Digitalization and automation are key focus areas at the Shell Energy and Chemicals Park Rheinland. The company is therefore relying on innovative automated inspection solutions from Energy Robotics at its largest site in Germany.
With the Energy Robotics software platform as well as two different robots and a drone, Shell is implementing powerful 360° monitoring of the plants at Rhineland. Shell is working closely with Energy Robotics as the start-up is a leader in the development of software solutions for the use of heterogeneous fleets of mobile, autonomous inspection robots in industrial applications.
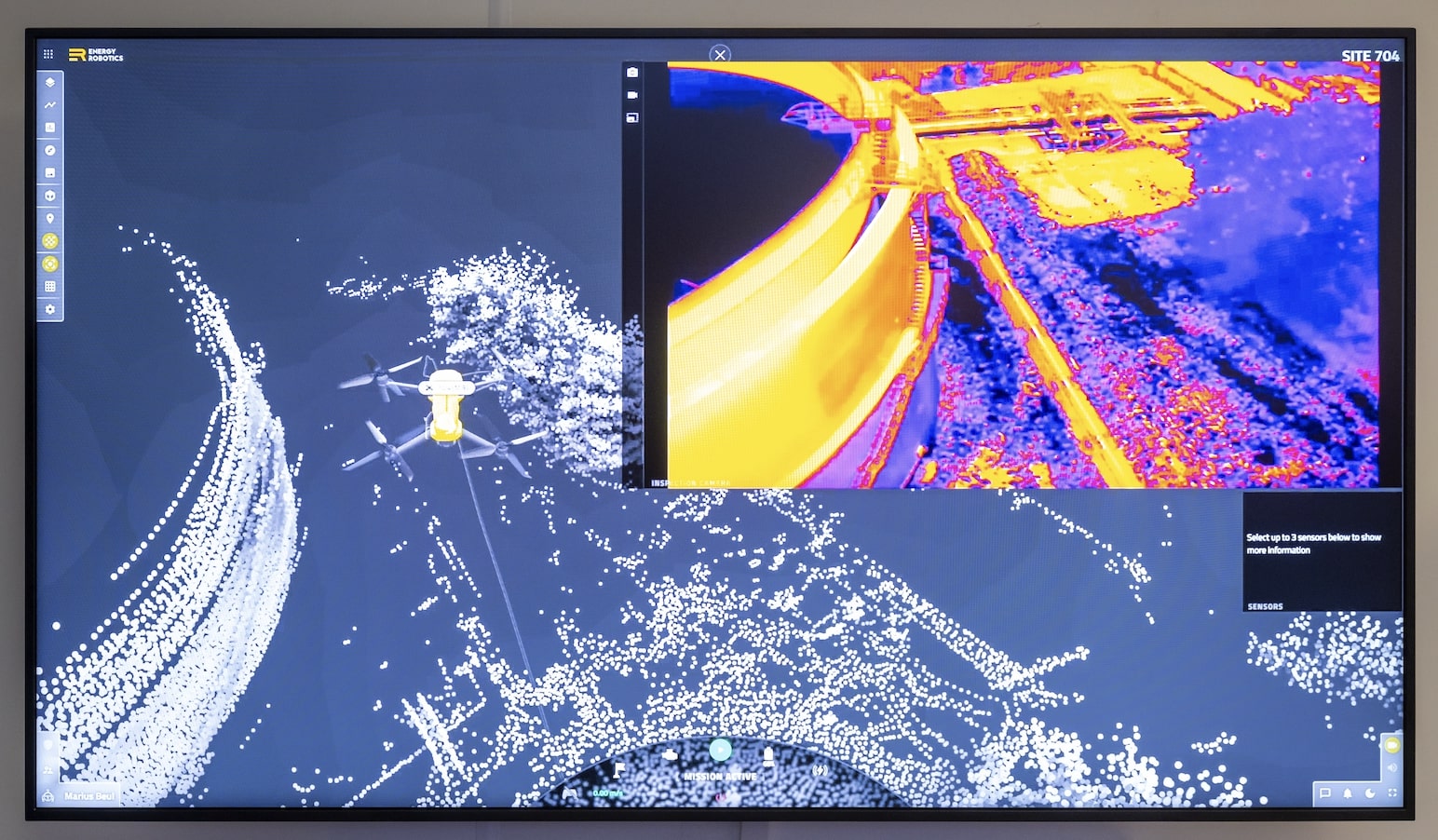
In a constant effort to remain fit for the future, not only does Shell regularly invest in the modernization of its plants, but also in topics such as digitalization and automation. This also includes the automation of inspection processes at the Shell Energy and Chemicals Park Rheinland with the help of robots and drones. Shell benefits from a large amount of inspection data, which is delivered with consistently high quality by the Energy Robotics software. The use of autonomous robots and automated drones also offers the company the opportunity to further raise safety standards and improve the working environment for employees.
