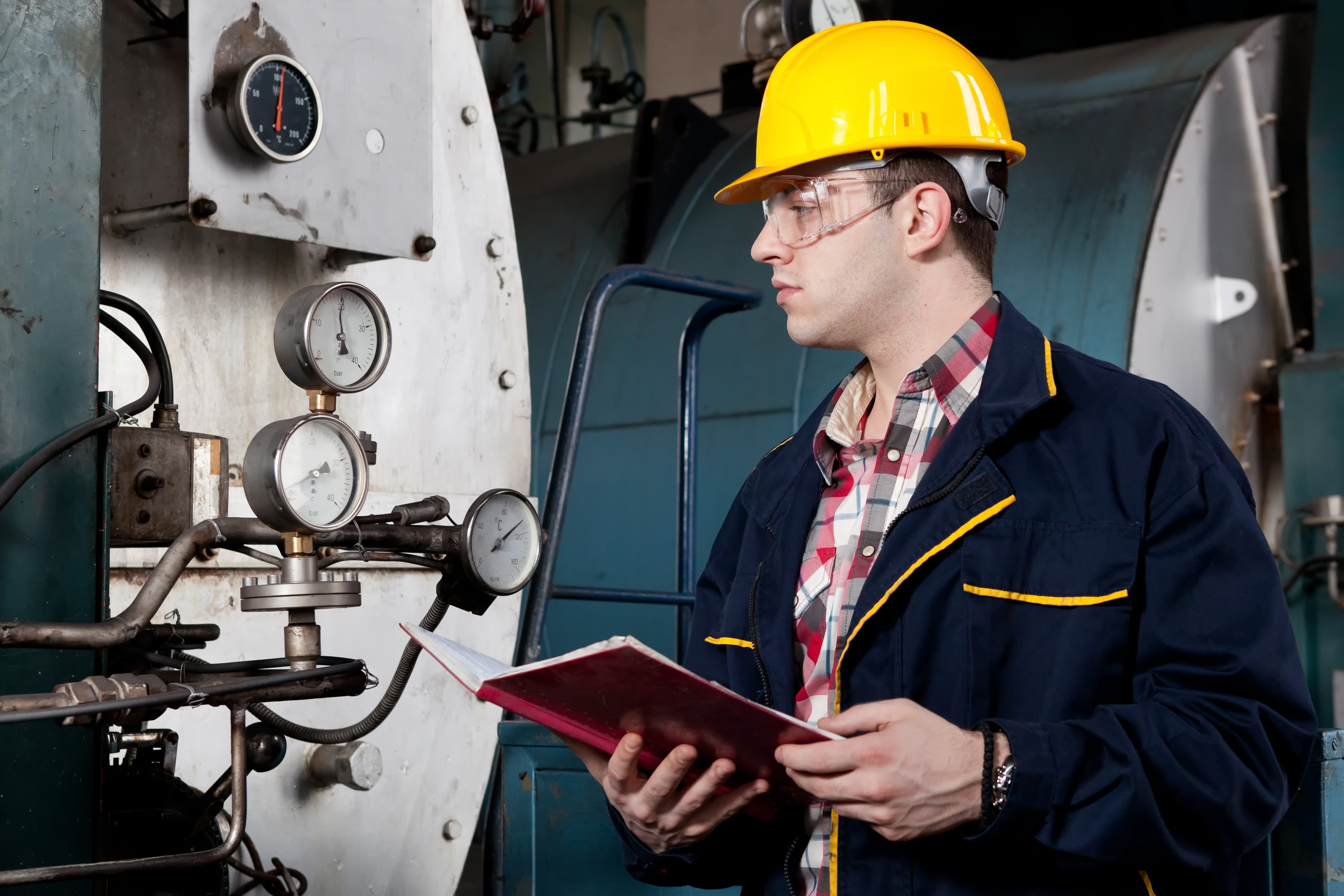
Table of Contents
- The Importance of Industrial Inspection
- Relevant Industries for Industrial Inspections
- Types of Industrial Inspections
- How to Implement an Effective Industrial Inspection Process
- Choosing the Right Industrial Inspection Services
- Risks and Challenges of Inspectors
- Automating Inspection through Mobile Robots and Drones
- Inspection Robots as Teammates
- Industrial Inspection Drones for Hard-to-reach Areas
- AI-driven Data Analysis
- End-To-End Solution For Industrial Robotic Inspection
- Selecting The Right Robot For Inspections
- The Future Of Industrial Inspection Is Mobile And Autonomous
The Importance of Industrial Inspection
The importance of industrial inspection can’t be overstated. It is the cornerstone of quality control and safety in the industrial sector. Inspection ensures that the manufacturing process adheres to the pre-defined standards and regulations, thereby reducing the risk of faulty products.
Industrial inspection also plays a vital role in the prevention of workplace accidents. By identifying potential hazards and ensuring the proper functioning of safety equipment, the inspection process helps to maintain a safe working environment. This, in turn, boosts the morale and productivity of employees.
Moreover, regular industrial inspection can save companies substantial money in the long run. By detecting and rectifying issues early, the inspection process prevents costly breakdowns and shutdowns. It also extends the lifespan of equipment and machinery, thus reducing the need for replacements.
The Role of Industrial Inspection in Safety and Maintenance
Industrial inspection has a dual role in safety and maintenance. On the safety front, it aids in the identification of potential hazards, such as faulty equipment, dangerous substances, and unsafe working conditions. This allows for the implementation of corrective measures before any harm can occur. Regular inspection also ensures that safety equipment, such as fire extinguishers and personal protective gear, is in good condition and readily available.
