What are Inspection Rounds?
Inspection rounds, also known as field operator rounds or plant rounds, are routine inspections and monitoring activities performed by operators in industrial facilities, such as manufacturing plants, refineries, or power generation sites. These rounds are essential for ensuring the safe and efficient operation of equipment, identifying potential issues, and maintaining overall plant integrity.
During operator rounds, operators physically inspect various areas of the facility, checking equipment status, monitoring instrumentation readings, and observing any abnormalities or deviations from normal operating conditions. These rounds are typically conducted at regular intervals, following predefined routes and checklists.
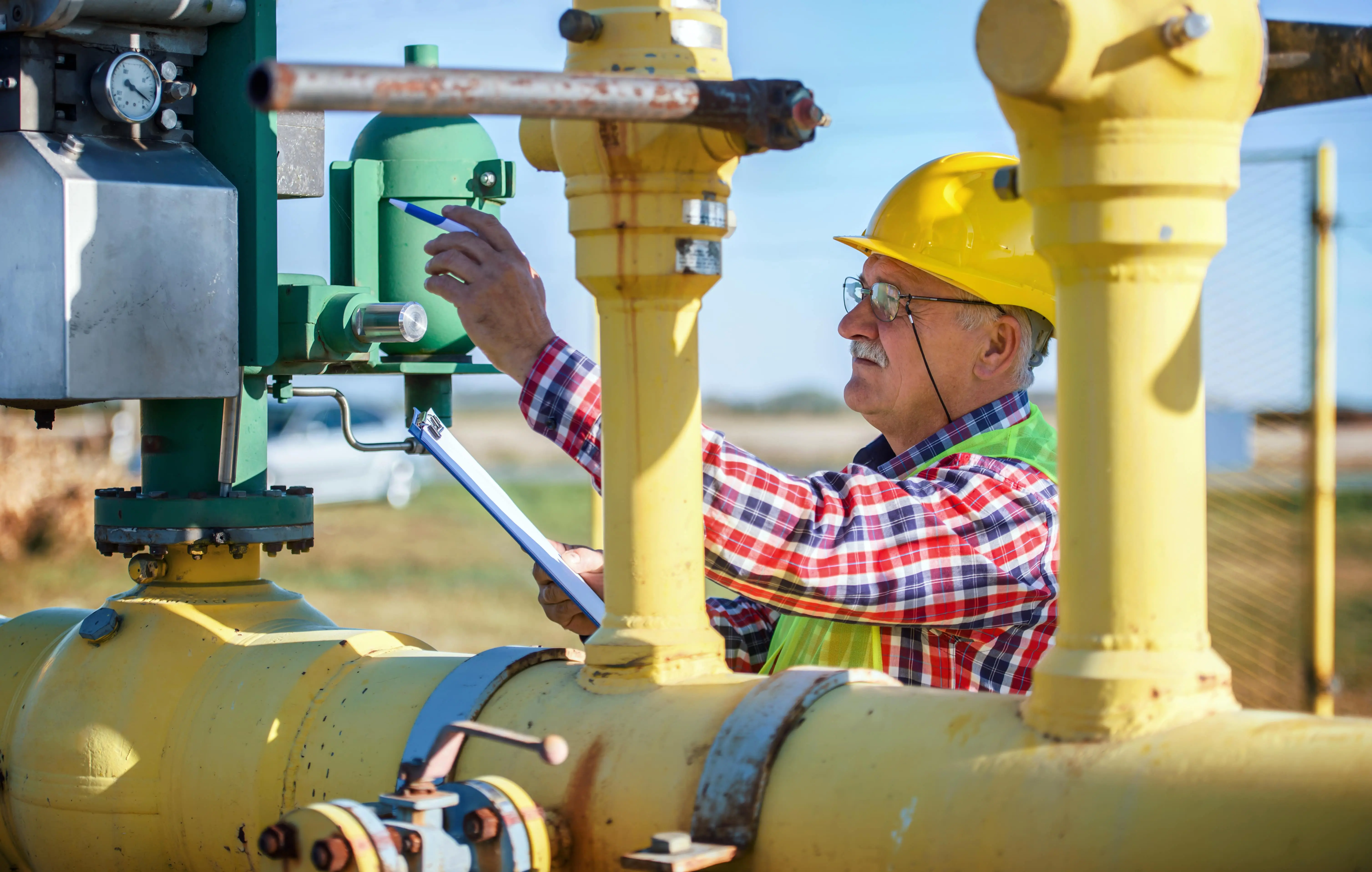
How is an Inspection Round performed?
