Maintenance can be a complex undertaking, requiring thorough planning and an astute understanding of a facility’s risk profile. This is particularly true of high-risk facilities, such as those in the oil and gas, chemical and energy industries. Maintenance does not occur in a ‘vacuum’ and can result in costly downtimes if it is unexpected or unplanned. Even planned maintenance can lead to lengthy downtimes resulting in huge losses. For example, oil refineries in the US alone lose an estimated $47 billion from 213,000 hours of downtime each year. What is required is a maintenance regime that is comprehensive, yet unobtrusive. This is where predictive maintenance comes in.
What is predictive maintenance?
Even the most updated and expensive machinery and equipment can be unpredictable. Increasingly sophisticated assets require maintenance that is as responsive and intelligent as possible. The precise prediction of when assets may need maintenance can greatly streamline a maintenance department’s workload and its ability to respond to the complexities of modern machinery. Predictive maintenance provides that solution.
Predictive maintenance uses artificial intelligence (AI) to assess operational data continuously and in real time. As its name implies, it is maintenance predicated on the ability to predict outcomes. It can do this, for example, with the aid of smart sensors and similar technology in or near assets that continually monitor their current status. This enables potential malfunctions or failures to be predicted, thus minimising the risk of unforeseen or sudden breakdowns. For example, sensors that perform vibration analysis and acoustic analysis help ensure that mechanical assets are protected from becoming faulty due to excessive vibration or grinding between components. Likewise, thermal sensors can help detect ‘hotspots’ or overheating in machinery, thereby thwarting future breakdowns because of scorched components or circuits.
In recent years, industries have been trying to implement predictive maintenance solutions through the Industrial Internet of Things (IIoT), which is the entire network of physical devices embedded with digital software, sensors and network connectivity that enable the exchange of data between devices in an industrial facility. Computer vision (CV) or other data-driven machine learning models are also often key factors. IIoT undoubtedly improves what is referred to as the ‘holy grail’ of facilities management. For example, AI can process data on the condition of assets with algorithms that detect anomalies before they worsen, i.e., what predictive maintenance is fundamentally about. This approach can reduce the mean time to repair rate (MTTR) of assets by up to 60 percent, thus significantly reducing expensive downtimes.
The huge cost of downtime
Downtime is debilitating, even crippling, for capital- and production-intensive facilities. The numbers are truly mind-numbing: for example, in the United States one hour of downtime costs electric utilities $300,000. A report titled "The True Cost of Downtime" found that the Fortune Global 500 manufacturing and industrial firms are losing nearly $1 trillion a year due to unplanned downtime, equating to a loss of 3.3 million person hours and an average loss of 8% in annual revenues.
And the industry that is hardest hit by downtime? The oil and gas sector, with an average downtime of 32 hours per facility each month, costing a facility $220,000 per hour or $84 million each year. According to research, just 3.65 days of unplanned downtime a year can cost an oil and gas company over $5 million. It gets worse: in 2020, Reuters reported that some oil refineries had seen their insurance rates for property damage and business interruption increase by as much as 100% due to explosions or fire.
Advantages of predictive maintenance
Taking cognisance of the astonishing impact of downtime, smart organisations have turned towards predictive maintenance strategies. They understand the value of harnessing AI to identify early warning signs in assets before malfunctions or disruptions occur, rather than relying on time-based maintenance that adheres to fixed schedules.
There are multiple benefits to predictive maintenance, the most obvious of which is that it predicts potential failures before they happen. By doing so, it extends the lifespan of assets, extracting maximum value from machinery and equipment. The result is a reduction in the overall risk profile of a facility, including safety risk factors and, ultimately, an improvement to a facility’s financial bottom line. And yet so many companies continue not to have this in place. It’s been found that fewer than 24% of oil and gas operators have a maintenance approach based on predictive data and analytics, according to GE statistics.
The Importance of Data
High quality data is an essential requirement for the effective implementation of predictive maintenance. In this regard it faces challenges when it is implemented solely based on IIoT and manual inspections. An over-reliance on data collection through IIoT, may sideline or reduce physical inspections, which is invaluable for the collection of data in locations that are out of the coverage area of stationary sensors. Even when frequent manual industrial inspection rounds are conducted to complement the IIoT infrastructure, data inconsistencies due to human-error are inevitable.
Predictive maintenance with autonomous mobile robots
To overcome these challenges, high-risk facilities are turning to autonomous mobile robots and drones for reliable inspections, and as active allies for facility management. Autonomous robotic inspection enables an ongoing physical inspection schedule, even in hazardous locations or difficult-to-reach areas, while at the same time freeing up maintenance personnel to perform specialized work which is less tedious and not dangerous.
In addition to the impressive flexibility and mobility, which enables mobile robots and drones to monitor locations and assets which may lie outside the coverage area of stationary digital sensors, they are also cost-effective and easier to onboard. Instead of having to equip facilities with thousands of expensive sensors, asset owners can onboard a single mobile robot as a roving sensor platform.