Maintenance-wise, industrial inspection helps to keep machinery and equipment in optimal working condition. By checking for signs of wear and tear, inspectors can recommend necessary repairs or replacements. This not only prevents unexpected breakdowns but also enhances efficiency and productivity.
Furthermore, the gathered data during the inspection process can be used to develop a preventive maintenance schedule. This proactive approach to maintenance helps to anticipate potential issues and address them before they escalate into major problems.
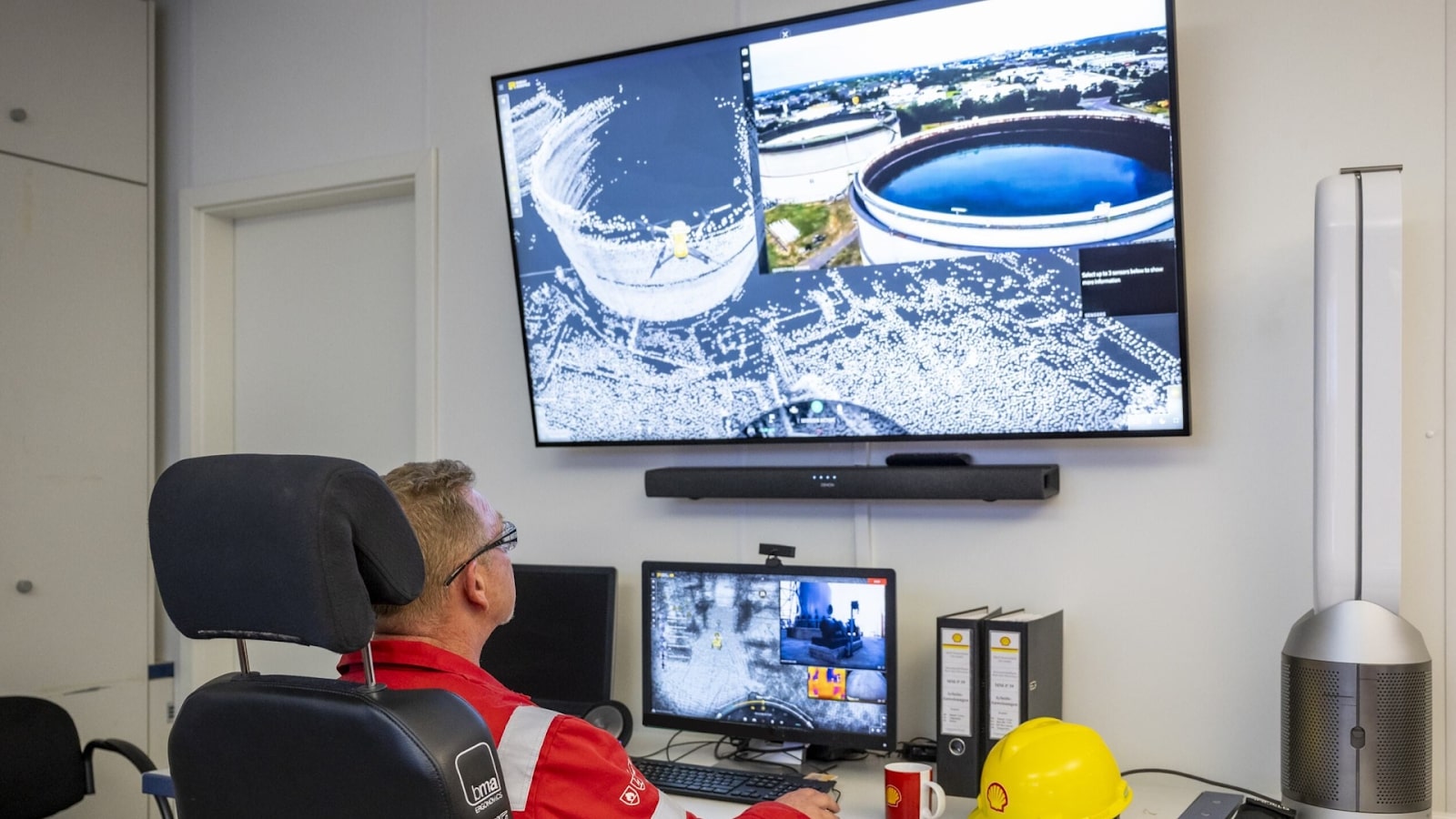
The Impact of Industrial Inspection on Quality Control
Industrial inspection is a core component of quality control in industries. It helps to ensure that products meet the required standards and specifications. By thoroughly inspecting raw materials, manufacturing processes, and finished products, inspectors play a key role in upholding the quality of industrial outputs.
Through industrial inspection, companies can identify and rectify defects at an early stage. This reduces the risk of producing substandard products that could damage the company's reputation and result in financial losses. Regular inspection also aids in continuous improvement by highlighting areas that require enhancement.
Moreover, the documentation of inspection findings provides a record of quality control efforts. This can be useful for regulatory compliance, customer assurance, and process optimization.
Relevant Industries for Industrial Inspections
The need for industrial inspection is not limited to a specific industry. It is a universal requirement across various sectors, such as:
- Power and Utilities
- Oil and Gas
- Chemicals
- Manufacturing
- Pharmaceuticals
- Construction
Each industry has its risks and challenges, making industrial inspection a complex and demanding task.
Types of Industrial Inspections
Industrial inspections can be categorized into several types, each serving a specific purpose. These include:
- Pre-production Inspection: This involves inspecting raw materials and components before the start of the production process. It helps to ensure that the materials are of the right quality and specification.
- In-process Inspection: Conducted during the production process, this type of inspection checks the quality and consistency of products. It helps to detect defects early and prevent wastage.
- Final Inspection: This is the inspection of finished products before they are shipped or sold. It validates that the products meet the required standards and are safe for use.