Traditionally, operator rounds have been carried out manually, with operators physically walking through the facility, visually inspecting equipment, and recording observations on paper or handheld devices. The process typically involves the following steps:
Route Planning: Operators are assigned specific routes or areas to cover during their rounds, ensuring comprehensive coverage of the facility.
Checklist Review: Before starting the round, operators review the relevant checklists or inspection forms to ensure they understand the items to be inspected and the criteria for evaluation.
Equipment Inspection: Operators physically inspect the assigned equipment, checking for any signs of wear, leaks, abnormal temperatures, or other potential issues.
Data Collection: Operators record various parameters, such as temperature, pressure, flow rates, or other relevant readings, either manually or using handheld devices.
Observation Logging: Any observations, abnormalities, or potential issues are documented for further investigation or corrective action.
Communication and Reporting: Upon completion of the round, operators communicate their findings to supervisors or relevant personnel, and formal reports are generated for record-keeping and follow-up actions.
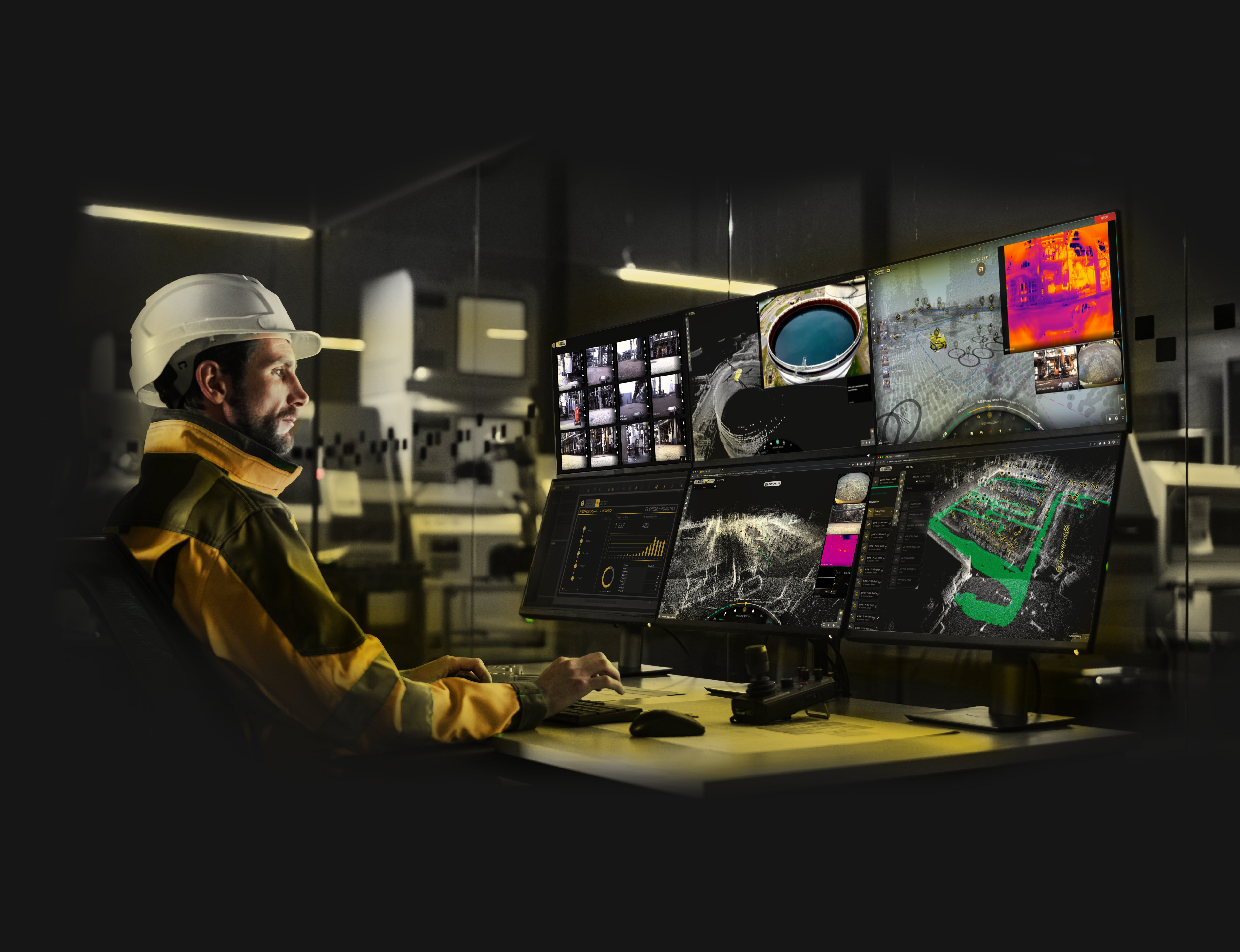
On-demand Inspection Rounds
On-demand Inspection Rounds is an innovative approach to industrial plant inspections that optimizes efficiency and resource allocation. This method deviates from traditional time-based inspection routines by focusing on areas that require immediate attention. In this system, operators conduct rounds based on real-time data and predefined triggers, rather than following a fixed schedule.
The process uses robots and drones to perform automated inspection rounds multiple times every day, collecting high quality data from all relevant assets. When values deviate from normal ranges, alerts are generated, prompting targeted inspections. This allows operators to prioritize critical issues and allocate their time effectively.
Implementing on-demand inspection rounds offers several advantages:
- Minimize Downtime: This approach leverages real-time data and monitoring systems to focus operator attention on potential issues that require immediate intervention, preventing unnecessary disruptions and keeping operations running smoothly with minimal interruptions.