Robots and Drones for Every Application
The hardware-agnostic software platform from Energy Robotics enables the use of different robots via standardized operator, data and AI analysis interfaces. It makes it possible to organize and manage the fleet of different robots and drones very efficiently and to plan inspection missions completely remotely, even when the robot or drone is offline - anywhere in the world.
The different robot types and the drone are equipped with visual and thermal cameras and other special sensors. Among other things, they use these sensors to create images of analog barometers and thermometers to read out pressure and temperature readings with artificial intelligence and computer vision. In the same way, they record and analyze valve positions or objects such as fire extinguishers and record thermal images of insulation and machines in order to detect thermal anomalies. They even register small quantities of escaping gases in the ppm range. Data is automatically transferred to a cloud platform where it is analyzed with the help of algorithms and artificial intelligence (AI). If measurements deviate from the predefined standard range, the maintenance employee (operator) is informed immediately.
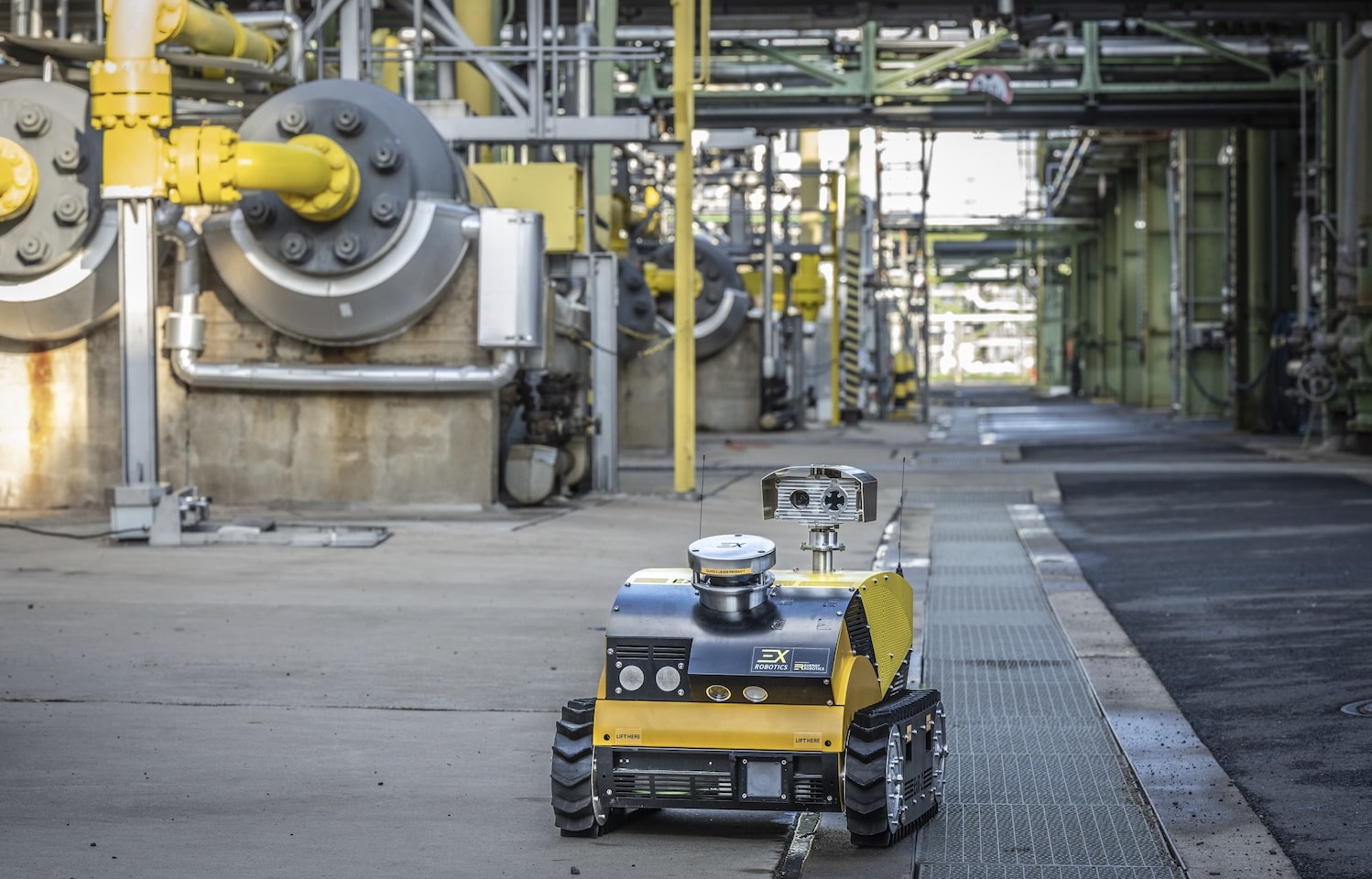
Two different robots and a drone are currently being used at the Energy and Chemicals Park Rheinland. This mixed fleet is necessary due to the heterogeneous environment of the plants. The tracked robot, ExR-2, from ExRobotics performs inspection tasks in Ex zones, i.e. areas with explosion hazards. The walking robot, Spot, from Boston Dynamics, on the other hand, navigates reliably over stairs and through narrow areas in non-hazardous environments. Finally, a drone inspects the roofs of the tank farms and inspection points that are difficult to access from the air, adding a third dimension to the inspection process.