- Safety Inspection: This involves inspecting the workplace and safety equipment to ensure a safe working environment. It aids in the prevention of workplace accidents and illnesses.
- Maintenance Inspection: This type of inspection checks the condition of machinery and equipment. It helps to detect signs of wear and tear and plan for necessary repairs or replacements.
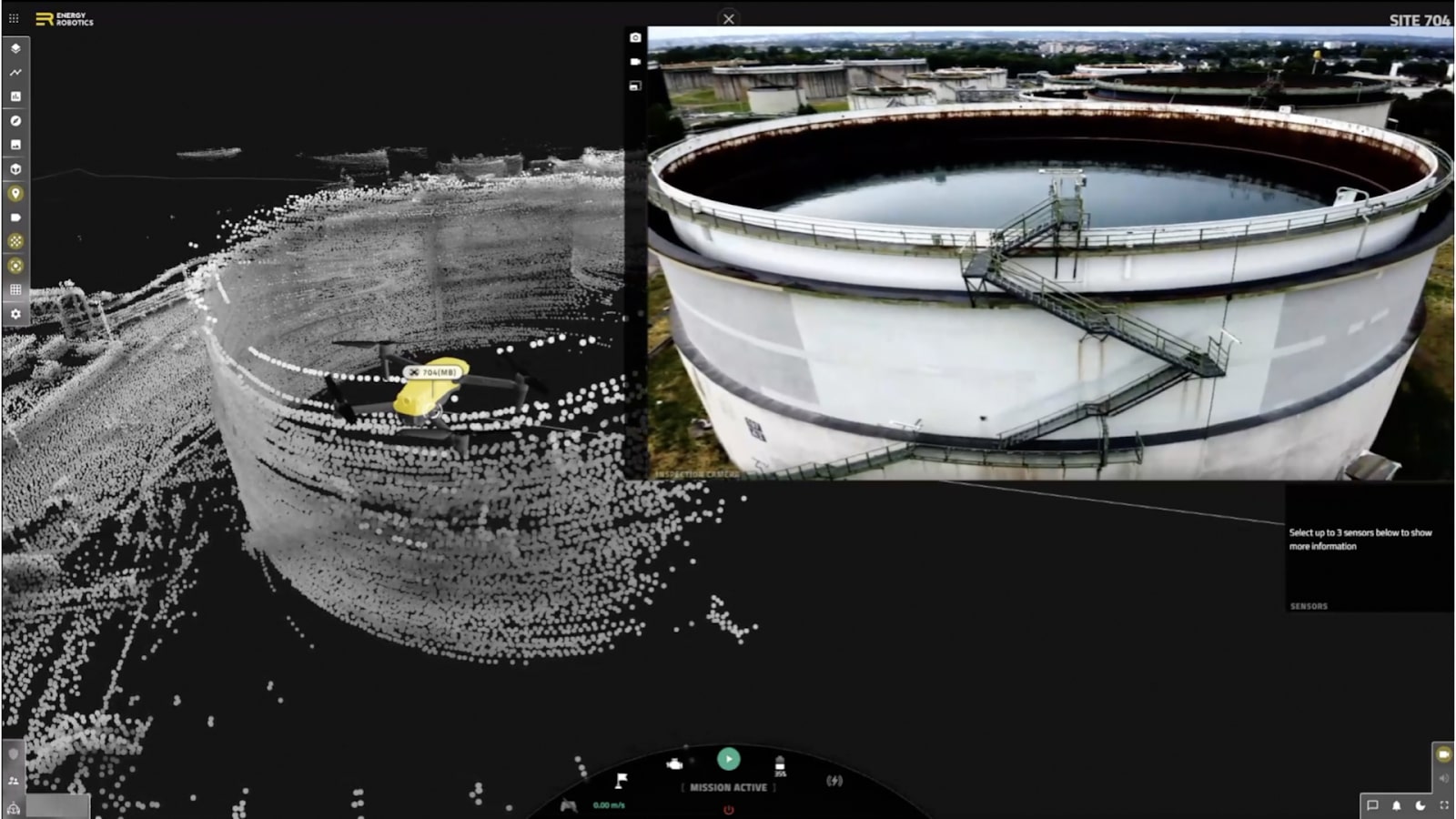
How to Implement an Effective Industrial Inspection Process
Implementing an effective industrial inspection process requires careful planning and execution. Here are some steps to consider:
- Define Inspection Objectives: The first step is to clearly define the objectives of the inspection. This could be ensuring quality control, maintaining safety standards, or extending equipment lifespan.
- Develop Inspection Procedures: The next step is to develop detailed inspection procedures. These should outline what needs to be inspected, how the inspection should be conducted, and who should perform the inspection.
- Train Inspectors: Inspectors need to be adequately trained to perform their duties effectively. This includes understanding the inspection procedures, using inspection tools, and interpreting inspection data.
- Schedule Regular Inspections: Inspections should be scheduled regularly to ensure continuous monitoring. The frequency of inspections can be determined based on the nature of the industry and the regulatory requirements.
- Document Inspection Findings: All inspection findings should be properly documented for future reference. This includes recording defects found, corrective actions taken, and recommendations for improvement.
- Review and Improve the Inspection Process: The inspection process should be reviewed periodically to identify areas for improvement. This could involve updating the inspection procedures, enhancing inspector training, or adopting new inspection technologies.
Choosing the Right Industrial Inspection Services
Choosing the right industrial inspection services is critical to achieving the desired outcomes. Here are some factors to consider:
- Expertise and Experience: The inspection service provider should have the necessary expertise and experience in your industry. This ensures that they can effectively identify potential issues and recommend suitable corrective measures.
- Certifications and Accreditations: The provider should have relevant certifications and accreditations. This attests to their competence and adherence to professional standards.