- Eliminates Shutdowns: Unplanned shutdowns can be prevented by identifying and addressing issues before they escalate with the help of timely alerts and AI-driven insights from robots and drones. This approach prioritizes proactive problem-solving rather than reactive measures, leading to increased equipment reliability and continuous production.
- Increased Efficiency: Reduces unnecessary inspections of well-functioning equipment
- Improved Safety: Enables quicker response to potential hazards and increases safety of the personnel by reducing the number of times an operator must physically enter the plant.
- Higher Work Satisfaction: Operators are freed from tiring multiple daily inspection rounds and are called into action only in exceptional situations when the robots have detected an anomaly.
- Cost-effectiveness: Optimizes labor utilization and reduces downtime.
- Enhanced Reliability: Focuses attention on areas that need it most.
- Plugging Workforce Gaps: Onboarding robots for regular daily inspection rounds enables asset owners to plug workforce gaps in the looming demographic crisis.
By adopting this approach, industrial plants can significantly improve their inspection processes, ensuring safer, more efficient operations while maximizing resource utilization.
Enabling On-demand Inspection Rounds
Energy Robotics' end-to-end inspection solution enables asset owners to automate daily inspection rounds through a fleet of different robots and drones. Operators can run automated inspection rounds on-demand using the Energy Robotics user interface and receive real-time insights and alerts from the plant without having to leave the comfort of their control rooms. The data collected by the robots and drones is processed using advanced Artificial Intelligence (AI) applications to deliver insights to the fingertips of operators. Only in the event of an alert is an operator required to perform an on-demand inspection round, taking proactive action to minimize potential downtime and eliminate shutdowns.
By onboarding a fleet of different robots and drones, asset owners can achieve 360°, round-the-clock monitoring of their facilities, from the land and the air, while reducing operational costs and improving worker safety and satisfaction at the same time.