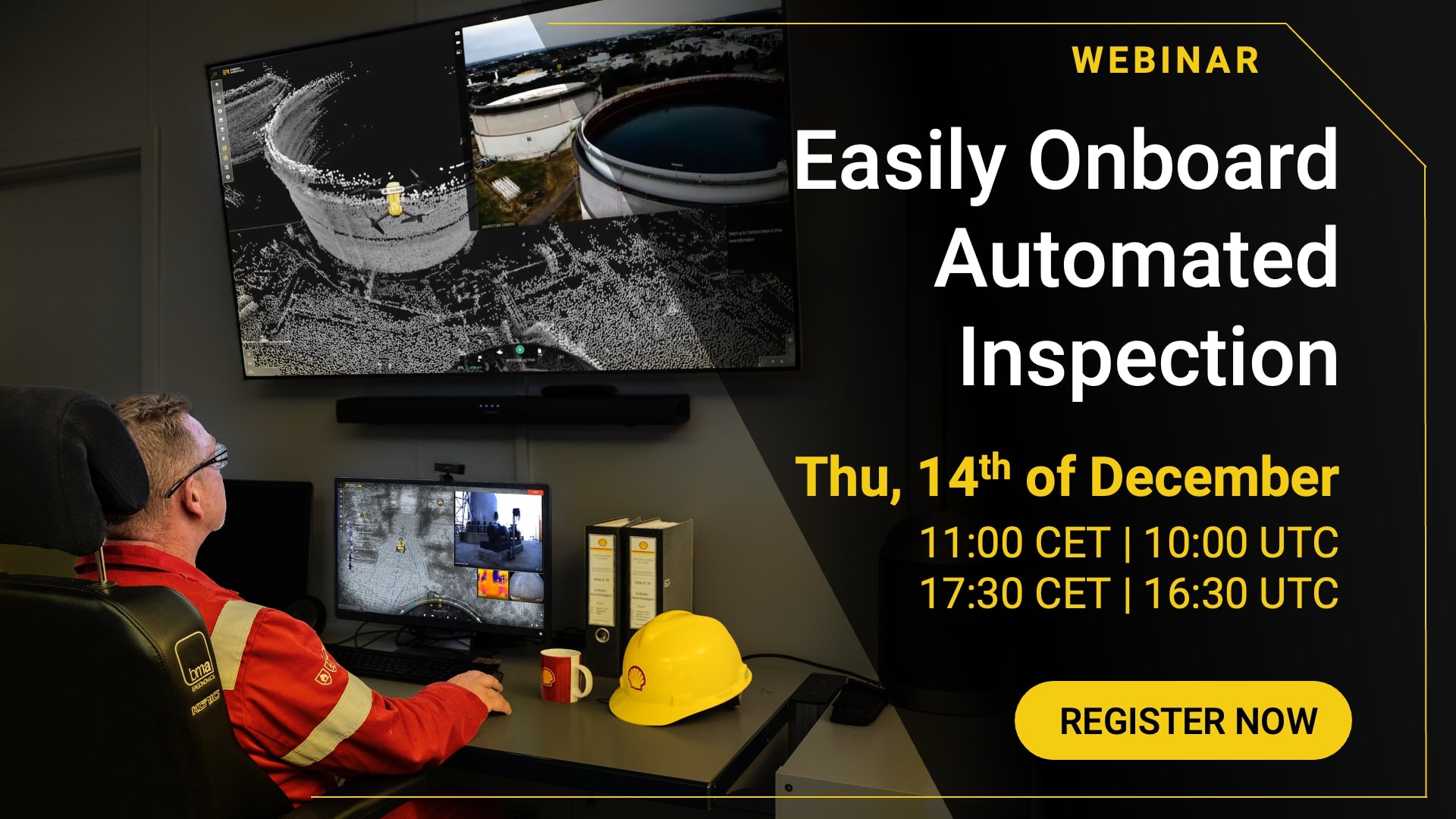
Mobile robots not only collect high quality data, but they also convert the collected data to actionable information, leaving no room for data misinterpretation. This is made possible through AI and computer vision applications called Skills. Skills are ‘containerised’ applications that process sensor data and influence a robot’s behaviour to perform specific tasks. For example, robots equipped with the skill to read analog devices are able to detect the needle position of analog devices with precision and record the reading accurately. An alarm can then be sounded if the reading is above or below a pre-defined threshold value. Such an autonomous mobile robot is more than a mere ‘data collector’.