- Availability and Responsiveness: The provider should be readily available to conduct inspections and respond to any issues or concerns. This is particularly important in the event of emergencies or urgent situations.
- Use of Technology: The provider should use modern inspection technologies to enhance the accuracy and efficiency of the inspection process.
- Customization and Flexibility: The provider should be able to customize their services to suit your specific needs. They should also be flexible in terms of scheduling inspections and reporting findings.
Risks and Challenges of Manual Inspections
Rising HSE Costs
The cost of health, safety, and environmental (HSE) compliance is a significant burden for many businesses. It is a necessary expense, but one that is progressively increasing due to various factors. Initially, the rising costs are directly associated with the rising risks and challenges of manual inspection. With manual inspection, not only is there a greater chance of human error, but there is also an increased risk of accidents and injuries, leading to hefty insurance claims and legal liabilities.
Moreover, manual inspection often requires investing in specialized equipment, training, and certification for inspectors, adding to the overall HSE costs. Frequently, this financial burden may force businesses to cut corners, compromising safety and the quality of inspections. This is a dangerous and costly mistake, as it could lead to severe fines and damage to the company's reputation.
Lastly, the cost of environmental damage is now being integrated into the financial equation. With manual inspections, there is a higher likelihood of missed or overlooked issues that could lead to environmental harm, like leaks or spills. The cost of cleanup and the potential fines are astronomical, not to mention the potential loss of business due to damaged public image.
Demographic Crisis
Another major challenge of manual inspection is the looming demographic crisis. With the aging workforce we're facing a shortage of skilled manual inspectors. This scarcity not only increases the cost of hiring and training new employees but also adds to workload of existing inspectors, increasing the chance of errors.
The demographic crisis is also evident in the gap between the retiring experienced inspectors and the younger, less-experienced workforce. The knowledge and expertise gained through years of experience cannot be easily transferred, leading to an experience gap. This gap can lead to mistakes and oversights during inspections, which can have severe consequences.
Manual inspection, with its perceived repetitive and labor-intensive nature, does not appeal to the younger workforce. This perception exacerbates the problem of finding and retaining skilled manual inspectors, as the younger workforce gravitates towards jobs that embrace technology and automation.
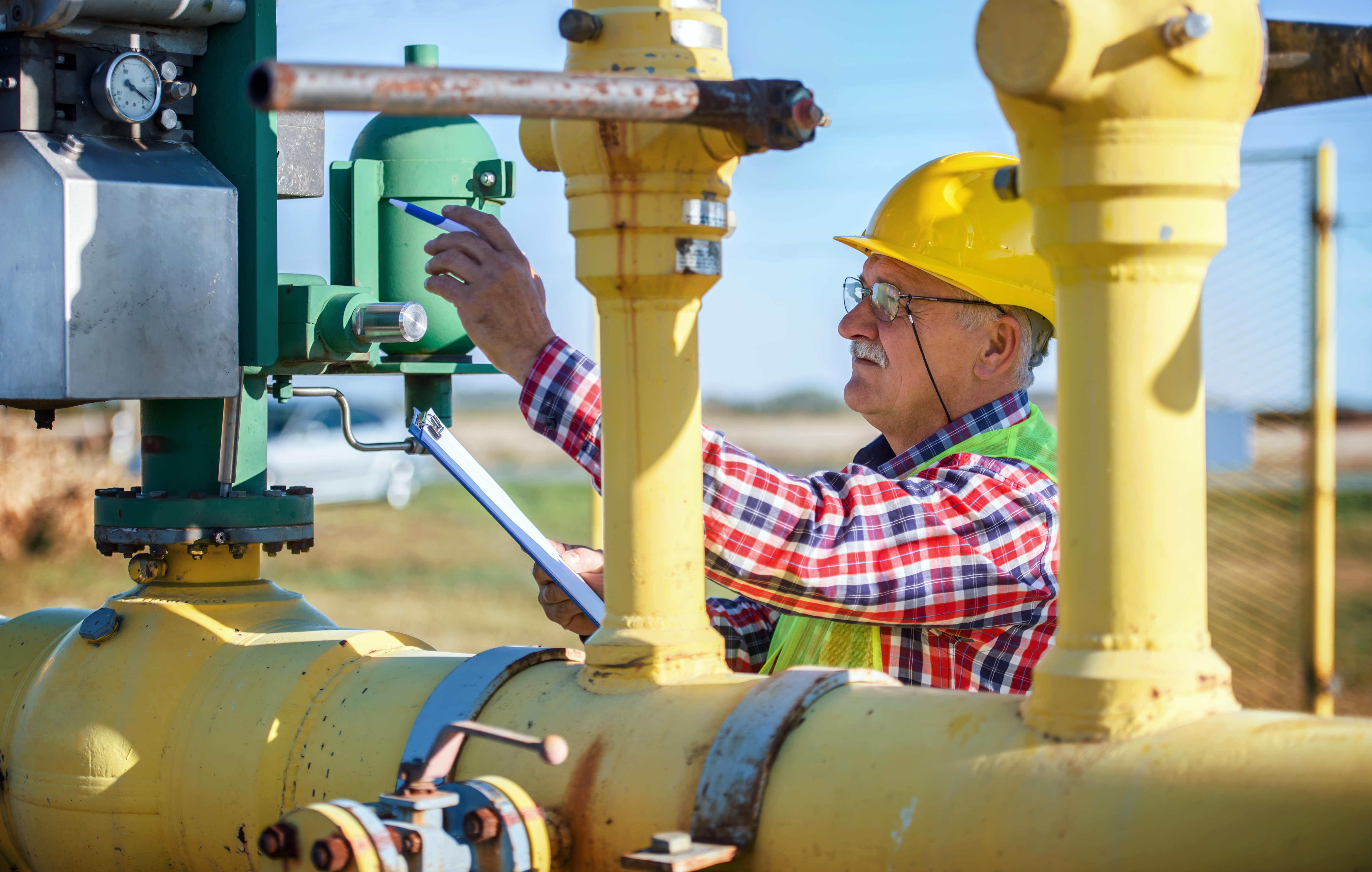
Error-prone Decision Making
Manual inspection is inherently error-prone. Human inspectors, no matter how skilled or experienced, are prone to mistakes. An estimated 70% of incidents in the oil and gas industry are related to human error. These mistakes can be due to various factors such as waning attention spans while performing repetitive tasks, fatigue, lack of concentration, or simply human error. It's common for an inspector to overlook a small defect, misread a measurement, or misinterpret an inspection guideline.