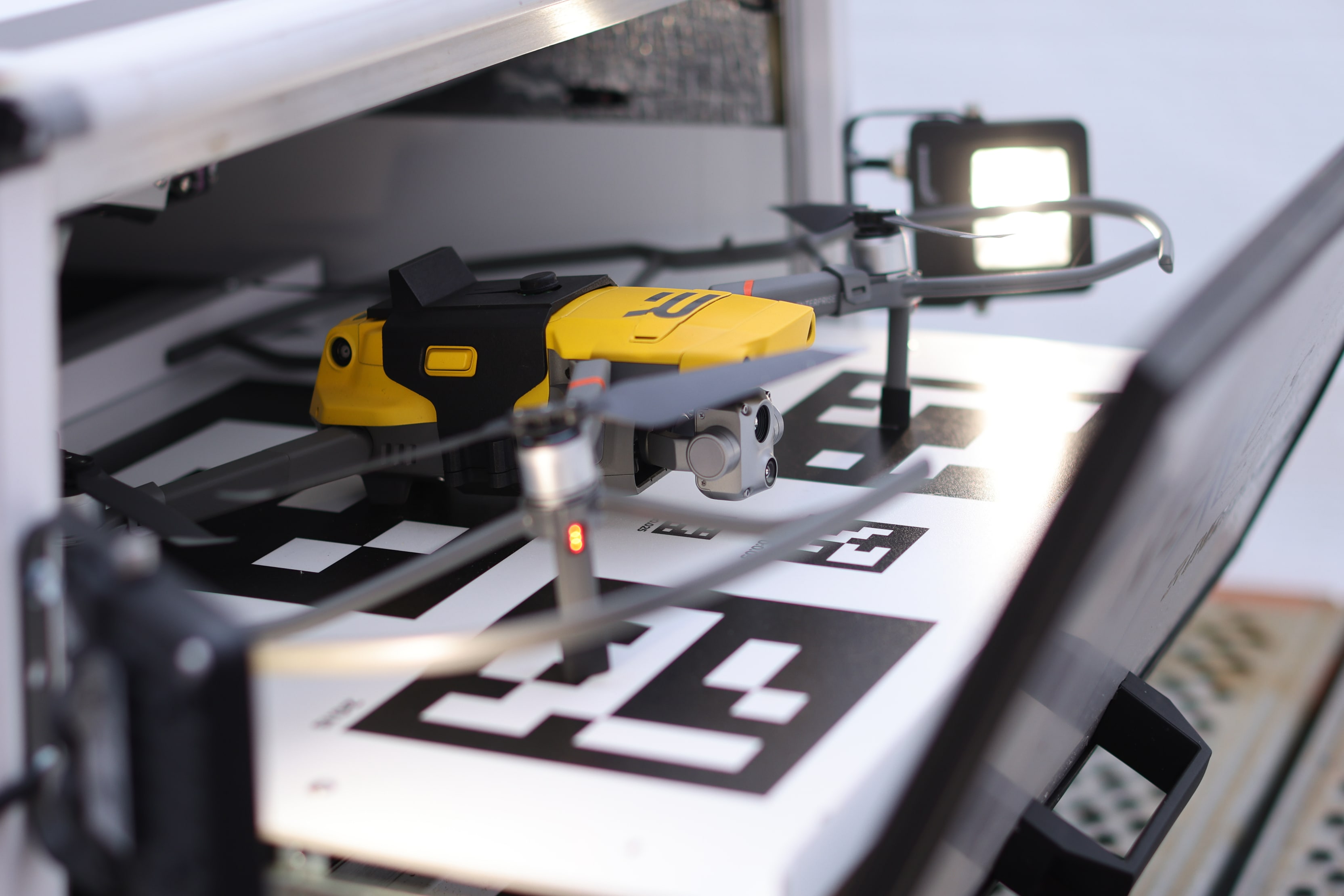
Vision for Automation
Through the cooperation with Energy Robotics and the use of automated robotic inspection, Shell is further expanding the digitalization of the Rhineland site.
"We are proud to have put a mixed fleet of autonomous inspection robots and a drone into operation as part of our innovation and digitalization efforts. The different specifications of the individual models give us the flexibility we need to inspect a large number of inspection points automatically," explains Thomas Klein, Digital Innovation Lead, Shell Energy and Chemicals Park Rheinland.
"The very successful use of different robots in the Shell Energy and Chemicals Park is further proof for us that our solution can be used in many different industries with great benefits for our customers. The use of different hardware platforms in one and the same plant and the wide range of inspection tasks are excellent examples of the 360° monitoring we offer our customers. We are delighted with the trust placed in us as part of this joint project," adds Marc Dassler, CEO Energy Robotics.