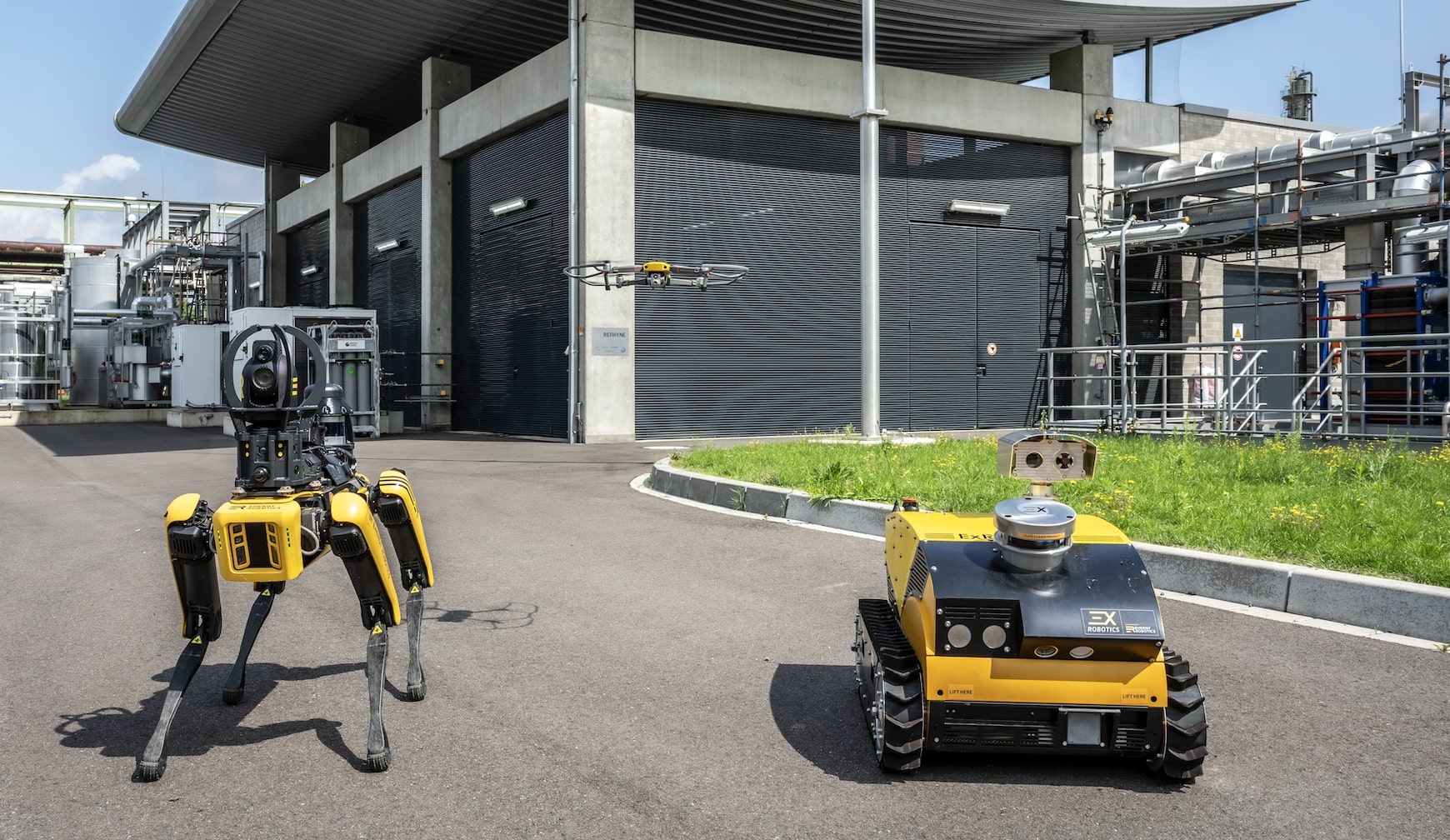
Therefore, the pay-off is that a single robot or drone can reliably and repeatedly collect multiple types of data from assets in different locations in the facility and deliver actionable information to the fingertips of operators. The data can be processed in real-time or integrated directly with an enterprise asset management (EAM) system, which incorporates a computerised maintenance management system (CMMS) for all maintenance scheduling and execution. The result is an intelligent, intuitive and streamlined predictive maintenance regime.
Accelerating the journey towards Industry 4.0
Facilities have gotten ‘smarter’ courtesy of AI, IIoT, machine learning (ML) and automation. Industry 4.0 demands smart maintenance to match. Predictive maintenance is an excellent option for ensuring intelligent maintenance that is always proactive, never reactive. Robotic inspection- and AI-enhanced predictive maintenance allows for far-improved data analytics and data that can make a discernible difference regarding maintenance decisions in a high-risk facility.
However, predictive maintenance is not about replacing maintenance workers and the incomparable human element they bring to the maintenance function. Rather, improved data collection and analytical capabilities allow maintenance managers and teams to make better-informed decisions regarding assets. Autonomous mobile robots with embedded sensors and customised AI Skills can do much to streamline and facilitate maintenance operations. Their versatility and formidable return on investment alone are worth serious consideration for capital-intensive facilities.