Moreover, the decision-making process during manual inspections can be highly subjective. An inspector's decision can be influenced by their personal bias, interpretation of guidelines, or even their mood on a particular day. This subjectivity can lead to inconsistencies in inspection results, affecting the overall quality and reliability of inspections.
The error-prone nature of manual inspection can lead to severe consequences. A missed defect or an incorrect assessment can lead to product failures, accidents, or environmental damage. These incidents not only cost a fortune in terms of financial losses but also damage the company's reputation and customer trust.
Stationary IOT Sensors are not a Fool-proof Solution
With the rise of Industry 4.0, many companies are turning to stationary IoT (Internet of Things) sensors as a solution to the challenges of manual inspection. However, these technologies, while promising, are not the foolproof solution they're often portrayed to be.
- As these sensors are stationary they do not provide full coverage detection. Gas sensors, for example, may not detect leaks that are out of the detection range.
- A typical industrial facility has 1000s of inspection points and to replace all of them with IoT sensors is extremely cost-prohibitive.
- Moreover, sensors are prone to malfunctions and false alarms, thus requiring asset owners to regularly inspect and carefully maintain the sensors themselves.
Industries are in need of mobile sensor platforms in the form of robots and drones, equipped with the relevant sensors, which autonomously collect high-quality data from every nook and corner of the facility.
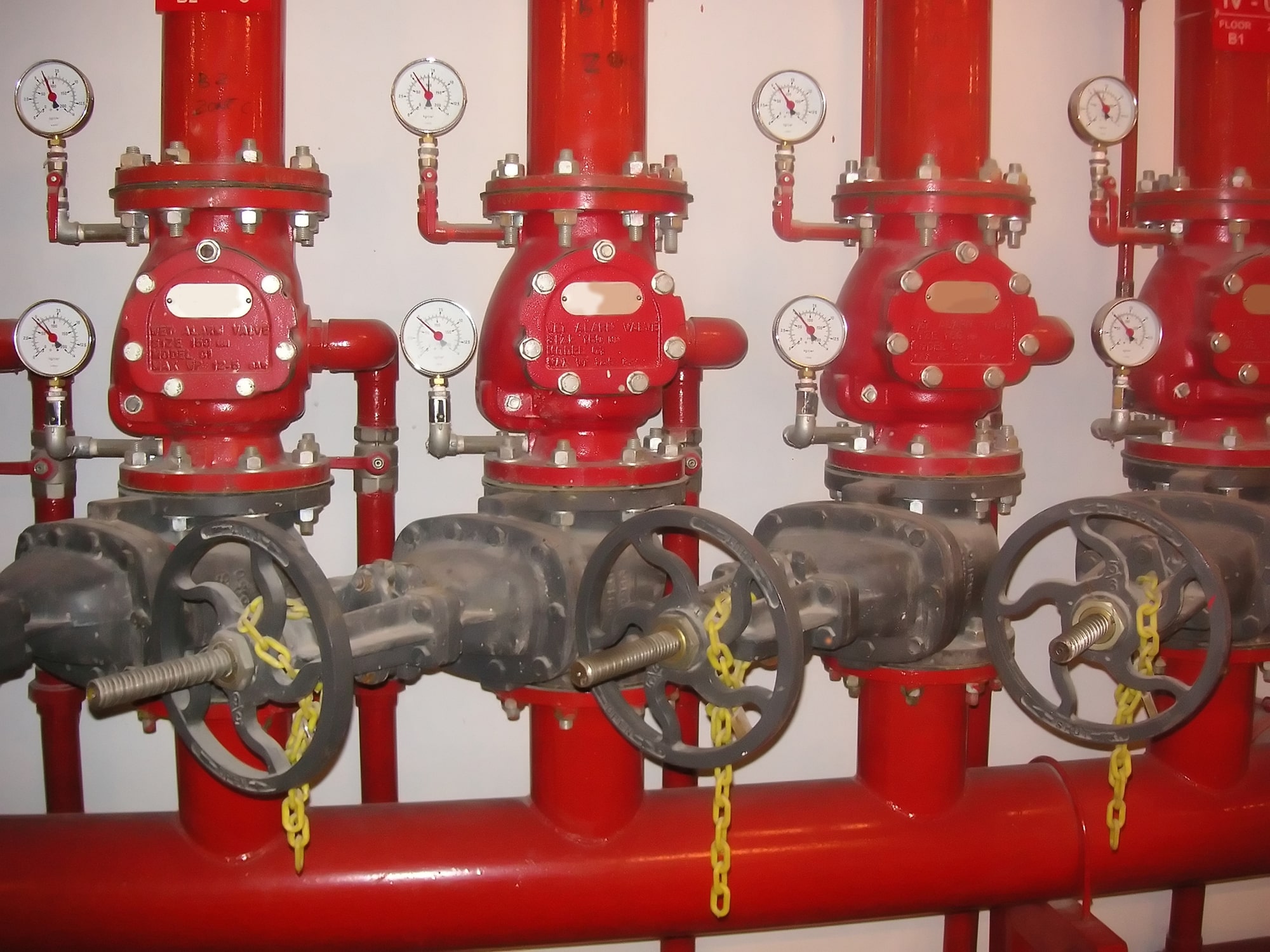
Automating Inspection through Mobile Robots and Drones
Inspection Robots as Teammates
Robots, equipped with advanced sensors and cameras, are capable of navigating complex terrain and collecting inspection data autonomously. Their ability to capture high-resolution images and videos, thermal patterns and detect different gases allows for precise analysis, ensuring thorough automated inspections.
Robotic inspection systems also offer the advantage of data consistency. By performing repetitive tasks with precision and in shorter intervals, these robots ensure that the inspection data collected is reliable and consistent. This is particularly beneficial in industries where maintaining stringent quality standards is crucial. On top of this, inspection robots also reduce the risk of human error, making the inspection process more efficient and accurate.
Inspection Drones for Hard-to-reach Areas
When it comes to inspecting hard-to-reach areas, drones offer a unique solution adding the 3rd dimension to automated inspection. These aerial devices can access spaces that are inaccessible to humans or ground-based robots. With their ability to fly and hover, drones can carry out inspections effectively, even in the most challenging conditions.
Drones equipped with high-definition cameras can capture detailed RGB-color and thermal data in the form of images and videos of the inspection site. This feature is especially useful in the construction and oil and gas industries, where tall structures are common. Drones can easily reach the top of these structures, providing a clear view of any potential issues or damages.
Just like ground-based robots, drones also offer the benefit of minimizing human risk. By taking over tasks that require climbing to the top of tanks or navigating through dangerous terrains, drones keep human operators safe. They also offer cost-saving benefits, eliminating the need for expensive scaffolding or other equipment usually required for such inspections.
AI-driven Data Analysis
Robots and drones reliably collect inspection data. However, asset owners are not interested in large volumes of raw data, what they need are actionable insights. This is where AI-driven data analysis comes in. AI applications, known as Skills, process images and videos captured by robots and drones, identify potential faults with high accuracy and deliver alerts to operators who can then take immediate action. This not only improves the efficiency of the inspection process but also ensures rapid response to any detected issues. AI can also predict potential failures based on the analyzed data, allowing for preventive measures to be taken before any serious damage occurs.
AI-driven data analysis also offers the advantage of continuous learning. With each inspection, the AI applications become smarter based on the feedback from operators, improving its capability to detect faults and anomalies. This continuous improvement leads to more accurate inspections, ensuring the long-term reliability of industrial systems.
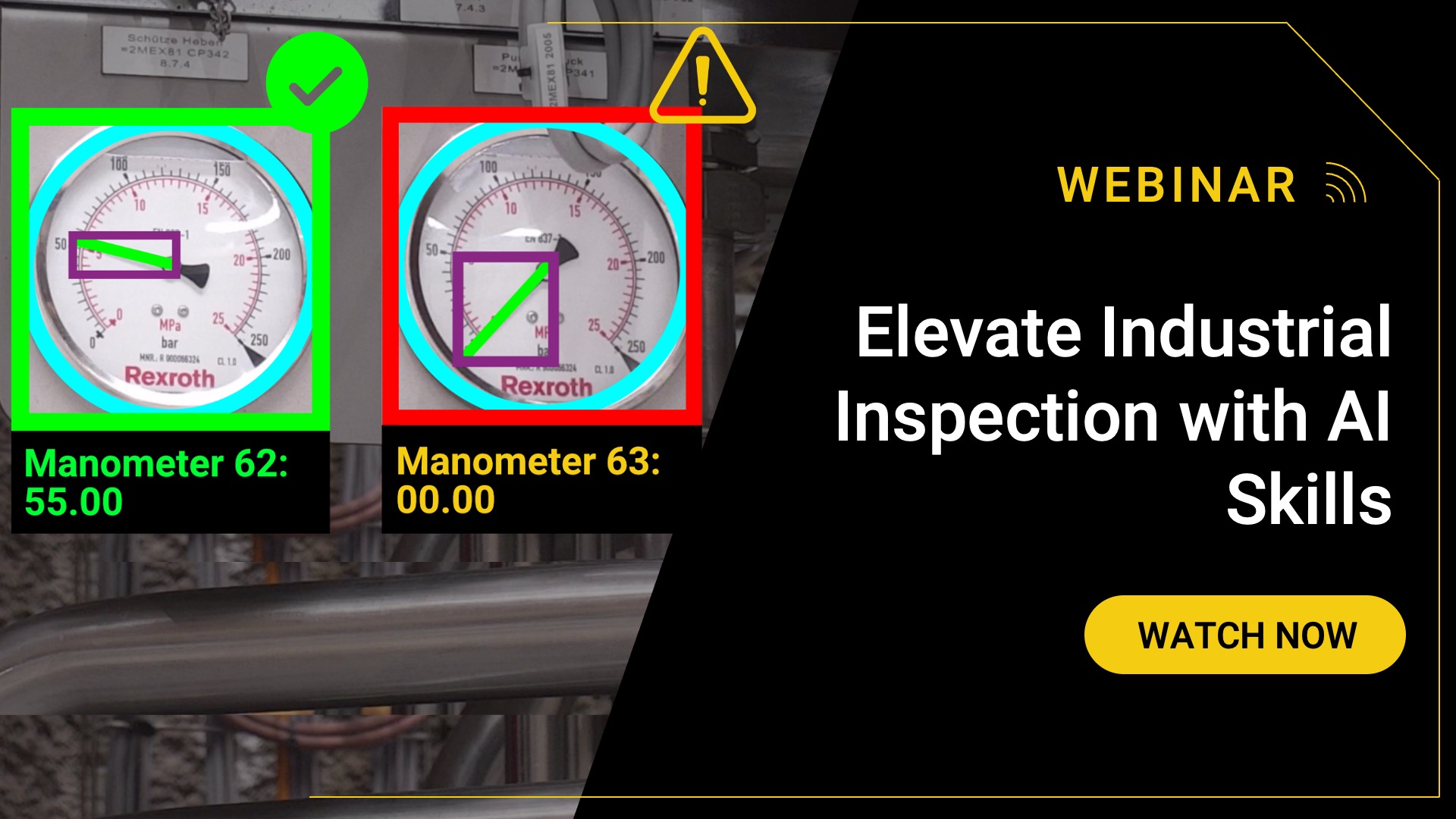
End-To-End Solution For Industrial Robotic Inspection
The combination of robots, drones, and AI offers an end-to-end solution for autonomous industrial inspection. From accessing hard-to-reach areas to analyzing vast amounts of inspection data, these technologies cover every aspect of the inspection process.
An end-to-end solution also ensures seamless integration of the entire inspection process. The data captured by robots and drones is directly fed into the cloud for analysis, ensuring quick and efficient fault detection.
Moreover, an end-to-end solution also offers scalability by being hardware-agnostic. As the inspection needs of an industry grow, the system can be expanded by adding different robots or drones to the fleet. This scalability ensures that the inspection process can keep up with the growing demands of the industry cost-effectively, without compromising on efficiency or accuracy.
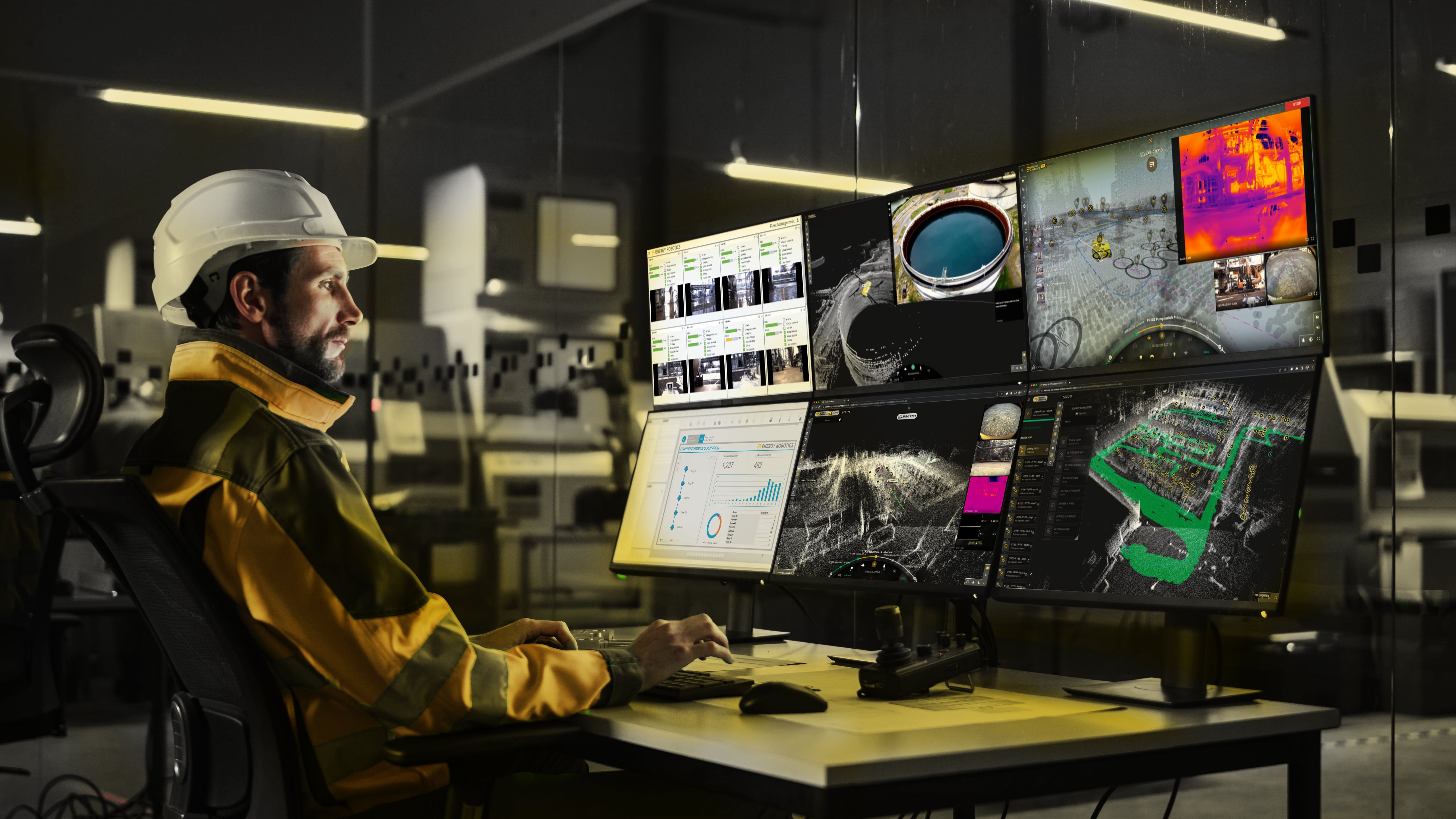
Selecting The Right Robot or Drone For Inspections
Selecting the right industrial robot or drone for inspections is crucial to ensure efficiency and accuracy. Several factors need to be considered when choosing a robot, including
- Nature of the inspection tasks
- Environment in which the robot will operate
- Cost-effectiveness in turning use-cases into business cases
The type of inspection task determines the capabilities required in a robot. For instance, if the task involves inspecting the top of a large structure, a drone with high-resolution cameras and strong flight capabilities might be the best choice. On the other hand, for tasks that require close and detailed inspection on the ground, a ground-based robot equipped with advanced sensors might be more suitable.
The environment in which the robot will operate also plays a significant role in the selection process. Robots designed for harsh environments need to be robust and durable, capable of withstanding extreme conditions. Similarly, robots operating in complex terrains need to have advanced navigation capabilities to wade through obstacles effectively. Furthermore, specialized robots are needed for highly sensitive areas such as potentially explosive ATEX zones commonly found in the Oil and Gas industry.
Lastly, the costs of deploying the robot should not be prohibitive in comparison to the use-case solved by it. In most cases, deploying a fleet of low-cost “specialist” robots is more economically viable than deploying expensive generalist robots.
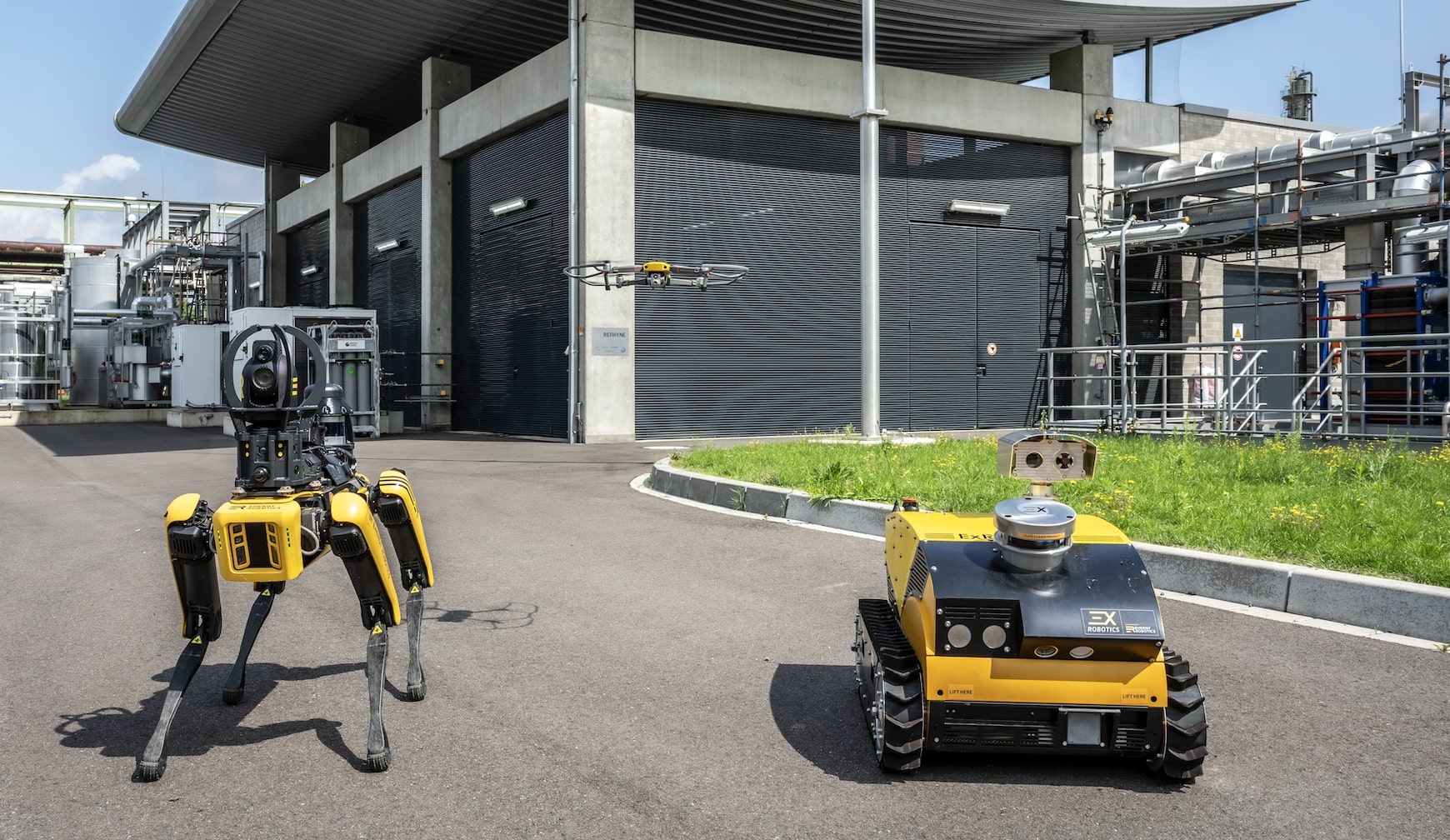
Conclusion: The Future Of Industrial Inspection Is Mobile And Autonomous
In conclusion, the future of industrial inspection lies in mobile and automated technologies. With the ability to navigate through complex terrains, perform tasks with precision, and analyze vast amounts of data, autonomous robots, and drones are set to play an even bigger part in the industrial inspection process.
These technologies not only improve the efficiency and accuracy of inspections but also ensure the safety of human operators, while freeing them to take up more specialized tasks. Furthermore, with continuous advancements in AI and robotics, these systems will only become smarter and more capable, further enhancing their role in industrial inspections.
The adoption of mobile and autonomous technologies for industrial inspections has already started. As industries continue to strive for efficiency and safety, while tackling a shortage in workforce, the role of autonomous robots and drones in inspections will only grow stronger. Embracing these technologies today can set the stage for a safer and more efficient industrial future.